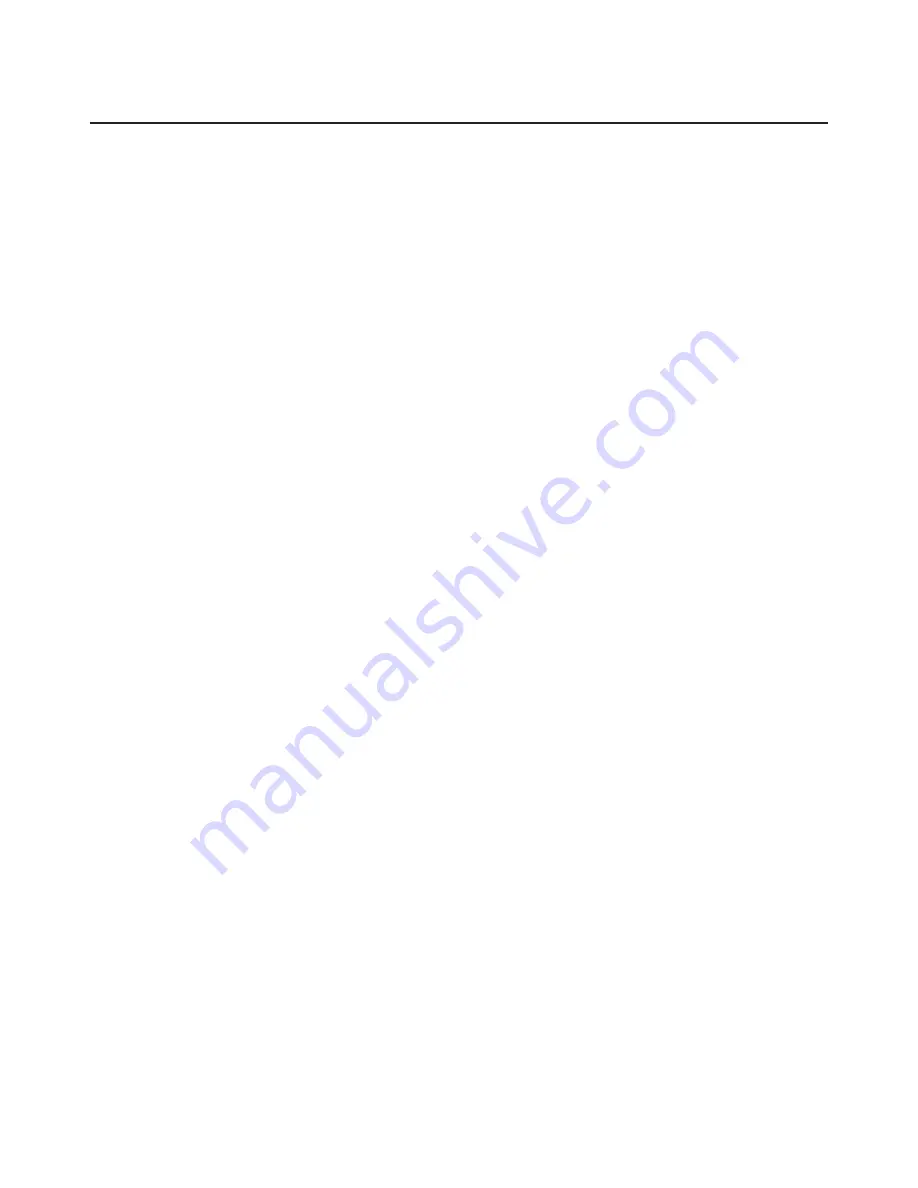
DISASSEMBLY OF STARTING MOTOR.
1. Remove the frame screws from the commutator end head and pull end head and armature from frame.
Lift the brushes and lock in elevated position with brush springs. Use a puller to remove the end head
from the armature. Use special bearing puller to remove the sealed ball bearing from the armature
shaft.
2. Remove the frame screws that secure the gear housing to the frame. Remove bolts and nuts holding
the gear housing to the pinion housing and separate the two units. Pull Bendix shaft from pinion hous-
ing. Do not lose the steel spacer that is located on the pinion end of the shaft. Remove reduction gear,
woodruff key and steel spacer from shaft.
3. Turn the Bendix pinion until it locks in the extended position. Locate "spiral" pin and use a punch to
remove. Slide drive assembly off the shaft. Do not attempt to disassemble the drive and do not dip it in
cleaning solvent.
4. To remove the roller bearings from the gear housing, use an arbor press and the correct bearing arbor.
DO NOT HAMMER OUT. Each part should be cleaned and inspected for excessive wear or damage.
Bearings should be checked for proper clearance and evidence of roughness or galling. Oil and dirt
should be removed from insulation and the condition of the insulation checked.
BRUSHES.
Check the brushes to see that they slide freely in their holders and make full contact on the commutator. If
worn to half their original length or less, they should be replaced.
ARMATURE.
