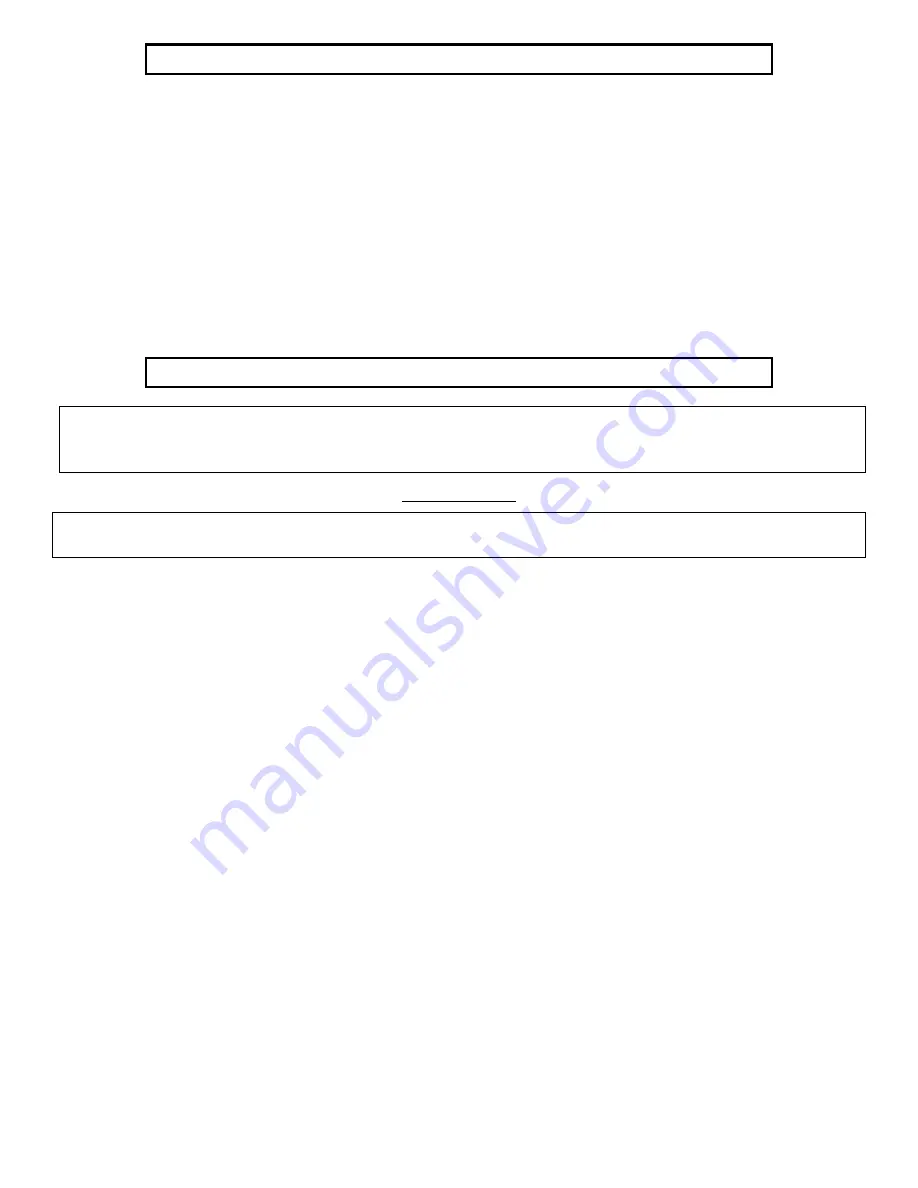
IP-010
Page
9
of
13
Revision 3
Re-pressuring and Field Testing
If the pipeline has been shut down, re-pressuring should be done with extreme caution. Re-pressuring
should be accomplished slowly and steadily without surges that could vibrate the pipeline or produce a
sudden impact load. Industry codes and standards are a good source of information on this subject.
Except for testing purposes, do not exceed the design pressure of the PLIDCO fitting. The PLIDCO
fitting is designed to be tested up to 1½ times its design pressure. However, PLIDCO recommends
following API Recommended Practice 2201, Procedures for Welding or Hot Tapping on Equipment in
Service, Section 6.5. The test pressure should be at least equal to operating pressure of the line or
vessel, but not to exceed internal pressure by 10%. This is meant to avoid possible internal collapse of
the pipe or vessel wall. However, if prevailing conditions could cause collapse of the pipe or pressure
walls, the test pressure may be reduced. (See API Standard 510 Section 5.8 for pressure testing
precautions.) Personnel should not be allowed near the repair until the seal has been proven.
Field Welding Instructions
Welding is not a requirement for the pressure sealing ability of the PLIDCO Clamp+Sleeves.
The issue of welding is dependent on your company’s requirements, applicable codes, and if
longitudinal loads need to be carried by the PLIDCO Clamp+Sleeves
!!
WARNING
!!
Failure to follow field welding instructions could result in explosion, fire, death, personal injury,
property damage and/or harm to the environment.
All of the aspects for in-service welding of PLIDCO Clamp+Sleeves are not addressed by this
document. ASME PCC-2, API 1104 Appendix B, ASME Section IX, PRCI L52047, PRCI Hot Tap®
Model, and other industry information pertaining to in-service welding must be considered when
planning in-service welding. Refer to IP-019, Welding Considerations for additional information.
It is recommended that the pipeline should be full and under flow.
Welders and weld procedures should be qualified in accordance with API Standard 1104,
Welding of
Pipelines and Related Facilities
, Appendix B,
In-Service Welding
. We strongly recommend the use of a
low hydrogen welding process such as GMAW or SMAW using low hydrogen electrodes (E-XX18)
because of their high resistance to moisture pick-up and hydrogen cracking. These are also the preferred
welding processes for seal welding the studs and nuts. SMAW electrodes must be absolutely dry.
Use weld material with equal or greater tensile strength than the pipe. Carefully control the size and
shape of the circumferential fillet welds. The size of the fillet weld should be at least 1.4 times the wall
thickness of the pipe. This assumes a 1.0 joint efficiency. You may need to select a different joint
efficiency based on your level of inspection. Strive for a concave faced fillet weld, with streamlined
blending into both members; avoid notches and undercuts. The smoother and more streamlined the
weld, the greater the resistance to fatigue failure. The worst possible shape would be a heavy reinforced
convex weld with an undercut. Improper weld shape can lead to rapid fatigue failure, which can cause
leakage, rupture or an explosion with attendant serious consequences.
It is very important that the field welding procedure closely follow the essential variables of the qualified
procedure so that the quality of the field weld is represented by the mechanical tests performed for the
procedure qualification.
We do not recommend the use of thermal blankets for pre-heating. Thermal blankets can generate hot
spots and reduce the ability of the PLIDCO Clamp+Sleeve to dissipate welding heat in the vicinity of the
seals. We recommend a small torch, such as a cutting torch, being careful not to aim the flame directly