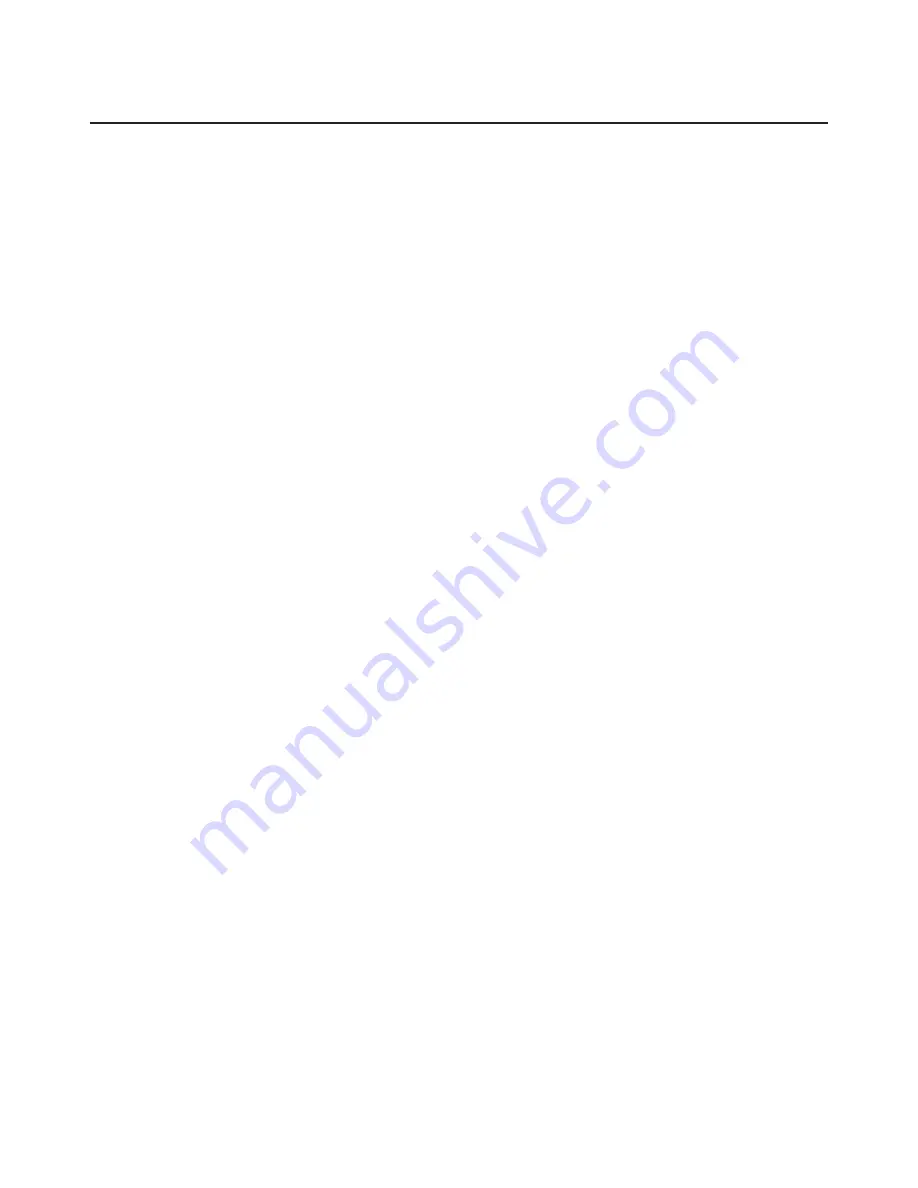
ELECTRICAL POWER SUPPLY.
MAGNETO.
INSPECTION OF MAGNETO.
After the first 50 hour period and every 100 hours thereafter, the magneto ignition system should be
checked. If engine operating troubles develop which appear to be caused by the ignition system, it is advis-
able to check the spark plugs and wiring first before working on the magneto. Should trouble appear defi-
nitely associated with magneto, the most effective measure is to install a replacement magneto which is
known to be in satisfactory condition and send the suspected unit to the overhaul shop for test and repair.
Should this not be possible, a visual inspection of the following items may disclose the source of trouble.
1. Check the lead terminals for definite contact with spring contacts in outlets.
2. Remove the harness outlet cover from the magneto and inspect for the presence of moisture and car-
bon tracking due to moisture.
3. Check contact springs in distributor block for evidence of spark erosion.
4. Check height of contacts springs (0.422 maximum from top of block tower to spring). (Refer to
5. With the cover and harness separated from the magneto housing, check contact assemblies to see that
cam follower is securely riveted to its spring.
6. Examine the contact points for excessive wear or burning. Figure 1 shows how the average contact
point will look when surfaces are separated for inspection.
– CAUTION –
Do not open point contacts more than .0625 of an inch for
examination of contact surfaces. Excessive spreading of the
breaker points will overstress and damage the contact spring.
