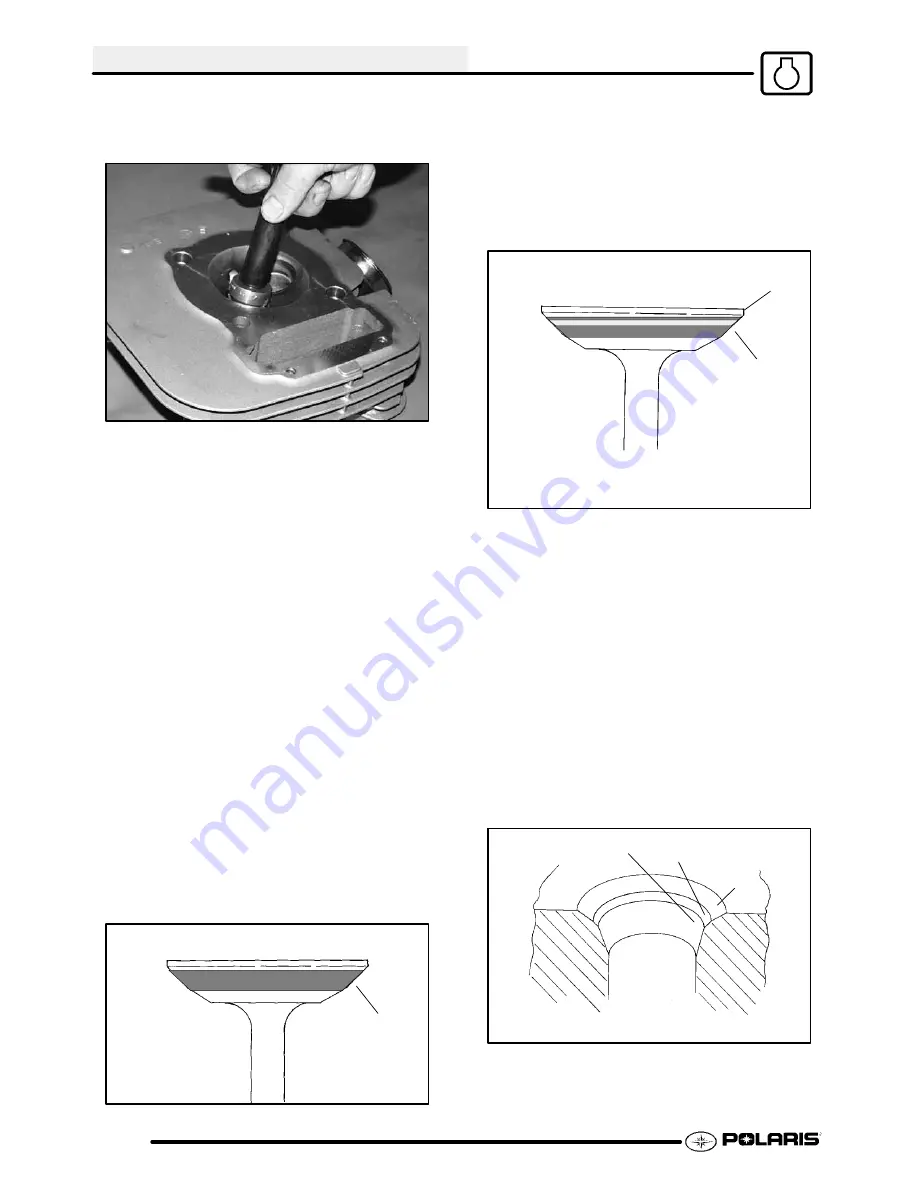
ENGINE
3.20
VALVE SEAT RECONDITIONING CONT’D
3.
Place 46
°
cutter on the pilot and make a light cut.
4.
Inspect the cut area of the seat.
G
If the contact area is less than 75%
of the circumference of the seat,
rotate the pilot 180
°
and make
another light cut.
G
If the cutter now contacts the uncut
portion of the seat, check the pilot.
Look for burrs, nicks, or runout. If the
pilot is bent it must be replaced.
G
If the contact area of the cutter is in
the same place, the valve guide is
distorted from improper installation
and must be replaced. Be sure the
cylinder head is at the proper
temperature and replace the guide.
G
If the contact area of the initial cut is
greater than 75%, continue to cut the
seat until all pits are removed and a
new seat surface is evident. NOTE:
Remove only the amount of material
necessary to repair the seat surface.
5.
To check the contact area of the seat on the valve
face, apply a thin coating of Prussian Blue
t
paste
to the valve seat. If using an interference angle
(46
°
) apply black marker to the entire valve face
(A).
(A)
6.
Insert valve into guide and tap valve lightly into
place a few times.
7.
Remove valve and check where the Prussian
Blue
t
or black marker indicates seat contact on
the valve face. The valve seat should contact the
middle of the valve face or slightly above, and
must be the proper width (A).
(A)
(B)
Proper Seat Contact On Valve Face
G
If the indicated seat contact is at the
top edge of the valve face and
contacts the margin area(B) it is too
high on the valve face. Use the 30
°
cutter to lower the valve seat.
G
If too low use the 60
°
or 75
°
cutter to
raise the seat. When contact area is
centered on the valve face, measure
seat width.
G
If the seat is too wide or uneven, use
both top and bottom cutters to
narrow the seat.
G
If the seat is too narrow, widen using
the 45
°
cutter and re-check contact
point on the valve face and seat width
after each cut.
Bottom - 60
°
or 75
°
Seat - 45
°
or 46
°
Top - 30
°
PartShark.com
877-999-5686
Summary of Contents for 2009 Trail Blazer 330
Page 94: ...ENGINE 3 48 NOTES P a r t S h a r k c o m 8 7 7 9 9 9 5 6 8 6 ...
Page 110: ...FUEL SYSTEM CARBURETION 4 16 NOTES P a r t S h a r k c o m 8 7 7 9 9 9 5 6 8 6 ...
Page 124: ...BODY STEERING SUSPENSION 5 14 NOTES P a r t S h a r k c o m 8 7 7 9 9 9 5 6 8 6 ...
Page 196: ...ELECTRICAL 10 4 REVERSE LIMIT SYSTEM P a r t S h a r k c o m 8 7 7 9 9 9 5 6 8 6 ...
Page 226: ...ELECTRICAL 10 34 NOTES P a r t S h a r k c o m 8 7 7 9 9 9 5 6 8 6 ...
Page 227: ...ELECTRICAL WIRING DIAGRAM 2009 TRAIL BOSS P a r t S h a r k c o m 8 7 7 9 9 9 5 6 8 6 ...
Page 228: ...ELECTRICAL WIRING DIAGRAM 2009 TRAIL BOSS P a r t S h a r k c o m 8 7 7 9 9 9 5 6 8 6 ...
Page 229: ...ELECTRICAL WIRING DIAGRAM 2009 TRAIL BLAZER P a r t S h a r k c o m 8 7 7 9 9 9 5 6 8 6 ...
Page 230: ...ELECTRICAL WIRING DIAGRAM 2009 TRAIL BLAZER P a r t S h a r k c o m 8 7 7 9 9 9 5 6 8 6 ...