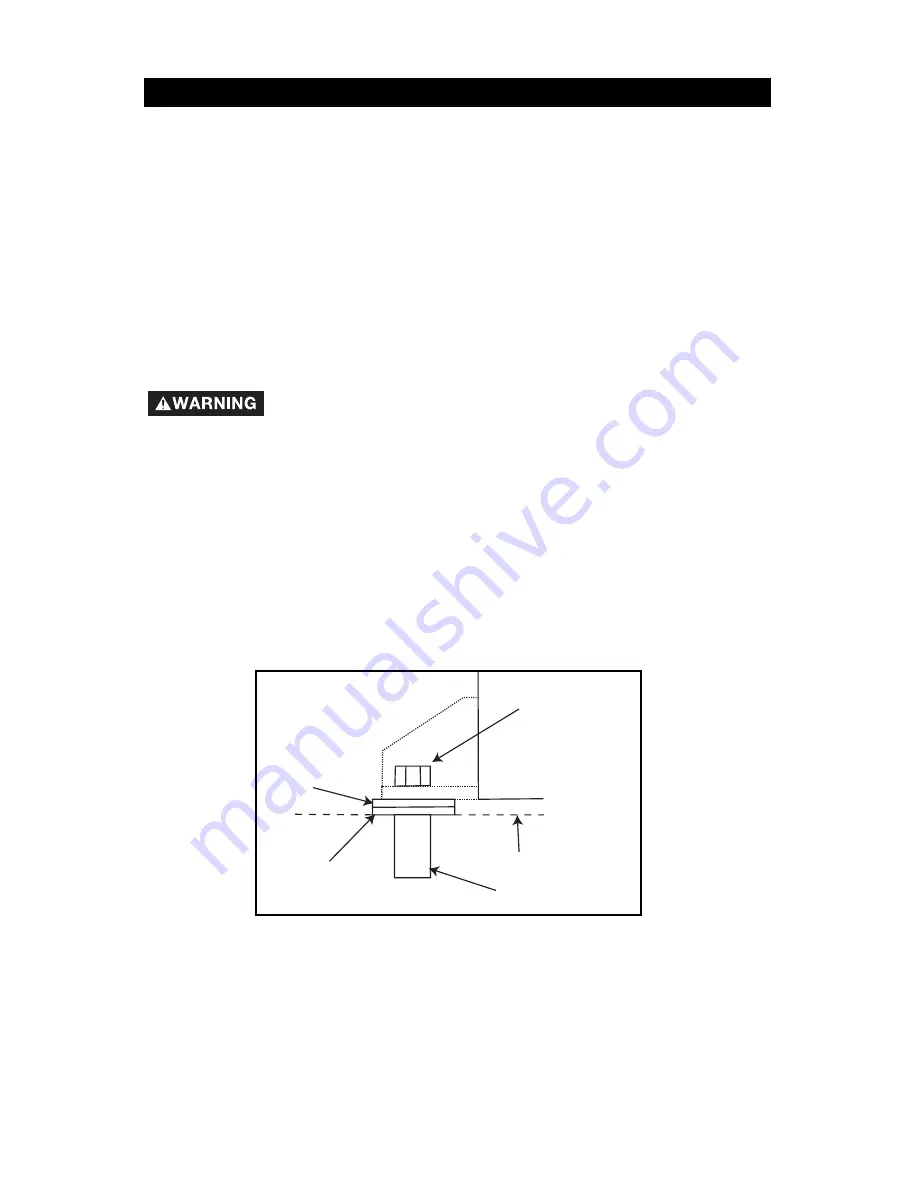
10- ENG
D28176
Anchoring of the Air Compressor
Excessive Vibration can weaken the air tank and cause an
explosion. The compressor must be properly mounted.
The air compressor MUST be bolted to a solid, level surface.
Hardware needed:
4 - Concrete anchors (not supplied)
4 - 3/8” Lag screw to fit concrete anchors
(not supplied)
4 - 5/8” Washer (found in parts bag)
shims (if needed)
1.
Place the air compressor on on a solid, level surface.
2.
Mark the surface using the holes in the air compressor feet as a template.
3.
Drill holes in the surface for the concrete anchors. Install concrete anchors.
4.
Line-up holes in surface with holes in air compressor feet.
5.
Place the (4) washers (supplied) between the floor and air compressor feet.
If needed, solid shims may be placed between the washers and floor to
evenly distribute weight on all four feet.
6.
Place the (4) 3/8” lag screws through the air compressor feet, washers,
shims, and into the anchors.
7.
Torque 3/8” lag screws to 7-10 ft.-lbs.
Location of the Air Compressor
•
Locate the air compressor in a clean, dry, and well ventilated area.
•
Locate the air compressor at least 12" away from the wall or other
obstructions that will interfere with the flow of air.
•
Locate the air compressor as close to the main power supply as possible
to avoid using long lengths of electrical wiring. NOTE: Long lengths of
electrical wiring could cause power loss to the motor.
•
The air filter must be kept clear of obstructions which could reduce air flow
to the air compressor.
HOW TO SET UP YOUR UNIT
3/8” Lag
Screw
(not supplied)
5/8” Washer
(supplied)
Shim Under
Washer
(not supplied)
Concrete Anchor
(not supplied)
Surface Line
INSTALLATION
Summary of Contents for C7510
Page 27: ...27 ENG D28176 NOTES...