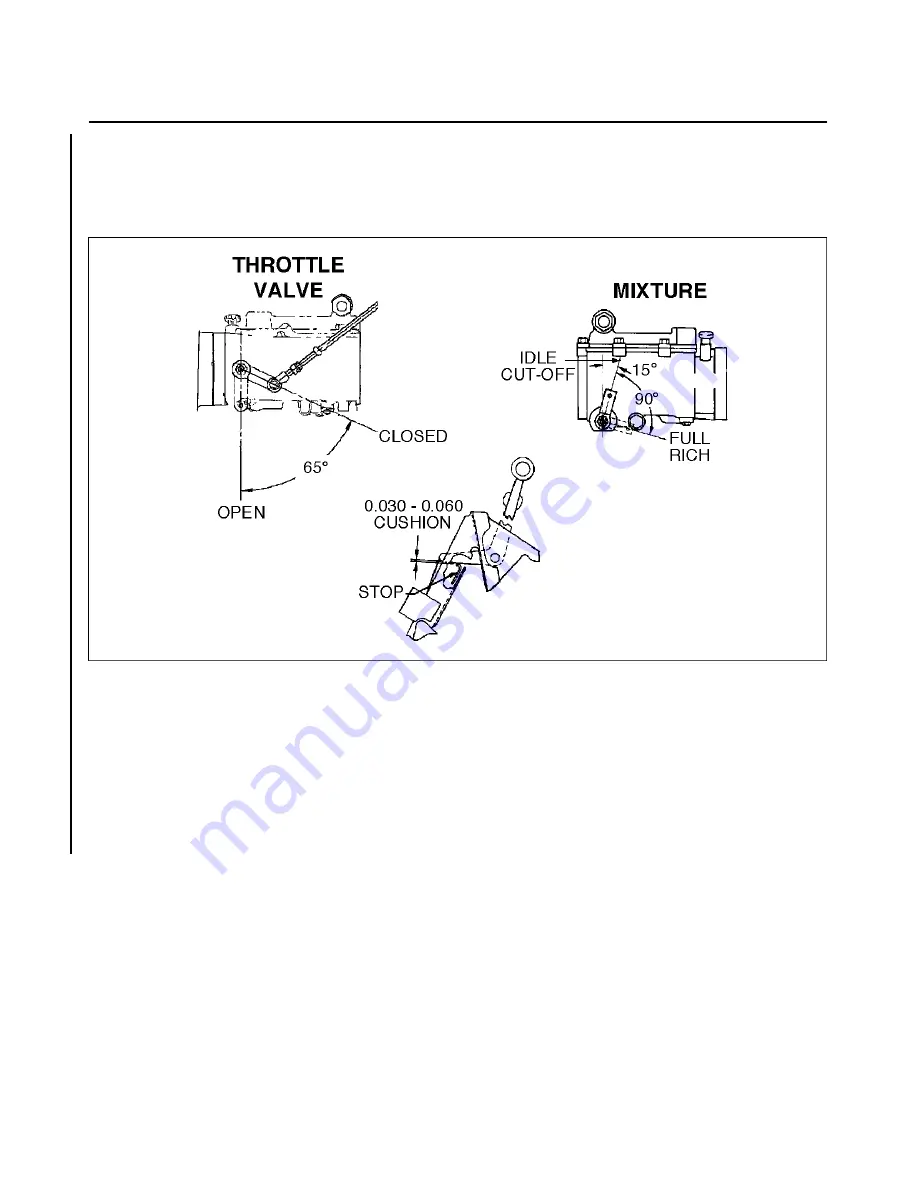
A.
At the carburetor, disconnect the clevis end of the mixture control cable from the control arm.
Loosen the jam nut that secures the clevis end.
B.
Adjust the linkage by rotating the clevis end on the cable to obtain a 0.030 to 0.060 inch cushion
from the instrument panel stop when in full rich position.
C.
Reconnect the clevis end to the control arm and safety.
Figure 73-5. Adjustment of Engine Controls (Sheet 2 of 2)
(PA-44-180, s/n’s 4495001 and up.)
