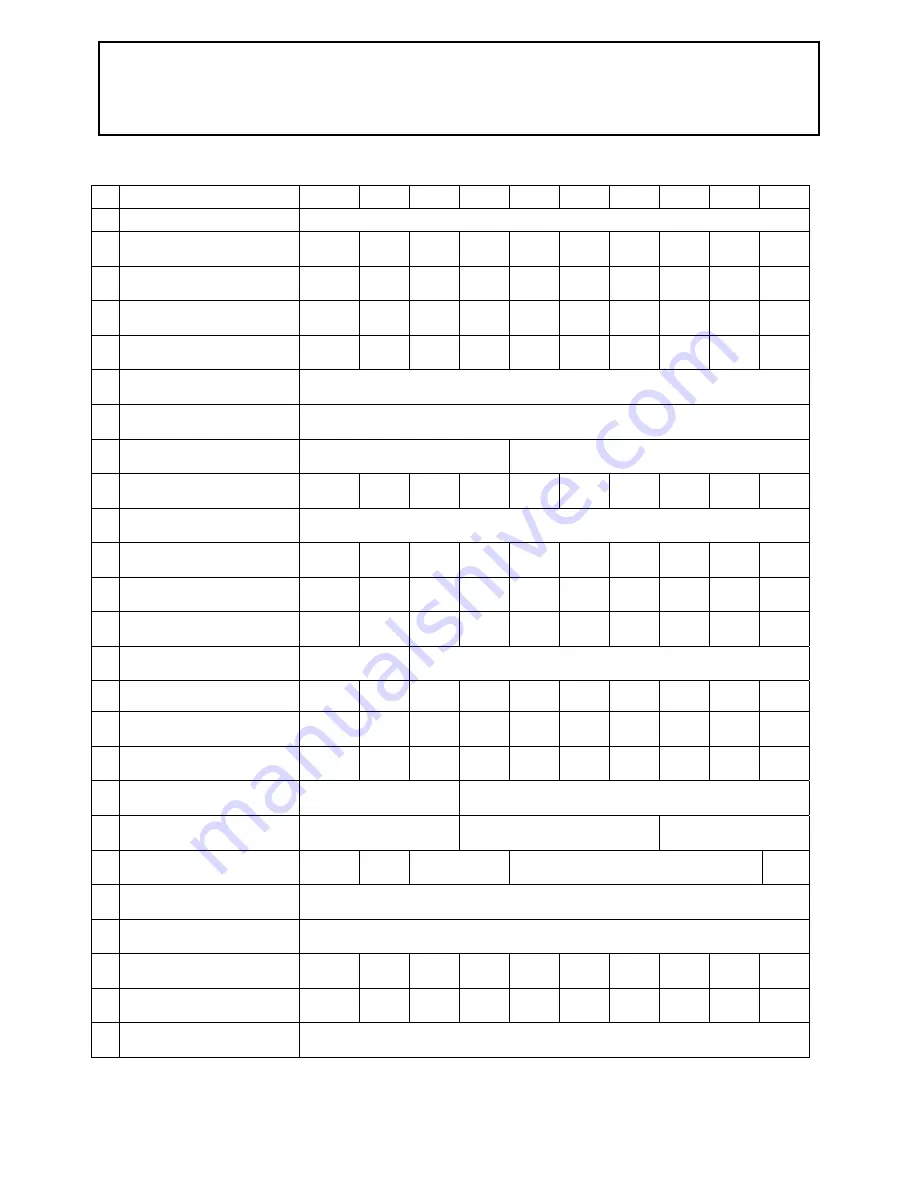
SECTION 1
POTTERTON COMMERCIAL PRODUCTS DIVISION
INSTALLATION, OPERATION & MAINTENANCE MANUAL
PAGE 2
ISIS HE
Table 3 – Technical Data
Number of Sections
6
7
8
9
10
11
12
13
14
15
CE Number
BG/EC87/97/127
Output kW
440
516
586
670
762
840
925
1000
1070
1172
Input (Gross)
GAS kW
OIL
kW
536
514
629
603
714
685
817
783
929
891
1024
982
1128
1082
1219
1169
1305
1251
1429
1370
Input (Net) GAS kW
OIL kW
483
482
567
566
643
642
736
734
837
836
922
921
1016
1015
1098
1096
1175
1173
1287
1285
1
Fuel
GAS m
3
/hr
Consumption
OIL
lit/hr
50
47.6
58.7
55.9
66.7
63.5
76.2
72.6
86.6
82.6
95.5
91
105.2
100.3
113.7
108.3
118.8
115.9
133.3
127
Maximum Design
Pressure
Bar
6 BAR ALL MODELS
2
Minimum Operating
Pressure
Bar
0.5 BAR ALL MODELS
3
Nominal Flue
Connection Size
250mm DIAMETER
350mm DIAMETER
4
Flue Gas Volume
m
3
/hr
656
770
874
999
1135
1252
1379
1491
1597
1748
Flue Draught Requirements
0 – 4 mm ALL MODELS
5
High Level Natural
Ventilation to BS 6644 cm
2
1342
1550
1742
1973
2225
2439
2673
2878
3070
3350
5
Low Ventilation Natural
Ventilation to BS 6644 cm
2
2684
3101
3485
3946
4451
4851
5346
5757
6141
6700
6
Mechanical Inlet to
BS 6644
m
3
/sec
0.482
0.566
0.644
0.735
0.836
0.922
1.02
1.097
1.175
1.286
7
Water Connection Size
(See Fig.3 & 4)
BSP
3''
4''
8
Water Flow
at 11°C
∆
t
lit/sec
9.5
11
12.6
14.5
16.5
18.2
20.1
21.7
23.2
25.4
8
Minimum Water Flow
at 11
o
C
∆
t lit/sec
5.2
6.1
6.9
8.0
9.1
10
11
11.9
12.8
14
8
Hydraulic Resistance
at 11°C
∆
t
kPa
2.8
4
5
6.5
8.2
11
13
14.5
15
21
9
Cold Feet Size to BS
6644 Minimum Bore
mm
38
50
9
Open Vent Size to BS
6644 Minimum Bore
mm
50
65
80
Safety Valve Size to BS
6644 Nominal Size
mm
32
40
50
65
80
2
Maximum
Flow Temperature
°C
90°C ALL MODELS
10
Minimum Return
Temperature
°C
55°C ALL MODELS
11 Dry Weight
kg
1460
1655
1850
2035
2230
2425
2620
2870
3065
3265
Water Content
kg
285
330
375
420
465
510
555
600
645
690
Power Requirements
415V ALL MODELS
For metric to imperial conversions refer to chart inside back cover
Summary of Contents for Isis HE
Page 1: ...MAY 2004 ...