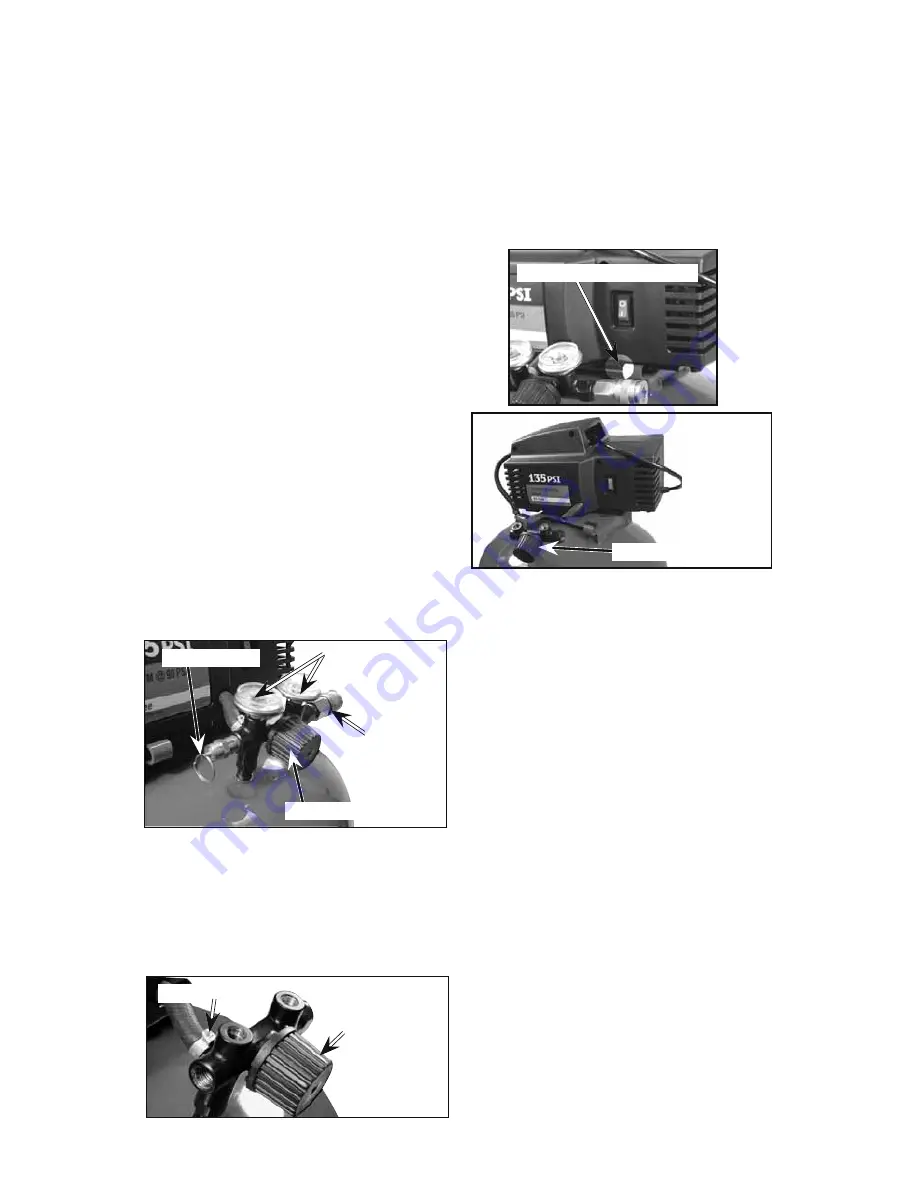
5. Make sure the valve disc moves
freely inside the check valve
and the spring holds the disc in
the upper, closed position. The
check valve may be cleaned
with a solvent, such as paint and
varnish remover.
6. Apply sealant to the check valve
threads. Reinstall the check valve
(turn clockwise).
7. Replace hose and new hose
clamp.
8. Perform the Break-in Procedure.
See "Break-in Procedure" in the
Operation section.
15 - ENG
A07300
5. Remove pump mounting screws
securing pump (one on each
side).
6. Carefully slide pump from
brackets and out of the way.
7. Using an adjustable wrench or
5/8" wrench remove the regulator
manifold.
8. Apply pipe sealant to new
regulator manifold and assemble,
tighten with wrench.
9. Reapply pipe sealant to gauges,
quick connect, and safety valve.
10. Reassemble all components in
reverse order of removal. Make
sure to orient gauges to read
correctly and use wrenches to
tighten all components.
To Replace Regulator
1. Release all air pressure from air
tank. See "To Drain Tank" in the
Maintenance section.
2. Unplug
unit.
3. Using an adjustable wrench or
specified wrench remove the
gauges (7/16" wrench), quick
connect (13/16" wrench), and
safety valve (9/16" wrench) from
the regulator manifold.
4. Remove the hose by removing
the hose clamp.
NOTE:
The hose
clamp is not reusable. You must
purchase a new hose clamp, see
the Parts List Manual or purchase
a standard hose clamp at a local
hardware store.
Pump Mounting Screw
Quick
Connect
Gauges
Safety Valve
Regulator Manifold
Hose Clamp
Regulator
Manifold
Pump shown
moved out of
the way
Regulator Manifold
Summary of Contents for CFBN125A
Page 17: ...17 ENG A07300 NOTES...