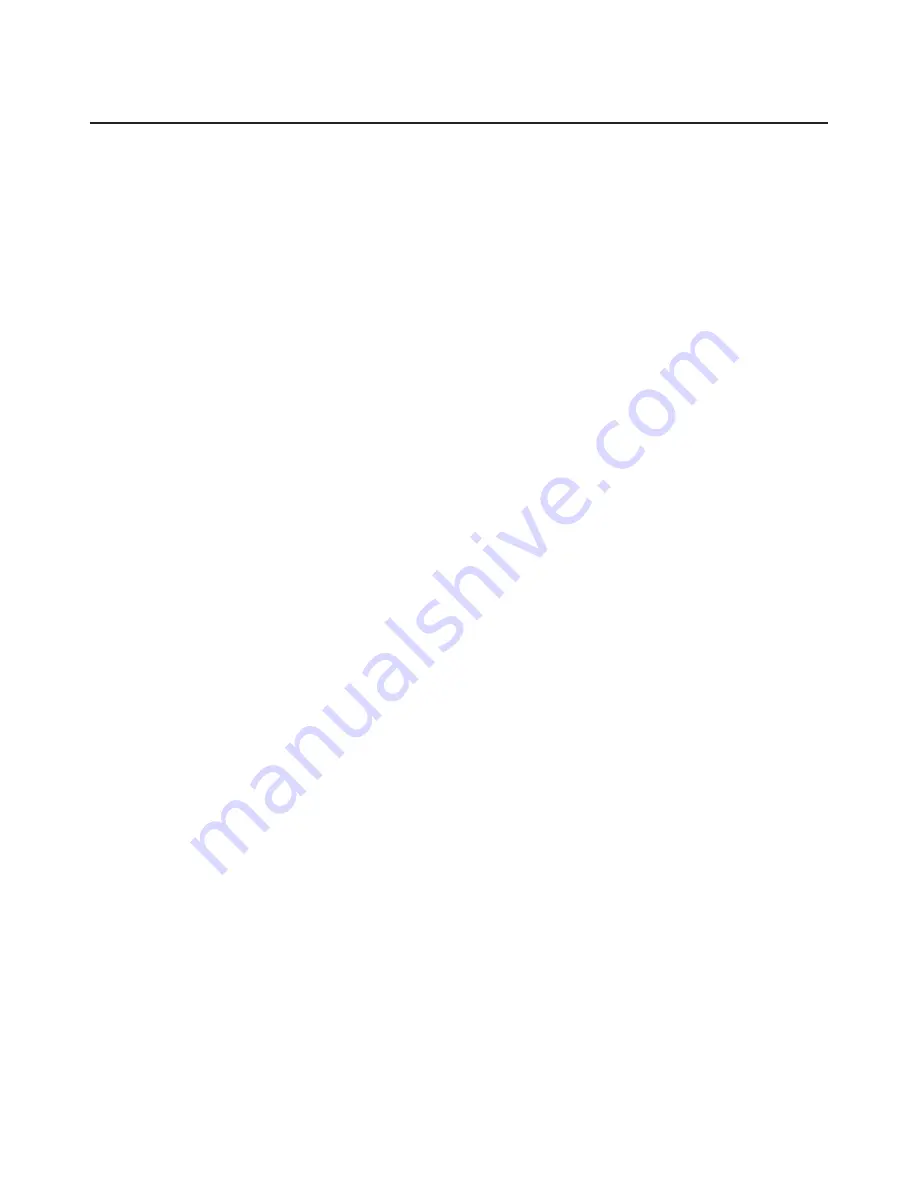
ICE AND RAIN PROTECTION (Cont.)
B. Description and Operation (cont.)
Propeller deice system, which can be installed by itself or included in a package with others of ice
protection system, is designed for both two- and three-bladed propeller installations. Each propeller
deice system consists of an electrically heated deicer bonded to each propeller blade, slip ring assembly
with brush block assembly to transfer electrical power to rotating deicers, a timer, an ammeter, a control
switch-circuit breaker, shunt, together with wiring harnesses to complete circuit. Power is drawn from
aircraft electrical system.
To conserve electrical power current is cycled to deicer heaters at timed intervals rather than
continuously. Each has two separate heaters; one for outer half and one for inner half. By heating all
outer or inner heaters, rotational balance is held during deicing. Current is drawn from airplane
electrical system through switch, ammeter and timer. Timer successively delivers current via slip ring
and brush block arrangement to (Phase 1) outer heaters on propeller and then inner heaters on propeller.
Timer energizes each of these phases in turn for about 30 seconds and then repeats cycle as long as
inflight if needed.
– NOTE –
Heating may begin at any phase in cycle depending on timer
position when switch was turned off from previous use.
Deicers contain special heater wires protected by fabric plies and by oil and abrasion-resistant rubber.
Side of deicer cemented to propeller has a dull finish whereas air side finish is glossy. Each deicer has
separate lead for inboard and a third lead which is a common ground. These leads are so marked. An
unmarked ground can be identified by using an ohmmeter across three possible pairs of leads. One pair
will show twice resistance of other pairs. Latter are hot leads and lead excluded from pair that shows
twice resistance of other pairs is ground lead.
