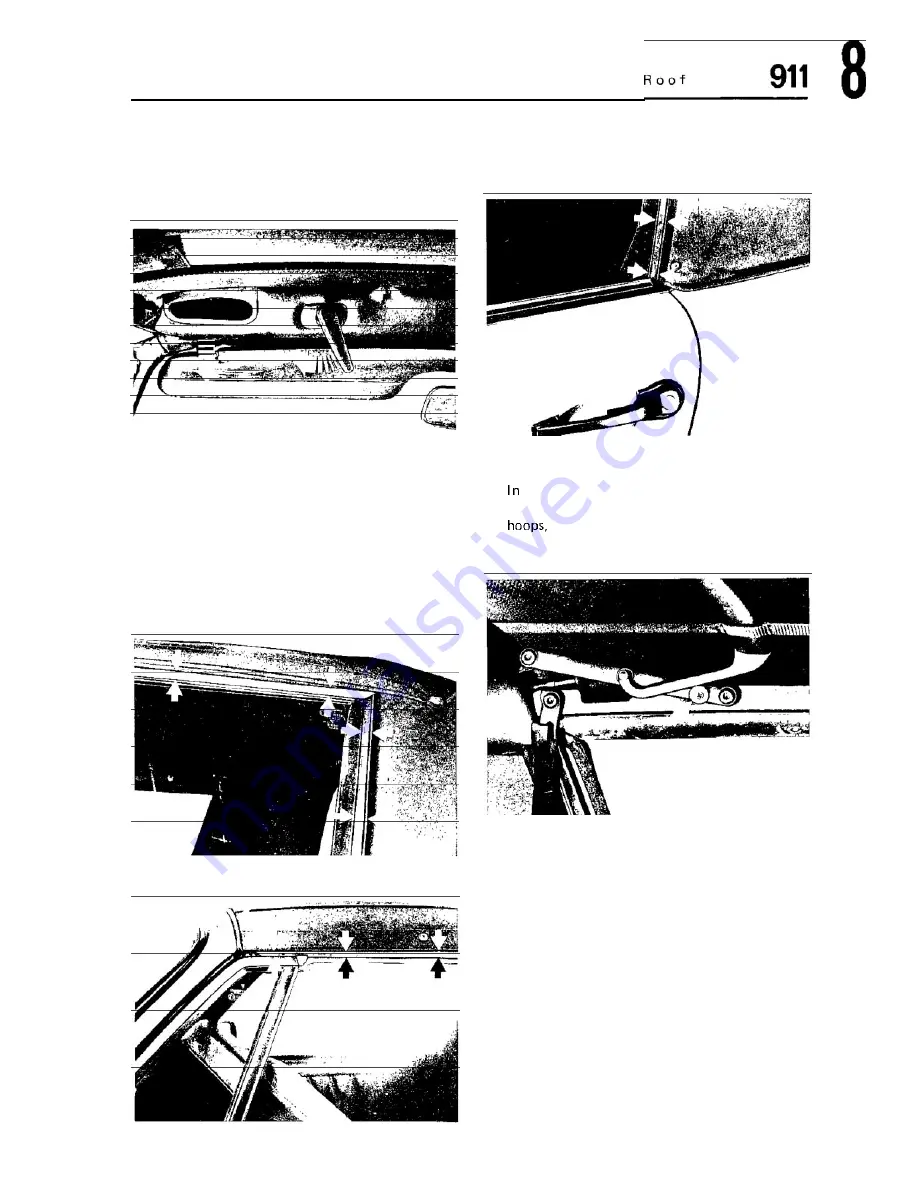
3.
Close top, pull down on grip plate with one hand
and lock lock simultaneously.
Repeat this step on the other side.
4.
If the top
i s
closed, make sure that there is equal
distance from the top frame to the windows. I f
not, center door frames and windows t o the top
frame.
5.
order t o have a smooth contour on the front
top canvas cover between the front and rear
the eccentric has t o be adjusted accord-
ingly.
Summary of Contents for 1972 911
Page 1: ...Workshop manual DR ING h c F PORSCHE KG STUTTGART ZUFFENHAUSEN ...
Page 3: ...Motor und Kupplung Engine and Clutch Moteur et Accouplement Motore e Frizione ...
Page 7: ......
Page 13: ......
Page 14: ......
Page 16: ...D e s c r i p t i o n 9 1 1 1 ...
Page 20: ......
Page 21: ...D e s c r i p t i o n ...
