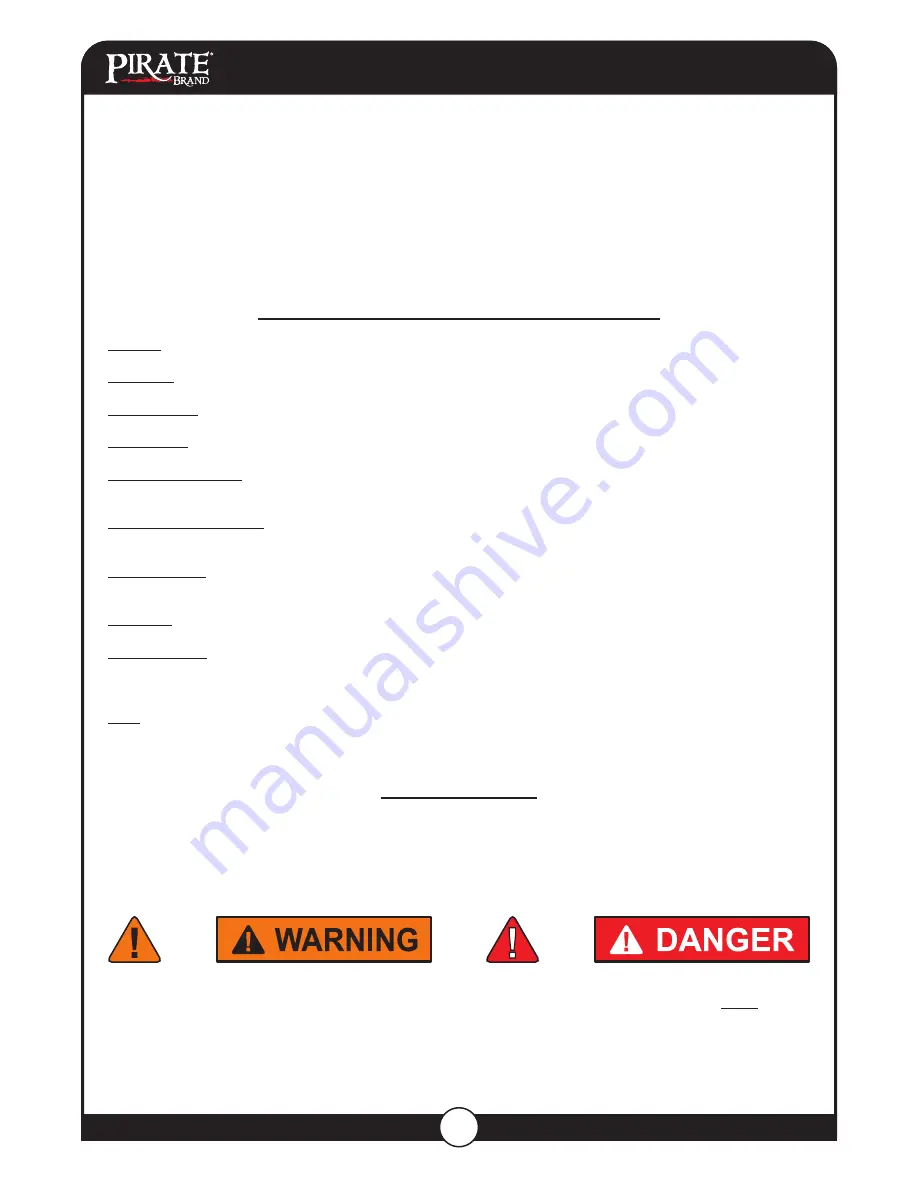
Manual Revision: June 20
Copyright © 2013-2020 Pirate Brand®, All Rights Reserved
2
C-Series Jr - 0.5 / 1.0
Cu Ft
User’s Manual
Thank you for your purchase of a Pirate Brand® CPR Series Blaster. It is important to note that
all Pirate Brand® blasting equipment is designed to be safe when used properly, however, misuse of any
abrasive blasting equipment is dangerous and can result in the severe injury or death of the operator and
others in the vicinity of the blasting equipment. In order to protect yourself and those around you, read
and follow all sections of this manual & warning labels located on the blasting equipment.
Definition Of Terms Used In This Manual
Abrasive: A granular material used for blasting the surface of an object. Also referred to as “Media.”
Blow-down: The automatic or manual release of air from a pressurized vessel. Also referred to as “Depressurize.”
Control Handle: A required device that allows the blaster to be remotely started and stopped.
Depressurize: The automatic or manual release of air from a pressurized vessel. Also known as “Blow-down”.
Pressure Hold System: Any blasting system in which the Pressure Vessel remains pressurized when the control
handle is released. Also known as a Manual Blow-down System.
Pressure Release System: Any blasting system in which the Pressure Vessel is automatically depressurized when
the control handle is released. Also known as an Automatic Blow-down System.
Pressure Vessel
: The enclosed area of the blaster in which abrasive is contained and filled with pressurized air when
blasting.
Pressurize
: To fill the pressure vessel with compressed air.
Properly Trained: A person who can be considered “properly trained” must have successfully completed a
sandblasting training course that focuses on the safe operation of stationary or portable abrasive blasters in the 0.5 -
6.0 cu. ft. capacity range. They must also have read and understood this manual in its entirety.
Silica: A hazardous substance which is contained in many naturally occurring abrasives. Dust produced by blasting
with abrasives containing silica can cause respiratory disease. Do not use abrasive containing silica under any
circumstance, even when respiratory protective equipment is being used.
Safety Symbols
The safety symbols shown below exist for the safety and protection of the operator and those in the
vicinity of the Abrasive Blaster. The descriptions below explain how they are used in relation to the
blasting equipment.
WARNING: This symbol calls attention to a
potentially hazardous situation that could result
in serious injury or death if the instructions
associated with the symbol are not followed. The
warning triangle will be displayed throughout the
manual to denote instructions to which special
attention should be paid.
DANGER: This symbol calls attention to a
potentially hazardous situation that
WILL
result
in serious injury or death if the instructions
associated with the symbol are not followed. The
warning triangle will be displayed throughout the
manual to denote instructions to which special
attention should be paid.
OR
OR
Using This Manual