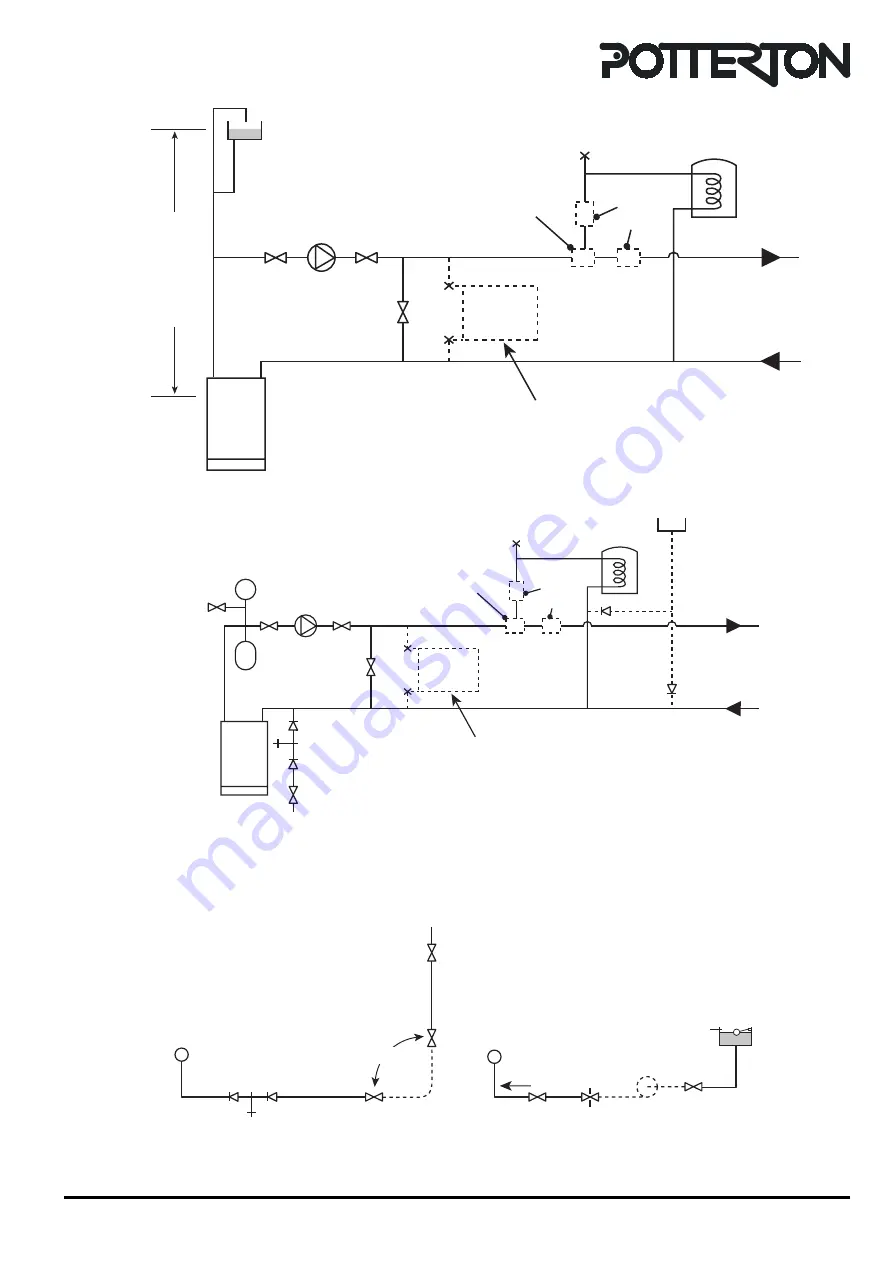
Publication No. 5105703
11
Fig. 5
Fig. 7
Installation Requirements
PRF0008A
Top
of Heat
Exchanger
Boiler
Alternative By-pass arrangement using the
Bathroom Radiator fitted with two locksheild valves
Water Level
By-pass
balancing
valve
Vent
Optional
Zone
Valves
Optional
3 Port
Valve
Max.
30.5m (100ft)
Min.
305mm (1ft)
PRF0009A
Boiler
Alternative By-pass arrangement using the
Bathroom Radiator fitted with two locksheild valves
By-pass
balancing
valve
Safety
Valve
Pressure
Gauge
Make up
Vessel
Expansion
Vessel
Cylinder
Filling Point
Vent
Optional
Zone
Valves
Optional
3 Port
Valve
PRF0010A
Two methods of filling a sealed
water system
Method 2
Cistern Filling Method
Note: Cistern to be supplied through a
temporary connection from a service
pipe or cold water distributing pipe
Method 1
Mains Topping-up Method
Note: This method of filling
a sealed system may only be
used if acceptable to the Local
Water Undertaking
Mains
Water
Supply
Overflow
Cistern
Pressure Pump
reducing valve
(if required)
Stop Valve
Heating System
Mains
Water
Supply
(Service
Pipe)
Hose Union
Temporary
Hose
Stop
Valve
Double
Check
Valve
Fig. 6