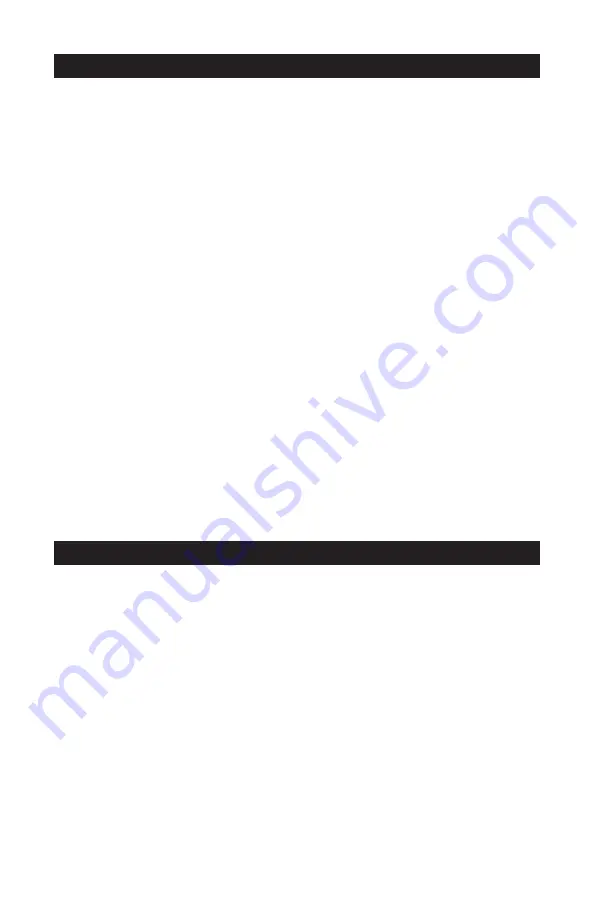
18- ENG
MAINTENANCE
SERVICE INTERVAL
CLEANING THE AIR FILTER
A dirty air filter will reduce the compressor’s performance and life. To avoid
any internal contamination of the pump, the filter should be cleaned frequently,
and replaced on a regular basis. Felt filters should be cleaned in warm, soapy
water, rinsed, and allowed to air dry before reinstallation. Paper filters should be
replaced when dirty. Do not allow the filter to become filled with dirt or paint. If
the filter becomes filled with paint, it should be replaced. Direct exposure to dirty
conditions or painting areas will void your warranty.
CHECKING THE RELIEF VALVE
Pull the relief valve daily to ensure that it is operating properly and to clear the
valve of any possible obstructions.
TESTING FOR LEAKS
Check that all connections are tight. A small leak in any of the hoses, transfer
tubes, or pipe connections will substantially reduce the performance of your air
compressor. If you suspect a leak, spray a small amount of soapy water around
the area of the suspected leak with a spray bottle. If bubbles appear, repair or
replace the faulty component. Do not overtighten any connections.
STORAGE
Before storing the compressor for a prolonged period, use an air blow gun to
clean all dust and debris from the compressor. Disconnect the power cord and
coil it up. Pull the pressure relief valve to release all pressure from the tank. Drain
all moisture from the tank. Clean the filter element and filter housing; replace the
element if necessary. Drain the oil from the pump crankcase and replace it with
new oil. Cover the entire unit to protect it from moisture and dust.
Perform the following maintenance at the intervals indicated below.
I
nspect and clean air filter ..........................................................................Daily
Check pump oil level ...................................................................................Daily
Change pump oil .................................................... Every 100 operating hours
.........................................
Use synthetic blend, nondetergent air compressor oil.
Operate the pressure relief valves .............................................................Daily
Check belt tension ................................................... Every 50 operating hours
Drain tank .....................................................................................................Daily
Check and tighten all bolts
(Do not overtighten) .............................................. .Every 100 operating hours
Summary of Contents for PXCM201
Page 12: ...13 ENG A Full B Add Fig 6 OPEN CLOSE F...
Page 27: ...NOTES...