1. Check the commutator for uneven wear, excessive glazing or evidence of excessive arcing. If only
slightly dirty, glazed or discolored, the commutator can be cleaned with 00 or 000 sandpaper. If the
commutator is rough or worn, it should be turned in a lathe. (Refer to Figure 2.) The armature shaft
should be inspected for rough bearing surfaces and rough or damaged splines.
2. To test the armature for grounds, a set of test probes connected in series with a 110-volt light should
be used. Touch one probe to a commutator segment and the other to the armature core. If the test lamp
lights, the armature is grounded and should be replaced.
growler and slowly rotated by hand while a steel strip is held over the core so that it passes over each
armature core slot. If a coil is shorted, the steel strip will vibrate.
4. A quick check for opens can be made by inspecting the trailing edge (in direction of rotation) of the
commutator segments for excessive discoloration. This condition indicates an open circuit.
FIELD COILS.
1. Check the field coils for grounds (refer to Figure 4) by placing one test probe on the frame and the
other on the starter terminal. Be sure the brushes are not accidentally touching the frame. If the lamp
lights, the fields are grounded. Repair or replace.
2. Inspect all connections to make sure they are clean and tight and inspect insulation for deterioration.
PIPER AIRCRAFT
PA-32R-301/301T
MAINTENANCE MANUAL
80-10-00
Page 80-6
Reissued: July 1, 1993
4D16
Summary of Contents for PA-32R-301T SARATOGA S
Page 26: ...CHAPTER 4 AIRWORTHINESS LIMITATIONS 1C1 ...
Page 29: ...CHAPTER 5 TIME LIMITS MAINTENANCE CHECKS 1C4 ...
Page 53: ...CHAPTER 6 DIMENSIONS AND AREAS 1D6 ...
Page 64: ...CHAPTER 7 LIFTING AND SHORING 1D21 ...
Page 68: ...CHAPTER 8 LEVELING AND WEIGHING 1E1 ...
Page 72: ...CHAPTER 9 TOWING AND TAXIING 1E5 ...
Page 76: ...CHAPTER 10 PARKING AND MOORING 1E9 ...
Page 80: ...CHAPTER 11 REQUIRED PLACARDS 1E13 ...
Page 92: ...CHAPTER 12 SERVICING 1F1 ...
Page 126: ...CHAPTER 20 STANDARD PRACTICES AIRFRAME 1G17 ...
Page 127: ...THIS PAGE INTENTIONALLY LEFT BLANK ...
Page 139: ...CHAPTER 21 ENVIRONMENTAL SYSTEMS 1H5 ...
Page 188: ...CHAPTER 22 AUTOFLIGHT 1J7 ...
Page 193: ...CHAPTER 23 COMMUNICATIONS 1J12 ...
Page 203: ...CHAPTER 24 ELECTRICAL POWER 1J22 ...
Page 263: ...CHAPTER 25 EQUIPMENT FURNISHINGS 2A13 ...
Page 269: ...CHAPTER 27 FLIGHT CONTROLS 2A20 ...
Page 332: ...CHAPTER 28 FUEL 2D11 ...
Page 363: ...CHAPTER 29 HYDRAULIC POWER 2E18 ...
Page 404: ...CHAPTER 30 ICE AND RAIN PROTECTION 2G16 ...
Page 470: ...CHAPTER 32 LANDING GEAR 3A13 ...
Page 550: ...CHAPTER 33 LIGHTS 3D24 ...
Page 562: ...CHAPTER 34 NAVIGATION AND PITOT STATIC 3E12 ...
Page 582: ...CHAPTER 35 OXYGEN 3F8 ...
Page 604: ...CHAPTER 37 VACUUM 3G6 ...
Page 616: ...CHAPTER 39 3G18 ELECTRIC ELECTRONIC PANELS MULTIPURPOSE PARTS ...
Page 620: ...CHAPTER 51 STRUCTURES 3G22 ...
Page 636: ...CHAPTER 52 DOORS 3H14 ...
Page 650: ...CHAPTER 55 STABILIZERS 3I4 ...
Page 662: ...CHAPTER 56 WINDOWS 3I16 ...
Page 670: ...CHAPTER 57 WINGS 3I24 ...
Page 688: ...CHAPTER 61 PROPELLER 3J18 ...
Page 704: ...CHAPTER 70 STANDARD PRACTICES ENGINES 3K10 ...
Page 708: ...CHAPTER 71 POWER PLANT 3K14 ...
Page 737: ...CHAPTER 73 ENGINE FUEL SYSTEM 4A13 ...
Page 749: ...CHAPTER 74 IGNITION 4B1 ...
Page 783: ...CHAPTER 77 ENGINE INDICATING 4C11 ...
Page 793: ...CHAPTER 78 EXHAUST 4C21 ...
Page 801: ...CHAPTER 79 OIL 4D5 ...
Page 805: ...CHAPTER 80 STARTING 4D9 ...
Page 819: ...CHAPTER 81 TURBINES 4D23 ...
Page 833: ...CHAPTER 91 CHARTS WIRING DIAGRAMS 4E13 ...