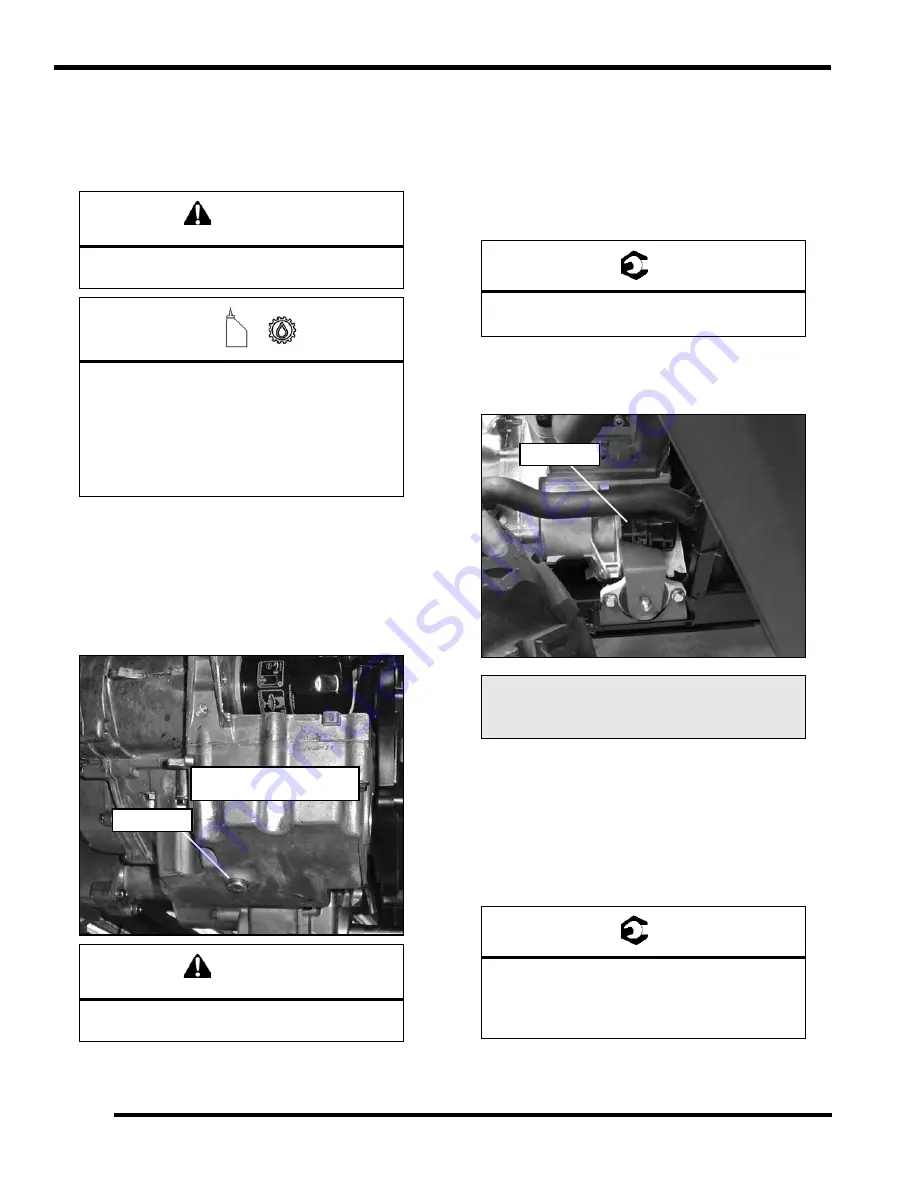
2.16
MAINTENANCE
9924125 - 2013
RANGER
RZR / RZR S / RZR 4 Service Manual
© Copyright 2012 Polaris Sales Inc.
Engine Oil and Filter Service
Always change engine oil and filter at the intervals outlined
in the Periodic Maintenance Chart. Always change the oil
filter whenever changing the engine oil.
1.
Position vehicle on a level surface.
2.
Place the transmission in PARK (P).
3.
Start the engine. Allow it to idle for two to three
minutes until warm. Stop the engine.
4.
Clean area around oil drain plug at bottom of engine.
5.
Place a drain pan beneath engine crankcase and
remove the drain plug.
6.
Allow oil to drain completely.
7.
Replace the sealing washer on drain plug.
NOTE: The sealing surface on the drain plug should
be clean and free of burrs, nicks or scratches.
8.
Reinstall drain plug and torque to specification.
9.
Place shop towels beneath oil filter. Using Oil Filter
Wrench (PU-50105) and a 3/8” extension, turn the oil
filter counter-clockwise to remove it.
10. Using a clean dry cloth, clean filter sealing surface on
the crankcase.
11. Lubricate O-ring on new filter with a film of fresh
engine oil. Check to make sure the O-ring is in good
condition.
12. Install new filter to specification.
WARNING
Personal injury can occur when handling used
oil. Hot oil can cause burns or skin damage.
=
Recommended Engine Oil / Filter:
PS-4 Plus Synthetic 4-Cycle Engine Oil
(PN 2876244) (Quart)
Engine Oil Filter (PN 2540086)
Capacity:
2 Quarts (1.9 L)
CAUTION
Oil may be hot. Do not allow hot oil to come into
contact with skin, as serious burns may result.
Drain Plug
NOTE: Drain plug is accessed
through the skid plate.
=
T
Crankcase Drain Plug:
16 ft-lbs (22 Nm)
Oil Filter Wrench:
PU-50105: 2.5” (64 mm)
=
T
Oil Filter:
Turn by hand until filter O-ring contacts
sealing surface, then turn an additional 1/2
turn
Oil Filter
PRELIMINARY
VERSION
Summary of Contents for 2013 RANGER RZR
Page 417: ...2013 RANGER RZR 800...
Page 418: ...2013 RANGER RZR 800...
Page 419: ...2013 RANGER RZR 800 EPS...
Page 420: ...2013 RANGER RZR 800 EPS...
Page 421: ...2013 RANGER RZR S 800...
Page 422: ...2013 RANGER RZR S 800...
Page 423: ...2013 RANGER RZR S 800 INT L...
Page 424: ...2013 RANGER RZR S 800 INT L...
Page 425: ...2013 RANGER RZR 4 800...
Page 426: ...2013 RANGER RZR 4 800...
Page 427: ...2013 RANGER RZR 4 800 EPS...
Page 428: ...2013 RANGER RZR 4 800 EPS...