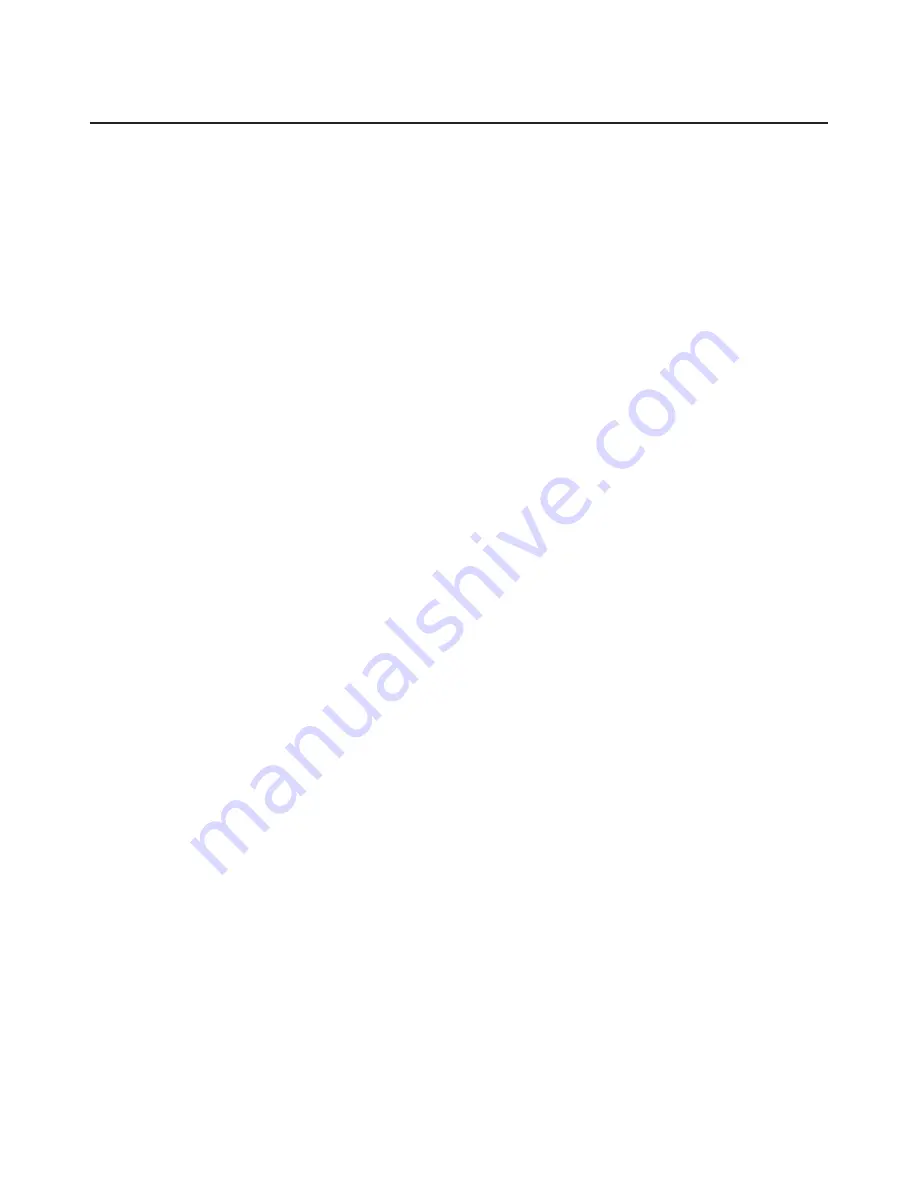
FLIGHT CONTROLS
A. General Information
(1) Description and Operation.
The airplane is controlled in flight by the use of three primary control surfaces: ailerons, stabilator
and rudder. The controls are operated by movement of the control column-tee bar assembly and
rudder pedals. On the forward end of each control column is a sprocket assembly. A chain is
wrapped around the sprockets to connect the right and left controls and then back to idler sprock-
ets on the column’s tee bar, which connect to the aileron primary control cables. The cables oper-
ate the aileron bellcrank and push-pull rods. The stabilator is controlled by a cable connected to
the bottom of the tee bar assembly and operates an aft fuselage bellcrank which controls a push
rod connected to the balance arm of the stabilator. Cables also connect the rudder pedals with the
rudder horn. Provisions for directional and longitudinal trim control is provided by an adjustable
trim mechanism for the stabilator and rudder. The stabilator trim is controlled by a wheel and
drum mounted on the floor tunnel between the front seats. Cables routed aft from the drum to a
screw assembly mounted above the stabilator attachment point. This screw assembly in turn
moves the push rod which controls the stabilator trim tab. The rudder trim is controlled by a knob
and screw assembly attached to the rudder pedal assembly. The flaps are mechanically operated
on early models and electrically operated on 1985 and later models.
(2) Standard Practices and Procedures
The following tips may be helpful in the removal, installation, and rigging of individual control
system assemblies.