Page 22: ...D e s c r i p t i o n 911 1 ...
Page 25: ...9 1 1 T e c h n i c a l D a t a ...
Page 30: ...Horsepower Output Ne DIN HP b ...
Page 31: ...911 T e c h n i c a l D a t a Full power Performan s C1L Engine Speed n rpm vJ ...
Page 33: ...T e c h n i c a l D a t a 911 1 Full power Performance Carrera Q Engine Speed n rpm a ...
Page 39: ...c i a a 911 1 ...
Page 40: ...fl T e c h n i c a l D a t a ...
Page 41: ...ine Speed n rpml W V ...
Page 44: ...T e c h n i c a l D a t a 911 1 ...
Page 56: ...C o o l i n g S y s t e m Exhaust System E m i s s i o n C o n t r o l 9 4 3 11 0 Z W ffi ...
Page 57: ......
Page 97: ...C a m s h a f t H o u s i n g a n d C y l i n d e r H e a d 911 ...
Page 143: ...REMOVING A N D I N S T A L L I N G T H R O W O U T BEARING ...
Page 147: ...C L U T C H M O D I F I C A T I O N S 1 9 7 8 M O D E L S ...
Page 149: ...Kraftstoffanlage Fuel System Systeme d alimentation Sistema d alimentazione ...
Page 155: ...D e s c r i p t i o n ...
Page 164: ......
Page 169: ......
Page 202: ...V A C U U M S Y S T E M L A Y O U T 1 9 7 8 M o d e l s ...
Page 213: ...S e r v i c i n g 3 I I 2 D I S A S S E M B L I N G A N D R E A S S E M B L I N G ...
Page 217: ......
Page 230: ...R e p a i r s D I S M A N T L I N G A N D ASSEMBLING M I X T U R E C O N T R O L U N I T ...
Page 280: ...Getriebe Transmission Bo itede Vitesses Cambio ...
Page 285: ...3 911 M a n u a l T r a n s m i s s i o n I ...
Page 291: ...911 T r a n s m i s s i o n ...
Page 298: ......
Page 300: ...o t o t i 911 3 ...
Page 305: ...S p o r t o m a t i c ...
Page 309: ...Transmission Diagram 5 speed transmission Ring Ratio 7 31 ...
Page 310: ...Transmission Diagram 4 speed transmission Pinion to Ring Ratio 7 31 Type 915 Transmission ...
Page 318: ...I T e c h n i c a l D a t a ...
Page 321: ...T e c h n i c a l D a t a 911 ...
Page 325: ...TransmissionDiagram 5 speed transmission Pinion to Rlng Ratio 8 31 Type 915 44 Transmission ...
Page 327: ...T e c h n i c a l D a t a 911 ...
Page 331: ...T e c h n i c a l D a t a 911 ...
Page 333: ......
Page 336: ...TransmissionDiagram Sportomatic Pinion to Ring Ratio 8 27 Type 925 09 12 13 Transmission ...
Page 339: ......
Page 359: ...D i s a s s e m b l y a n d R e a s s e m b l y ...
Page 386: ...911 M a n u a l T r a n s m i s s i o n ...
Page 395: ...M a n u a l T r a n s m i s s i o n 9 1 1 3 RELEASE LEVER 1 9 7 8 M O D E L S ...
Page 421: ...S p o r t o m a t i c Disassembling and Assembling Transmission ...
Page 430: ...911 S p o r t o m a t i c Disassembling and Assembling Transmission Front Cover ...
Page 433: ...S p o r t o m a t i c 9 1 1 3 4 Install shift rod seal with special tool P 218 ...
Page 442: ...9 1 1 S p o r t o m a t i c D I S M A N T L I N G A N D A S S E M B L I N G ...
Page 446: ...D I S M A N T L I N G A N D A S S E M B L I N G ...
Page 464: ...911 F i n a l D r i v e M a n u a l T r a n s m i s s i o n ...
Page 468: ......
Page 486: ...Vorderachse Front Axle ssieu AV Assale anteriore ...
Page 501: ...REMOVING A N D I N S T A L L I G F R O N T AXLE BALL J O I N T ...
Page 507: ...911 F r o n t A x l e D I S A S S E M B L Y A N D R E A S S E B L Y ...
Page 512: ...911 S t e e r i n g W h e e l a n d S t e e r i n g C o l u m n DISASSEMBLY A N D REASSEMBLY ...
