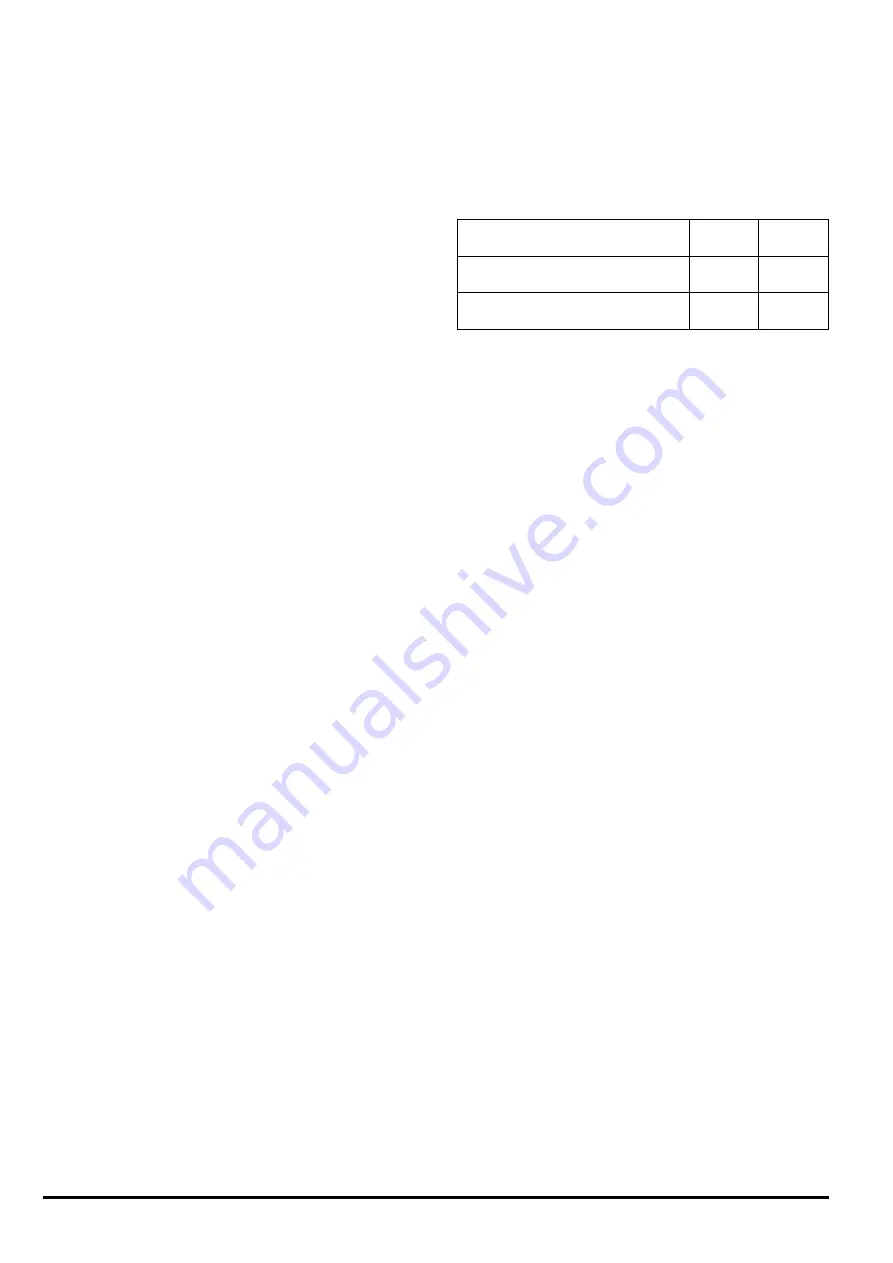
Publication No. 5105703
10
Cylinder
The hot water cylinder must be an indirect coil type or a
direct cylinder fitted with an immersion calorifier suitable
for operating at a gauge pressure of 0.3 bar (5 lbf/in²) in
excess of safety valve setting. Single feed indirect
cylinders are not suitable for sealed systems.
Method of Make-up
Provision shall be made for replacing water loss from the
system either:-
i) from a make-up vessel or tank mounted in a position
higher than the top point of the system, and connected
through a non-return valve to the system on the
return side of the hot water cylinder or the return side
of all heat emitters.
or
ii) where access to a make-up vessel would be difficult
by using the mains top up method or a remote
automatic pressurisation and make-up unit as shown
in Figs. 7.
Mains Connection
There shall be no connection to the mains water supply
or to the water storage tank which supplies domestic hot
water even though a non-return valve, without the
approval of the Local Water Authority.
Filling Point
The system shall be fitted with a filling point at low level
which incorporates a stop valve to BS 1010 and a double
check valve of an acepted type to be fitted in this order
from the system mains, see Fig. 7.
1.5
1.0
V x 0.087
Vessel Charge Pressure (bar)
Initial System Pressure (bar)
Expansion Vessel Volume (litres)
0.5
1.0
V x 0.11
Table 1.
Installation Requirements
Sealed Systems
Installation
The installation must comply with the requirements of
BS 6798: 1987 and BS 5449: Pt 1. The British Gas
publication "British Gas Specification for Domestic
Wet Central Heating Systems" should also be consulted.
Pressure Relief Valve
A non-adjustable spring-loaded pressure relief valve,
preset to operate at 3 bar (45lbf/in²) shall be used. It
must comply with BS 6759: Pt 1. and include a manual
testing device. It shall be positioned in the flow pipe
either horizontally or vertically upwards and close to
the boiler. No shut-off valves are to be placed between
the boiler and the safety valve. The valve should be
installed with a discharge pipe which permits the safe
discharge of steam and hot water such that no hazard
to persons or damage to electrical components is
caused.
Pressure Gauge
A pressure gauge incorporating a fill pressure indicator,
covering the range 0 - 4 bar (60 lbf/in²) shall be fitted to
the system. It should be connected to the system,
preferably at the same point as the expansion vessel.
Its location should be visible from the filling point.
Expansion Vessel
A diaphragm type expansion vessel to BS 4814: Pt 1.
shall be fitted close to the inlet side of the pump. The
connecting pipework should not be less than 15 mm.
Pipework connecting the expansion vessel should not
incorporate valves of any sort. Methods of supporting
the vessel are supplied by the vessel manufacturer.
The nitrogen or air charge pressure of the expansion
vessel shall not be less than the hydrostatic head,
(height of the top point of the system above the
expansion vessel). To size the expansion vessel it is
first necessary to calculate the volume of water in the
system in litres. The following volumes may be used as
a conservative guide to calculating the system volume.
Boiler Heat Exchanger:
2.1 litres
Small Bore Pipework:
1 litre per kW of system
output
Micro Bore Pipework:
7 litres
Steel Panel Radiators:
8 litres per kW of system
output
Low Water Capacity Rads:
2 litres per kW of system
output
Hot Water Cylinder:
2 litres
If the system is extended, the expansion vessel
volume may have to be increased unless provision has
been made for extension. Where a vessel of the
calculated size is not available, the next available
larger size should be used.
The boiler flow temperature is controlled at approximately
82 °C. The vessel size can now be determined from the
information in Table 1 where V = System volume in
litres.