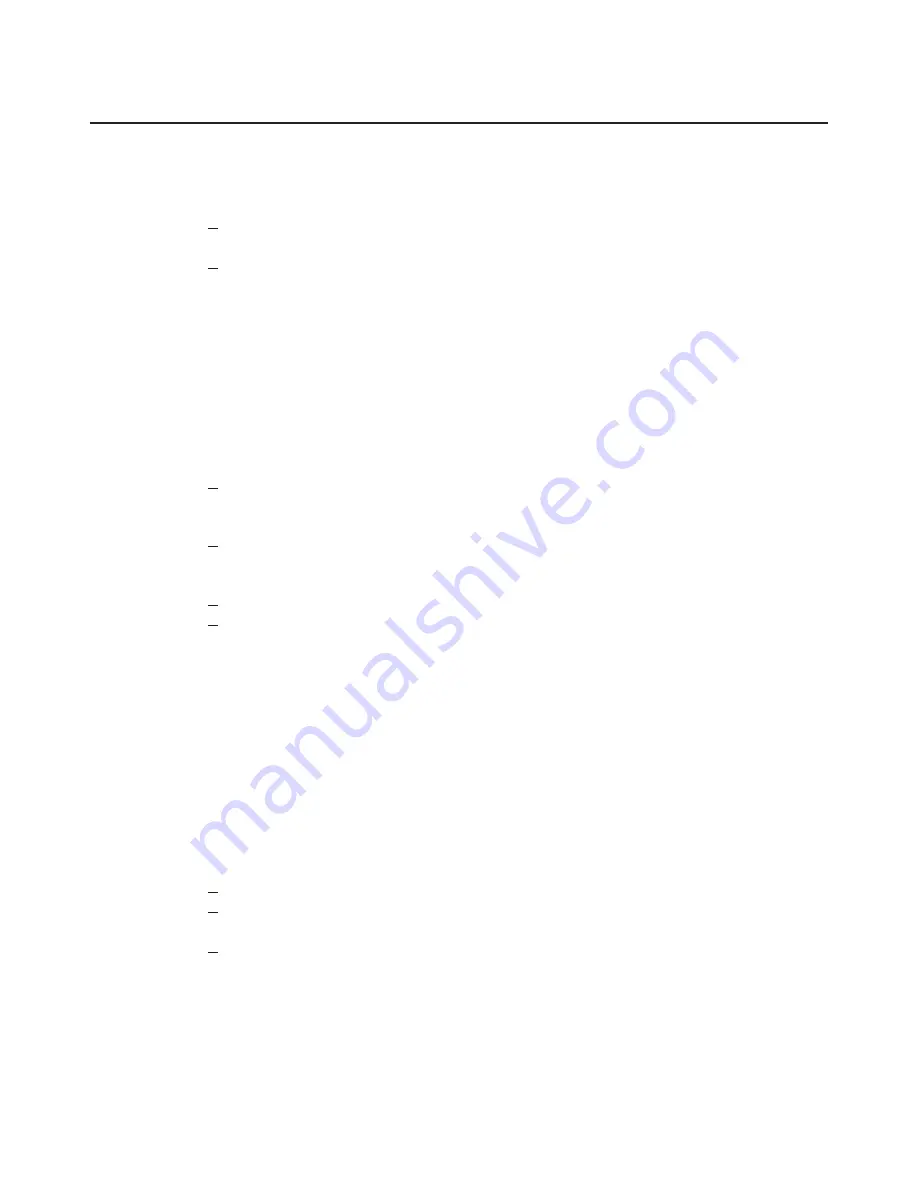
FLAPS (cont.)
(3) Manually Operated Wing Flaps Rigging and Adjustment (cont.)
(c) Adjust flap up stop and step lock
1 Loosen jam nut of
right
torque tube stop screw, located in the floor opening along the
outer end of the flap torque tube.
2 Turn stop screw to obtain approximately 0.60 of an inch between stop fitting and bearing
block measured along top side of screw (refer to Figure 27). It may be necessary to
loosen the adjustment screw of the left stop.
(d) Check cable tension and adjust as required to remove all slack. Do not tighten cable to point
that stop screw comes off stop.
(e) Place a 0.125 of an inch thick spacer between right hand stop screw and stop fitting. With
flaps installed and control rods connected, determine that, when down pressure is applied on
top of the flap, it will not cause the flap to come down. If the flap extends (comes down
under pressure), turn stop screws out a few turns until flap remains in the up-lock position
the spacer inserted. Adjust both stop screws, tighten jam nuts and remove spacer block.
(f) To check up-neutral position of flaps:
1 Place a flap rigging tool as shown in Figure 28 against underside of wing and flap as
close as possible to the outboard end of the flap without contacting any rivets. (Refer to
Chapter 95 for dimensions to fabricate this tool.)
2 Tool must be positioned parallel with wing ribs, with aft end of tool even with trailing
edge of flap.
(g) With flap control rods connected between torque tube crank arm and flaps; check that:
1 Surface of wing contacts tool at its forward surface and at spacer.
2 Aft end of flap contacts aft end of tool. Maintain a light pressure on underside of flap to
remove slack in the linkage while making this check.