(a) Turnbuckles must be assembled and adjusted in a manner that each terminal end is screwed
into the barrel an approximately equal distance. During adjustment, the terminals must not be
turned in a manner which would put a permanent twist in the cable.
(b) After adjustment is completed, each turnbuckle must be checked. Not more than three
terminal threads shall be visible outside the barrel. Locking clips must be installed and
checked for proper installation by trying to remove the clips using fingers only. Locking clips
which have been installed and removed must be scrapped and new clips used.
(c) Torque all nuts in the flight control surface rigging system in accordance with AC 43.13-1A
or to torques specified within this manual.
(d) After completion of adjustment, each jam nut must be tightened securely and inspected.
(e) On push rods or rod ends provided with an inspection hole, screws must be screwed in
sufficiently far to pass the hole. This can be determined visually or, by feel, by inserting a
piece of wire into the inspection hole. If no inspection hole is provided, a minimum of 0.375
of an inch thread engagement must be maintained.
(f) All cable rigging tensions given must be corrected to ambient temperature in the area where
the tension is being checked. Refer to Chart 1.
(g) See Figure 1 for proper method of adjusting rod ends to prevent possible damage and binding
of bearing surface in rod end.
(h) All pulley guard pins should be properly installed.
PIPER AIRCRAFT
PA-32R-301/301T
MAINTENANCE MANUAL
27-00-00
Page 27-1
Reissued: July 1, 1993
2A23
Summary of Contents for PA-32R-301T SARATOGA S
Page 26: ...CHAPTER 4 AIRWORTHINESS LIMITATIONS 1C1 ...
Page 29: ...CHAPTER 5 TIME LIMITS MAINTENANCE CHECKS 1C4 ...
Page 53: ...CHAPTER 6 DIMENSIONS AND AREAS 1D6 ...
Page 64: ...CHAPTER 7 LIFTING AND SHORING 1D21 ...
Page 68: ...CHAPTER 8 LEVELING AND WEIGHING 1E1 ...
Page 72: ...CHAPTER 9 TOWING AND TAXIING 1E5 ...
Page 76: ...CHAPTER 10 PARKING AND MOORING 1E9 ...
Page 80: ...CHAPTER 11 REQUIRED PLACARDS 1E13 ...
Page 92: ...CHAPTER 12 SERVICING 1F1 ...
Page 126: ...CHAPTER 20 STANDARD PRACTICES AIRFRAME 1G17 ...
Page 127: ...THIS PAGE INTENTIONALLY LEFT BLANK ...
Page 139: ...CHAPTER 21 ENVIRONMENTAL SYSTEMS 1H5 ...
Page 188: ...CHAPTER 22 AUTOFLIGHT 1J7 ...
Page 193: ...CHAPTER 23 COMMUNICATIONS 1J12 ...
Page 203: ...CHAPTER 24 ELECTRICAL POWER 1J22 ...
Page 263: ...CHAPTER 25 EQUIPMENT FURNISHINGS 2A13 ...
Page 269: ...CHAPTER 27 FLIGHT CONTROLS 2A20 ...
Page 332: ...CHAPTER 28 FUEL 2D11 ...
Page 363: ...CHAPTER 29 HYDRAULIC POWER 2E18 ...
Page 404: ...CHAPTER 30 ICE AND RAIN PROTECTION 2G16 ...
Page 470: ...CHAPTER 32 LANDING GEAR 3A13 ...
Page 550: ...CHAPTER 33 LIGHTS 3D24 ...
Page 562: ...CHAPTER 34 NAVIGATION AND PITOT STATIC 3E12 ...
Page 582: ...CHAPTER 35 OXYGEN 3F8 ...
Page 604: ...CHAPTER 37 VACUUM 3G6 ...
Page 616: ...CHAPTER 39 3G18 ELECTRIC ELECTRONIC PANELS MULTIPURPOSE PARTS ...
Page 620: ...CHAPTER 51 STRUCTURES 3G22 ...
Page 636: ...CHAPTER 52 DOORS 3H14 ...
Page 650: ...CHAPTER 55 STABILIZERS 3I4 ...
Page 662: ...CHAPTER 56 WINDOWS 3I16 ...
Page 670: ...CHAPTER 57 WINGS 3I24 ...
Page 688: ...CHAPTER 61 PROPELLER 3J18 ...
Page 704: ...CHAPTER 70 STANDARD PRACTICES ENGINES 3K10 ...
Page 708: ...CHAPTER 71 POWER PLANT 3K14 ...
Page 737: ...CHAPTER 73 ENGINE FUEL SYSTEM 4A13 ...
Page 749: ...CHAPTER 74 IGNITION 4B1 ...
Page 783: ...CHAPTER 77 ENGINE INDICATING 4C11 ...
Page 793: ...CHAPTER 78 EXHAUST 4C21 ...
Page 801: ...CHAPTER 79 OIL 4D5 ...
Page 805: ...CHAPTER 80 STARTING 4D9 ...
Page 819: ...CHAPTER 81 TURBINES 4D23 ...
Page 833: ...CHAPTER 91 CHARTS WIRING DIAGRAMS 4E13 ...