Page 518: ...Hinterachse Rear Axle Essieu AR Assale posteriore ...
Page 528: ...5 911 R e a r A x l e DISASSEMBLY A N D REASSEMBLY ...
Page 537: ...Brernsen Rader Reifen Brakes Wheels Tires Freins Roues Pneus Freni Ruote Gomme ...
Page 544: ...B r a k e s W h e e l s T i r e s 911 6 REMOVING A N D I N S T A L L I N G BRAKE BOOSTER ...
Page 563: ...Hebelwerk Pedal System and Levers Pedalier et Leviers Pedaleria e Leve ...
Page 567: ...D I S A S S E M B L I N G A N D A S S E M B L I N G S H I F T LEVER ASSEMBLY ...
Page 573: ...D I S A S S E M B L Y A N D REASSEMBLY ...
Page 586: ...11 P e d a l C o n t r o l s D I S A S S E M B L I N G A N D R E A S S E M B L I N G ...
Page 592: ...7 911 P e d a l C o n t r o l s D I S A S S E M B L Y A N D REASSEMBLY ...
Page 601: ...Aufbau Body Carrosserie Carrozzeria ...
Page 614: ...B u m p e r s 911 F R O N T B U M P E R S E F F E C T I V E W I T H 1 9 7 4 M O D E L S ...
Page 618: ...B u m p e r s 9 1 1 8 R E A R BUMPER E F F E C T I V E W I T H 1 9 7 4 M O D E L S ...
Page 625: ...Rear L i d w i t h S p o i l e r 911 8 ...
Page 648: ......
Page 722: ...F l o o r P a n e l A s s e m b l y D i m e n s i o n s 50 ...
Page 746: ...53 B o d y R e a r B O D Y R E P A I R S R E A R ...
Page 755: ...Elektrische Anlage Electrical System Installation electrique lmpianto elettrico ...
Page 777: ...Current flow diagram Type 911USA Model 74 9 ...
Page 781: ...Additional current flow diagram CIS injection and Sportomatic Type 911 Model 74 9 ...
Page 783: ...Current flow diagram Type 911USA Model 75 9 ...
Page 785: ...Current flow diagram Type 911USA Model 75 ...
Page 789: ...Additional current flow diagram headlight washers Type 911 ...
Page 794: ...Additional current flow diagram power windows Type 911 ...
Page 797: ...Additional current flow diagram windshield and rear window defoggers Type 911 ...
Page 799: ...Current flow diagram Type 911S USA Model 76 9 ...
Page 800: ......
Page 801: ...Current flow diagram Type 911S USA Model 76 ...
Page 802: ...Additional current flow diagram automatic speed control Type 911 ...
Page 804: ...Additional current flow diagram intermittent wiper operation Model 76 ...
Page 806: ...Additional current flow diagram air conditioner with front condenser ...
Page 808: ...Additional current flow diagram fog lights ...
Page 811: ...Additional current flow diagram remotely controlled outside mirrors Type 911 9 ...
Page 813: ...Current flow diagram Type 911 S USA Model 77 g ...
Page 815: ...Current flow diagram Type 911 S USA Model 77 ...
Page 819: ...Current flow diagram Type 911SC USA Model 78 9 ...
Page 821: ...Current flow diagram 9 Type 911 SC USA Model 78 ...
Page 823: ...Additional current flow diagram power windows Type 911 from model 77 ...
Page 825: ...Additional Current Flow Diagram Air Conditioner M 399 Type 911 from model 77 ...
Page 827: ...AdditionalCurrent Flow Diagram Type 911SCUSA Model 80 Oxygen Sensor System ...
Page 838: ...Current Flow Diagram Type 911 SC USA Model 81 Part W FRESH AIR BLOWER ...
Page 840: ......
Page 841: ...Current Flow Diagram Type 911SC USA Model 81 Part VI OXYGENSENSOR SYSTEM ...
Page 842: ......
Page 854: ......
Page 856: ...Current Row Diagram Type 911 SC USA Model82 Part IV 1 5 bk FRESH AIR BLOWER ...
Page 858: ...Current Flow Diagram Type 911 SC USA Model82 Part V ...
Page 859: ...Current Flow Diagram Type 911 SC USA Model 82 Part VI OXYGEN SENSOR SYSTEM HEADLIGHT WASHER ...
Page 871: ...D i s a s s e m b l i n g a n d A s s e m b l i n g S t a r t e r ...
Page 984: ......