3. Check security of cable casing attachments.
4 . Pull the throttle and mixture cockpit levers full aft to ensure that the carburetor idle screw contacts
its stop and the carburetor mixture control arm contacts its lean position.
5. Adjust the carburetor heat control as follows:
A.
Position the air box valve in the full cold position and the cockpit control 0.16 inch below the cold
detent.
B.
The air box valve must be in the full heat position when the cockpit control is in the hot position .
INDICATING.
FUEL PRESSURE GAUGE.
The fuel pressure gauge instruments are mounted on the instrument panel in the cluster for their respective
engines. The gauges are electrically connected to pressure senders for their respective engines: The senders
are mounted through the aft side. and outboard half of each firewall to the fuel pressure line. running from
each engine’s carburetor to the firewall. The oil pressure senders are those units with the two terminals on the
aft side of the instrument.
PIPER AIRCRAFT
PA - 4 4 - 1 8 0 / 1 8 0 T
AIRPLANE MAINTENANCE MANUAL
73-30-01
Page 73-08
Revised: June 20, 1995
3F11
Summary of Contents for SEMINOLE PA-44-180
Page 38: ...CHAPTER DIMENSIONS AND AREAS 1B14...
Page 49: ...CHAPTER LIFTING AND SHORING 1C1...
Page 53: ...CHAPTER LEVELING AND WEIGHING 1C5...
Page 58: ...CHAPTER TOWING AND TAXIING 1C10...
Page 62: ...CHAPTER PARKING AND MOORING 1C14...
Page 65: ...CHAPTER REQUIRED PLACARDS 1C17...
Page 70: ...CHAPTER SERVICING 1C22...
Page 98: ...CHAPTER STANDARD PRACTICES AIRFRAME 1E2...
Page 108: ...CHAPTER ENVIRONMENTAL SYSTEM 1E12...
Page 189: ...CHAPTER AUTOFLIGHT 1H21...
Page 192: ...CHAPTER COMMUNICATIONS 1H24...
Page 202: ...CHAPTER ELECTRICAL POWER 1I10...
Page 228: ...CHAPTER EQUIPMENT FURNISHINGS 1J12...
Page 233: ...CHAPTER FIRE PROTECTION 1J17...
Page 238: ...CHAPTER FLIGHT CONTROLS 1J24...
Page 304: ...2A18 CHAPTER FUEL...
Page 325: ...2B17 CHAPTER HYDRAULIC POWER...
Page 357: ...2D1 CHAPTER ICE AND RAIN PROTECTION...
Page 414: ...CHAPTER LANDING GEAR 2F13...
Page 479: ...2I6 CHAPTER LIGHTS...
Page 488: ...2I16 CHAPTER NAVIGATION AND PITOT STATIC...
Page 503: ...2J7 CHAPTER OXYGEN...
Page 524: ...2K6 CHAPTER VACUUM...
Page 535: ...2K19 CHAPTER ELECTRICAL ELECTRONIC PANELS AND MULTIPURPOSE PARTS...
Page 546: ...INTENTIONALLY LEFT BLANK PA 44 180 180T AIRPLANE MAINTENANCE MANUAL 2L6 PIPER AIRCRAFT...
Page 547: ...2L7 CHAPTER STRUCTURES...
Page 582: ...CHAPTER DOORS 3A18...
Page 593: ...CHAPTER STABILIZERS 3B8...
Page 604: ...CHAPTER WINDOWS 3B22...
Page 611: ...CHAPTER WINGS 3C10...
Page 624: ...CHAPTER PROPELLER 3D1...
Page 643: ...CHAPTER POWER PLANT 3D21...
Page 667: ...CHAPTER ENGINE FUEL SYSTEM 3F1...
Page 681: ...CHAPTER IGNITION 3F16...
Page 712: ...CHAPTER ENGINE INDICATING 3H1...
Page 730: ...CHAPTER EXHAUST 3H19...
Page 734: ...CHAPTER OIL 3I1...
Page 743: ...CHAPTER STARTING 3I11...
Page 755: ...CHAPTER TURBINES 3J1...