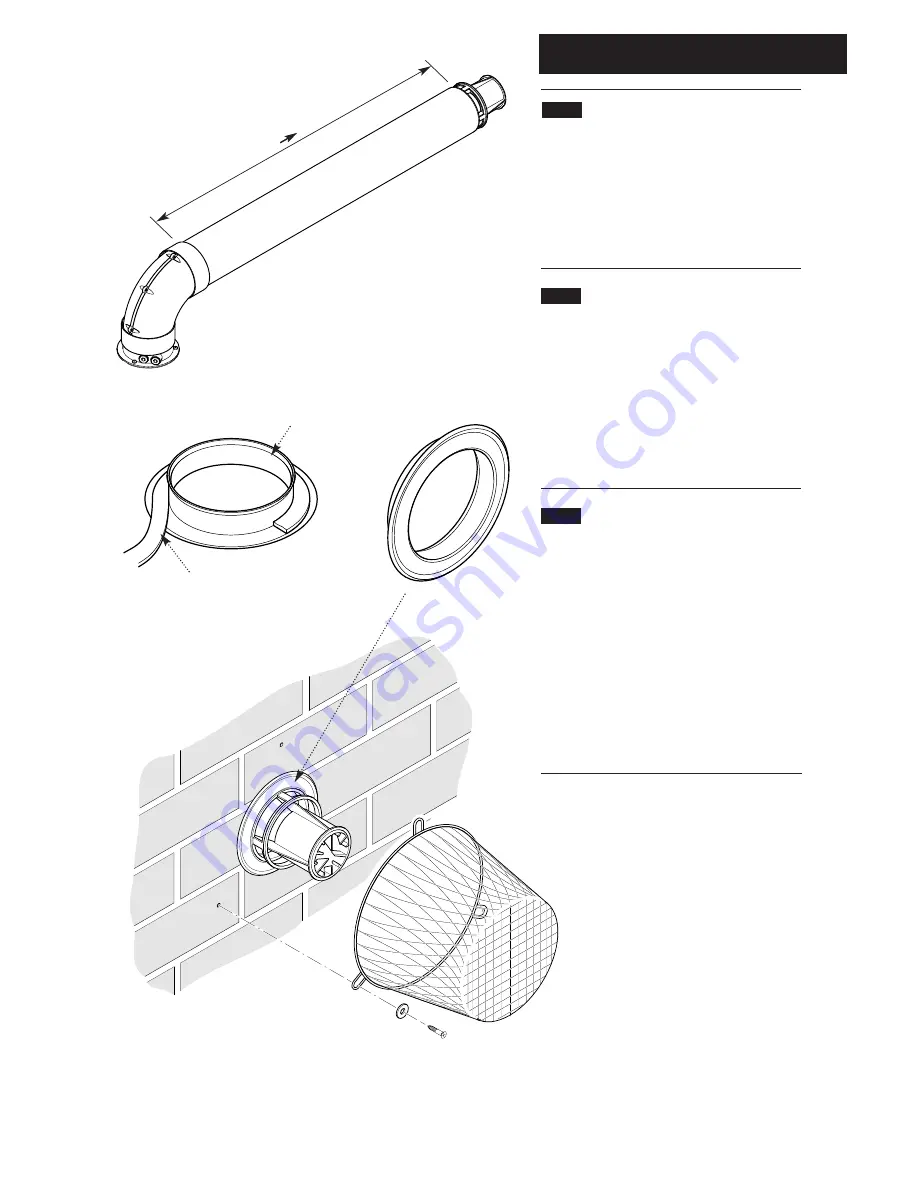
7.0 Site Requirements
17
7.9
Flue Dimensions
The standard horizontal flue kit allows for flue
lengths between 100mm and 1m from elbow to
terminal (Fig. 10).
The maximum permissible equivalent flue
length is:
System 12e,18e,24e
5 metres
System 28e
4 metres
7.10
Flue Terminal Trim
1. Once the flue is secure the trim can be fitted if
required.
2. Remove the protective backing from the
adhesive seal. Apply the seal to the rear of the
trim flange (Fig. 11).
3. Locate the trim over the flue terminal and push
it back to the wall to compress the seal (Fig. 12).
7.11
Terminal Guard
(Fig. 13)
1. When codes of practice dictate the use of
terminal guards, they can be obtained from most
Plumbers’ and Builders’ Merchants.
2. There must be a clearance of at least 50mm
between any part of the terminal and the guard.
3. When ordering a terminal guard, quote the
appliance name and model number.
4. The flue terminal guard should be positioned
centrally over the terminal and fixed as
illustrated.
Fig. 10
Fig. 13
100mm
1m
Fig. 12
Fig. 11
Flue Trim
Adhesive Seal
Summary of Contents for Performa System 12e
Page 42: ...16 0 Notes 42 ...
Page 43: ...16 0 Notes 43 ...