Desired contact surfaces have a dull gray, sand-blasted (almost rough) or frosted appearance over the area
where electrical contact is made. This means that points are worn in and mated to each other, thereby pro-
viding the best possible electrical contact and highest efficiency of performance. Minor irregularities or
roughness of point surfaces are not harmful. ( Refer to Figure 1, center.) Neither are small pits or mounds,
if not too pronounced. If there is a possibility of pit becoming deep enough to penetrate pad (refer to
Figure 1, right), reject contact assembly.
– NOTE –
No attempt should be made to stone or dress contact point.
Should contact assembly have bad points or show excessive
wear, the complete contact assembly should be replaced.
7. Check condition of cam follower felts for proper lubrication. If oil has migrated from one follower felt
to another, it may be necessary to remove the lubrication from one felt strip while oiling another. If felt
is overlubricated, remove oil by using a clean, lintless cloth. If dry, apply one or two drops of Bendix
Breaker Felt Lubricant 10-86527.
PIPER AIRCRAFT
PA-32R-301/301T
MAINTENANCE MANUAL
74-10-00
Page 74-3
Reissued: July 1, 1993
4B5
Summary of Contents for PA-32R-301T SARATOGA S
Page 26: ...CHAPTER 4 AIRWORTHINESS LIMITATIONS 1C1 ...
Page 29: ...CHAPTER 5 TIME LIMITS MAINTENANCE CHECKS 1C4 ...
Page 53: ...CHAPTER 6 DIMENSIONS AND AREAS 1D6 ...
Page 64: ...CHAPTER 7 LIFTING AND SHORING 1D21 ...
Page 68: ...CHAPTER 8 LEVELING AND WEIGHING 1E1 ...
Page 72: ...CHAPTER 9 TOWING AND TAXIING 1E5 ...
Page 76: ...CHAPTER 10 PARKING AND MOORING 1E9 ...
Page 80: ...CHAPTER 11 REQUIRED PLACARDS 1E13 ...
Page 92: ...CHAPTER 12 SERVICING 1F1 ...
Page 126: ...CHAPTER 20 STANDARD PRACTICES AIRFRAME 1G17 ...
Page 127: ...THIS PAGE INTENTIONALLY LEFT BLANK ...
Page 139: ...CHAPTER 21 ENVIRONMENTAL SYSTEMS 1H5 ...
Page 188: ...CHAPTER 22 AUTOFLIGHT 1J7 ...
Page 193: ...CHAPTER 23 COMMUNICATIONS 1J12 ...
Page 203: ...CHAPTER 24 ELECTRICAL POWER 1J22 ...
Page 263: ...CHAPTER 25 EQUIPMENT FURNISHINGS 2A13 ...
Page 269: ...CHAPTER 27 FLIGHT CONTROLS 2A20 ...
Page 332: ...CHAPTER 28 FUEL 2D11 ...
Page 363: ...CHAPTER 29 HYDRAULIC POWER 2E18 ...
Page 404: ...CHAPTER 30 ICE AND RAIN PROTECTION 2G16 ...
Page 470: ...CHAPTER 32 LANDING GEAR 3A13 ...
Page 550: ...CHAPTER 33 LIGHTS 3D24 ...
Page 562: ...CHAPTER 34 NAVIGATION AND PITOT STATIC 3E12 ...
Page 582: ...CHAPTER 35 OXYGEN 3F8 ...
Page 604: ...CHAPTER 37 VACUUM 3G6 ...
Page 616: ...CHAPTER 39 3G18 ELECTRIC ELECTRONIC PANELS MULTIPURPOSE PARTS ...
Page 620: ...CHAPTER 51 STRUCTURES 3G22 ...
Page 636: ...CHAPTER 52 DOORS 3H14 ...
Page 650: ...CHAPTER 55 STABILIZERS 3I4 ...
Page 662: ...CHAPTER 56 WINDOWS 3I16 ...
Page 670: ...CHAPTER 57 WINGS 3I24 ...
Page 688: ...CHAPTER 61 PROPELLER 3J18 ...
Page 704: ...CHAPTER 70 STANDARD PRACTICES ENGINES 3K10 ...
Page 708: ...CHAPTER 71 POWER PLANT 3K14 ...
Page 737: ...CHAPTER 73 ENGINE FUEL SYSTEM 4A13 ...
Page 749: ...CHAPTER 74 IGNITION 4B1 ...
Page 783: ...CHAPTER 77 ENGINE INDICATING 4C11 ...
Page 793: ...CHAPTER 78 EXHAUST 4C21 ...
Page 801: ...CHAPTER 79 OIL 4D5 ...
Page 805: ...CHAPTER 80 STARTING 4D9 ...
Page 819: ...CHAPTER 81 TURBINES 4D23 ...
Page 833: ...CHAPTER 91 CHARTS WIRING DIAGRAMS 4E13 ...