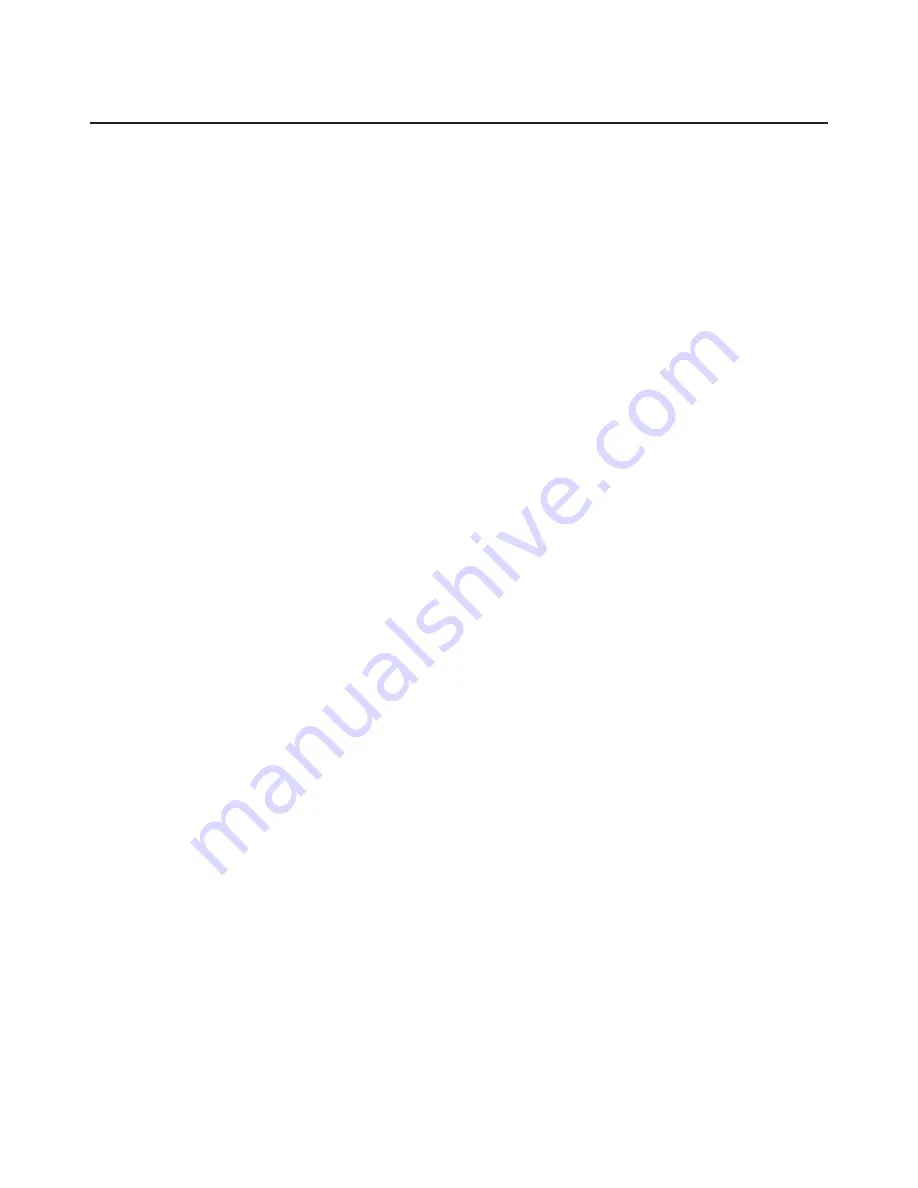
STRUCTURAL REPAIRS (Cont.)
FIBERGLASS TOUCH-UP AND SURFACE REPAIRS
1. Remove wax, oil and dirt from around damaged area with acetone, Methylethylketone or equivalent
and remove paint to gel coat.
2. Damaged area may be scraped with a fine blade knife or a power drill with a burr attachment to roughen
bottom and sides of damaged area. Feather edge surrounding scratch or cavity. Do not undercut edge.
(If scratch or cavity is shallow and penetrates only surface coat, continue to step 8.)
3. Pour a small amount of resin into a jar lid or on a piece of cardboard, just enough to fill area being
worked on. Mix an equal amount of milled fiberglas with resin, using a putty knife or stick. Add
catalyst, according to kit instruction, to resin and mix thoroughly. A hypodermic needle may be used
to inject gel into small cavities not requiring fiberglas millings mixed with gel.
4. Work mixture of resin, fibers and catalyst into damaged area, using sharp point of a putty knife or stick
to press it into bottom of hold and to puncture any air bubbles which may be present. Fill scratch or
hole above surrounding undamaged area about 1/16 inch.
5. Lay piece of cellophane or waxed paper over repair to cut off air and start cure of gel mixture.
6. Allow gel to cure 10 to 15 minutes until it feels rubbery to touch. Remove cellophane and trim flush
with surface, using a sharp razor blade or knife. Replace cellophane and allow to cure completely for
30 minutes to an hour. Patch will shrink slightly below structure surface as it cures. (If wax paper is
used, ascertain wax is removed from surface.)