(h) Adjust each flap push rod so that chord line of flap forms a zero 1° angle with wing
chord at the outboard end of flap. This is the neutral position.
—NOTE—
To remedy condition of wing heaviness during flight, on PA-
32R-301/301T SP models, adjust flap on side of heavy wing
down from neutral by lengthening the control rod . Check
inspection hole in each rod end to ensure that there are suffi-
cient threads remaining and a wire cannot be inserted through
these holes. Do not raise flap of other wing above neutral. A
wing heavy condition on PA-32R-301 II HP models may be
corrected by ground adjusting trim tab on trailing edge of left
airleron.
(i) Measuring from the neutral position obtained from Steps (f), (g), and (h):
1 Maintain light up pressure on underside of flap.
2 Check flap down travel, which should be 10° ± 2° at first notch, 25° ± 2° at second notch
and 40° ± 2° at the third notch.
3 Adjust the torque tube screw in or out as required. After any adjustment of screw it will
be necessary to review steps (c) thru (i).
(j) Check complete operation of the flaps, flap control handle and ratchet mechanism.
(k) Install all access covers removed.
PIPER AIRCRAFT
PA-32R-301/301T
MAINTENANCE MANUAL
27-50-00
Page 27-51
Reissued: July 1, 1993
2D1
Summary of Contents for PA-32R-301T SARATOGA S
Page 26: ...CHAPTER 4 AIRWORTHINESS LIMITATIONS 1C1 ...
Page 29: ...CHAPTER 5 TIME LIMITS MAINTENANCE CHECKS 1C4 ...
Page 53: ...CHAPTER 6 DIMENSIONS AND AREAS 1D6 ...
Page 64: ...CHAPTER 7 LIFTING AND SHORING 1D21 ...
Page 68: ...CHAPTER 8 LEVELING AND WEIGHING 1E1 ...
Page 72: ...CHAPTER 9 TOWING AND TAXIING 1E5 ...
Page 76: ...CHAPTER 10 PARKING AND MOORING 1E9 ...
Page 80: ...CHAPTER 11 REQUIRED PLACARDS 1E13 ...
Page 92: ...CHAPTER 12 SERVICING 1F1 ...
Page 126: ...CHAPTER 20 STANDARD PRACTICES AIRFRAME 1G17 ...
Page 127: ...THIS PAGE INTENTIONALLY LEFT BLANK ...
Page 139: ...CHAPTER 21 ENVIRONMENTAL SYSTEMS 1H5 ...
Page 188: ...CHAPTER 22 AUTOFLIGHT 1J7 ...
Page 193: ...CHAPTER 23 COMMUNICATIONS 1J12 ...
Page 203: ...CHAPTER 24 ELECTRICAL POWER 1J22 ...
Page 263: ...CHAPTER 25 EQUIPMENT FURNISHINGS 2A13 ...
Page 269: ...CHAPTER 27 FLIGHT CONTROLS 2A20 ...
Page 332: ...CHAPTER 28 FUEL 2D11 ...
Page 363: ...CHAPTER 29 HYDRAULIC POWER 2E18 ...
Page 404: ...CHAPTER 30 ICE AND RAIN PROTECTION 2G16 ...
Page 470: ...CHAPTER 32 LANDING GEAR 3A13 ...
Page 550: ...CHAPTER 33 LIGHTS 3D24 ...
Page 562: ...CHAPTER 34 NAVIGATION AND PITOT STATIC 3E12 ...
Page 582: ...CHAPTER 35 OXYGEN 3F8 ...
Page 604: ...CHAPTER 37 VACUUM 3G6 ...
Page 616: ...CHAPTER 39 3G18 ELECTRIC ELECTRONIC PANELS MULTIPURPOSE PARTS ...
Page 620: ...CHAPTER 51 STRUCTURES 3G22 ...
Page 636: ...CHAPTER 52 DOORS 3H14 ...
Page 650: ...CHAPTER 55 STABILIZERS 3I4 ...
Page 662: ...CHAPTER 56 WINDOWS 3I16 ...
Page 670: ...CHAPTER 57 WINGS 3I24 ...
Page 688: ...CHAPTER 61 PROPELLER 3J18 ...
Page 704: ...CHAPTER 70 STANDARD PRACTICES ENGINES 3K10 ...
Page 708: ...CHAPTER 71 POWER PLANT 3K14 ...
Page 737: ...CHAPTER 73 ENGINE FUEL SYSTEM 4A13 ...
Page 749: ...CHAPTER 74 IGNITION 4B1 ...
Page 783: ...CHAPTER 77 ENGINE INDICATING 4C11 ...
Page 793: ...CHAPTER 78 EXHAUST 4C21 ...
Page 801: ...CHAPTER 79 OIL 4D5 ...
Page 805: ...CHAPTER 80 STARTING 4D9 ...
Page 819: ...CHAPTER 81 TURBINES 4D23 ...
Page 833: ...CHAPTER 91 CHARTS WIRING DIAGRAMS 4E13 ...