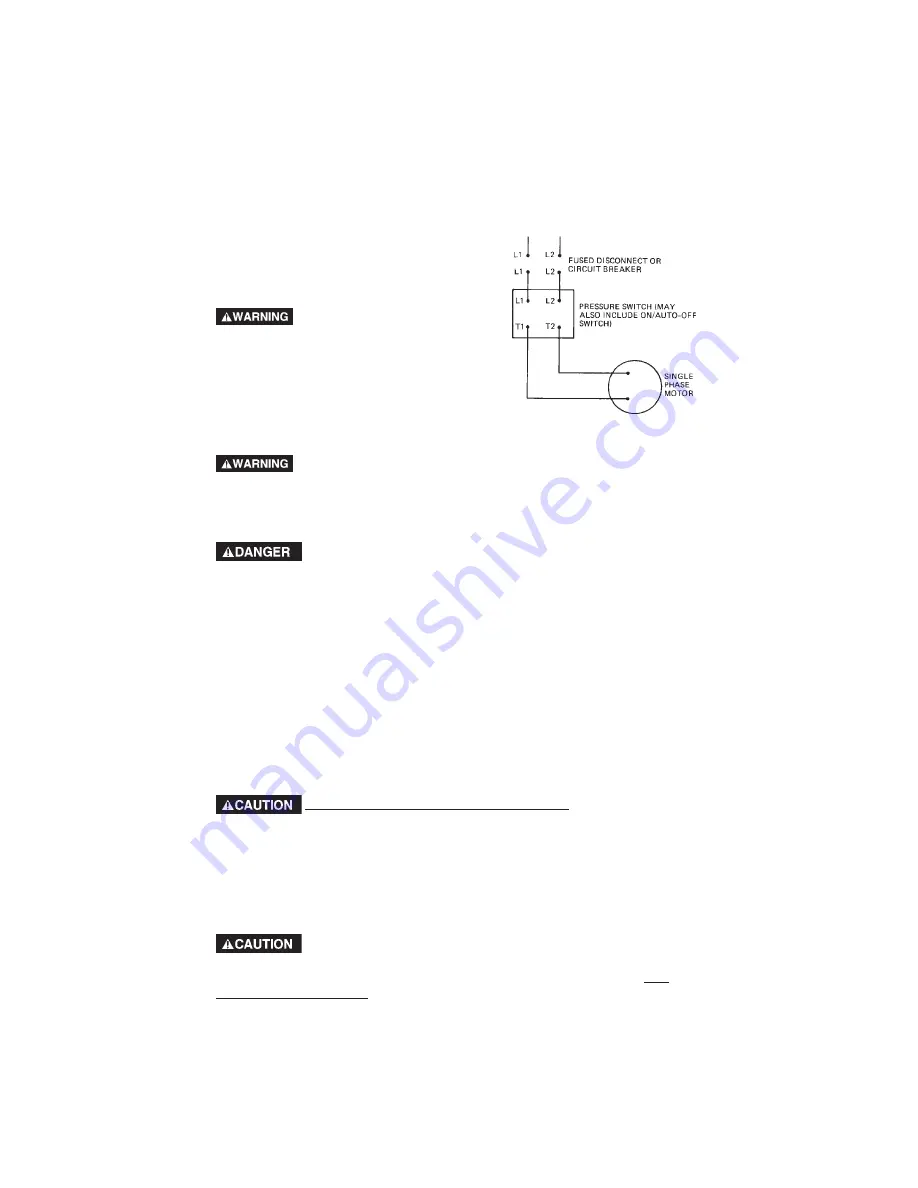
10-ENG
GROUNDING INSTRUCTIONS
RISK OF ELECTRICAL
SHOCK! In the event of a short circuit,
grounding reduces the risk of shock by
providing an escape wire for the electric
current. This air compressor must be properly grounded.
Improper grounding can result in electrical shock! All
grounding should be performed by a licensed electrician in
accordance with national and local electrical codes!
Make certain that the electrical circuit to which the air compressor is connected
provides proper electrical grounding, correct voltage and adequate fuse protection.
The air compressor can be grounded by the following method:
When hard wiring an air compressor, use wiring that contains a bare copper
grounding wire. This wire must be connected to the pressure switch at the
grounding location provided. This is located inside the pressure switch. The other
end of the wire must be connected to a ground at the fuse/circuit breaker box in
accordance with national and local electrical codes.
If these grounding instructions are not completely understood, or if you are in
doubt as to whether the air compressor is properly grounded, have the installation
checked by an Authorized Warranty Service Center or a licensed electrician.
Lubrication and Oil
Air compressors are shipped without oil. A small
amount of oil may be present in the pump upon receipt of the air
compressor. This is due to plant testing and does not mean that the
pump contains the correct amount of oil. Do not attempt to operate in
order to check wiring or for any reason without first adding oil to the
crankcase. Serious damage to the pump can result from even very
limited use without oil. Fill crankcase with recommended oil before
operating.
Multi-viscosity motor oils like 10W30, should not be
used in an air compressor. They leave carbon deposits on critical
components, thus reducing performance and air compressor life. Use
air compressor oil only.
Voltage and Circuit Protection
Refer to the Specifications for the voltage and
circuit protection requirements of your air
compressor. Use only a fuse or circuit breaker
that is the same rating as the branch circuit on
which the air compressor is operated. If the air
compressor is connected to a circuit protected
by fuses, use only dual element time delay fuses,
as noted in the Specifications.
This product should be
connected to a grounded, metallic,
permanent wiring system, or an
equipment-grounding terminal or lead on
the product.
Typical schematic subject
to all changes as dictated
by local electrical codes
and authorities.
Fig. 4
Summary of Contents for CPLC7060V
Page 25: ...25 ENG NOTES ...