7. Rough up bottom and edges of hole with electric burr attachment or rough sandpaper. Feather hole into
surrounding gel coat, do not undercut.
8. Pour out a small amount of resin, add catalyst and mix thoroughly, using a cutting motion rather than
stirring. Use no fibers.
9. Using tip of putty knife or fingertips, fill hole to about 1/16 inch above surrounding surface with gel
coat mixture.
ly cured.
11. After trimming patch, immediately place another small amount of gel coat on cut edge of patch and
cover with cellophane. Then, using a squeegee or back of a razor blade, squeegee level with area sur-
rounding patch, leave cellophane on patch for one or two hours or overnight, for complete cure.
12. After repair has cured for 24 hours, sand patched area using sanding block with fine wet sand- paper.
Finish by priming, again sanding and applying color coat.
FIBERBLASS FRACTURE AND PATCH REPAIRS
1. Remove wax, oil and dirt from around damaged area with acetone, methylethyketone or equivalent.
2. Using a key hole saw, electric saber saw, or sharp knife cut away ragged edges. Cut back to sound
material.
3. Remove paint three inches back from around damaged area.
4. Working inside structure, bevel edges to approximately a 30 degree angle and rough-sand hole and
area around it, using 80-grit dry paper. Feather back for about two inches all around hole. This roughens
surface for strong bond with patch.
PIPER AIRCRAFT
PA-32R-301/301T
MAINTENANCE MANUAL
51-00-00
Page 51-4
Reissued: July 1, 1993
3H3
Summary of Contents for PA-32R-301T SARATOGA S
Page 26: ...CHAPTER 4 AIRWORTHINESS LIMITATIONS 1C1 ...
Page 29: ...CHAPTER 5 TIME LIMITS MAINTENANCE CHECKS 1C4 ...
Page 53: ...CHAPTER 6 DIMENSIONS AND AREAS 1D6 ...
Page 64: ...CHAPTER 7 LIFTING AND SHORING 1D21 ...
Page 68: ...CHAPTER 8 LEVELING AND WEIGHING 1E1 ...
Page 72: ...CHAPTER 9 TOWING AND TAXIING 1E5 ...
Page 76: ...CHAPTER 10 PARKING AND MOORING 1E9 ...
Page 80: ...CHAPTER 11 REQUIRED PLACARDS 1E13 ...
Page 92: ...CHAPTER 12 SERVICING 1F1 ...
Page 126: ...CHAPTER 20 STANDARD PRACTICES AIRFRAME 1G17 ...
Page 127: ...THIS PAGE INTENTIONALLY LEFT BLANK ...
Page 139: ...CHAPTER 21 ENVIRONMENTAL SYSTEMS 1H5 ...
Page 188: ...CHAPTER 22 AUTOFLIGHT 1J7 ...
Page 193: ...CHAPTER 23 COMMUNICATIONS 1J12 ...
Page 203: ...CHAPTER 24 ELECTRICAL POWER 1J22 ...
Page 263: ...CHAPTER 25 EQUIPMENT FURNISHINGS 2A13 ...
Page 269: ...CHAPTER 27 FLIGHT CONTROLS 2A20 ...
Page 332: ...CHAPTER 28 FUEL 2D11 ...
Page 363: ...CHAPTER 29 HYDRAULIC POWER 2E18 ...
Page 404: ...CHAPTER 30 ICE AND RAIN PROTECTION 2G16 ...
Page 470: ...CHAPTER 32 LANDING GEAR 3A13 ...
Page 550: ...CHAPTER 33 LIGHTS 3D24 ...
Page 562: ...CHAPTER 34 NAVIGATION AND PITOT STATIC 3E12 ...
Page 582: ...CHAPTER 35 OXYGEN 3F8 ...
Page 604: ...CHAPTER 37 VACUUM 3G6 ...
Page 616: ...CHAPTER 39 3G18 ELECTRIC ELECTRONIC PANELS MULTIPURPOSE PARTS ...
Page 620: ...CHAPTER 51 STRUCTURES 3G22 ...
Page 636: ...CHAPTER 52 DOORS 3H14 ...
Page 650: ...CHAPTER 55 STABILIZERS 3I4 ...
Page 662: ...CHAPTER 56 WINDOWS 3I16 ...
Page 670: ...CHAPTER 57 WINGS 3I24 ...
Page 688: ...CHAPTER 61 PROPELLER 3J18 ...
Page 704: ...CHAPTER 70 STANDARD PRACTICES ENGINES 3K10 ...
Page 708: ...CHAPTER 71 POWER PLANT 3K14 ...
Page 737: ...CHAPTER 73 ENGINE FUEL SYSTEM 4A13 ...
Page 749: ...CHAPTER 74 IGNITION 4B1 ...
Page 783: ...CHAPTER 77 ENGINE INDICATING 4C11 ...
Page 793: ...CHAPTER 78 EXHAUST 4C21 ...
Page 801: ...CHAPTER 79 OIL 4D5 ...
Page 805: ...CHAPTER 80 STARTING 4D9 ...
Page 819: ...CHAPTER 81 TURBINES 4D23 ...
Page 833: ...CHAPTER 91 CHARTS WIRING DIAGRAMS 4E13 ...