To transfer electrical power to rotating deicer, a brush block assembly is mounted to engine or similar
stationary member and has brushes which are spring loaded to press against revolving slip rings. Slip
ring assembly is provided as a slip ring gear assembly which replaces original starter ring gear of
engine.
Timer is a sealed unit. If found inoperative, it must be replaced as an assembly - no field repairs are
authorized.
Ammeter is designed for each particular system and it is therefore important that correct replacement
part number be used if replacement should be required. In event of low aircraft battery voltage (very
possible in ground check), ammeter reading will be lower than at full voltage. Provided ammeter
needle reads in shaded range on scale, (full aircraft voltage) current flow is considered as normal.
A heated windshield panel can also be installed as a separate item or with any combination of systems.
Installation is controlled by a circuit breaker/switch on control panel along with use of a glass panel
imbedded with wire filaments. Panel is mounted to a metal frame and secured by two screws to
fuselage, just outside of windshield on pilot’s side. Frame is hinged at its base to facilitate cleaning of
windshield and panel. When not in use, panel can be removed by removing two attaching screws and
harness from fuselage.
PIPER AIRCRAFT
PA-32R-301/301T
MAINTENANCE MANUAL
30-00-00
Page 30-2
Reissued: July 1, 1993
2G20
Summary of Contents for PA-32R-301T SARATOGA S
Page 26: ...CHAPTER 4 AIRWORTHINESS LIMITATIONS 1C1 ...
Page 29: ...CHAPTER 5 TIME LIMITS MAINTENANCE CHECKS 1C4 ...
Page 53: ...CHAPTER 6 DIMENSIONS AND AREAS 1D6 ...
Page 64: ...CHAPTER 7 LIFTING AND SHORING 1D21 ...
Page 68: ...CHAPTER 8 LEVELING AND WEIGHING 1E1 ...
Page 72: ...CHAPTER 9 TOWING AND TAXIING 1E5 ...
Page 76: ...CHAPTER 10 PARKING AND MOORING 1E9 ...
Page 80: ...CHAPTER 11 REQUIRED PLACARDS 1E13 ...
Page 92: ...CHAPTER 12 SERVICING 1F1 ...
Page 126: ...CHAPTER 20 STANDARD PRACTICES AIRFRAME 1G17 ...
Page 127: ...THIS PAGE INTENTIONALLY LEFT BLANK ...
Page 139: ...CHAPTER 21 ENVIRONMENTAL SYSTEMS 1H5 ...
Page 188: ...CHAPTER 22 AUTOFLIGHT 1J7 ...
Page 193: ...CHAPTER 23 COMMUNICATIONS 1J12 ...
Page 203: ...CHAPTER 24 ELECTRICAL POWER 1J22 ...
Page 263: ...CHAPTER 25 EQUIPMENT FURNISHINGS 2A13 ...
Page 269: ...CHAPTER 27 FLIGHT CONTROLS 2A20 ...
Page 332: ...CHAPTER 28 FUEL 2D11 ...
Page 363: ...CHAPTER 29 HYDRAULIC POWER 2E18 ...
Page 404: ...CHAPTER 30 ICE AND RAIN PROTECTION 2G16 ...
Page 470: ...CHAPTER 32 LANDING GEAR 3A13 ...
Page 550: ...CHAPTER 33 LIGHTS 3D24 ...
Page 562: ...CHAPTER 34 NAVIGATION AND PITOT STATIC 3E12 ...
Page 582: ...CHAPTER 35 OXYGEN 3F8 ...
Page 604: ...CHAPTER 37 VACUUM 3G6 ...
Page 616: ...CHAPTER 39 3G18 ELECTRIC ELECTRONIC PANELS MULTIPURPOSE PARTS ...
Page 620: ...CHAPTER 51 STRUCTURES 3G22 ...
Page 636: ...CHAPTER 52 DOORS 3H14 ...
Page 650: ...CHAPTER 55 STABILIZERS 3I4 ...
Page 662: ...CHAPTER 56 WINDOWS 3I16 ...
Page 670: ...CHAPTER 57 WINGS 3I24 ...
Page 688: ...CHAPTER 61 PROPELLER 3J18 ...
Page 704: ...CHAPTER 70 STANDARD PRACTICES ENGINES 3K10 ...
Page 708: ...CHAPTER 71 POWER PLANT 3K14 ...
Page 737: ...CHAPTER 73 ENGINE FUEL SYSTEM 4A13 ...
Page 749: ...CHAPTER 74 IGNITION 4B1 ...
Page 783: ...CHAPTER 77 ENGINE INDICATING 4C11 ...
Page 793: ...CHAPTER 78 EXHAUST 4C21 ...
Page 801: ...CHAPTER 79 OIL 4D5 ...
Page 805: ...CHAPTER 80 STARTING 4D9 ...
Page 819: ...CHAPTER 81 TURBINES 4D23 ...
Page 833: ...CHAPTER 91 CHARTS WIRING DIAGRAMS 4E13 ...