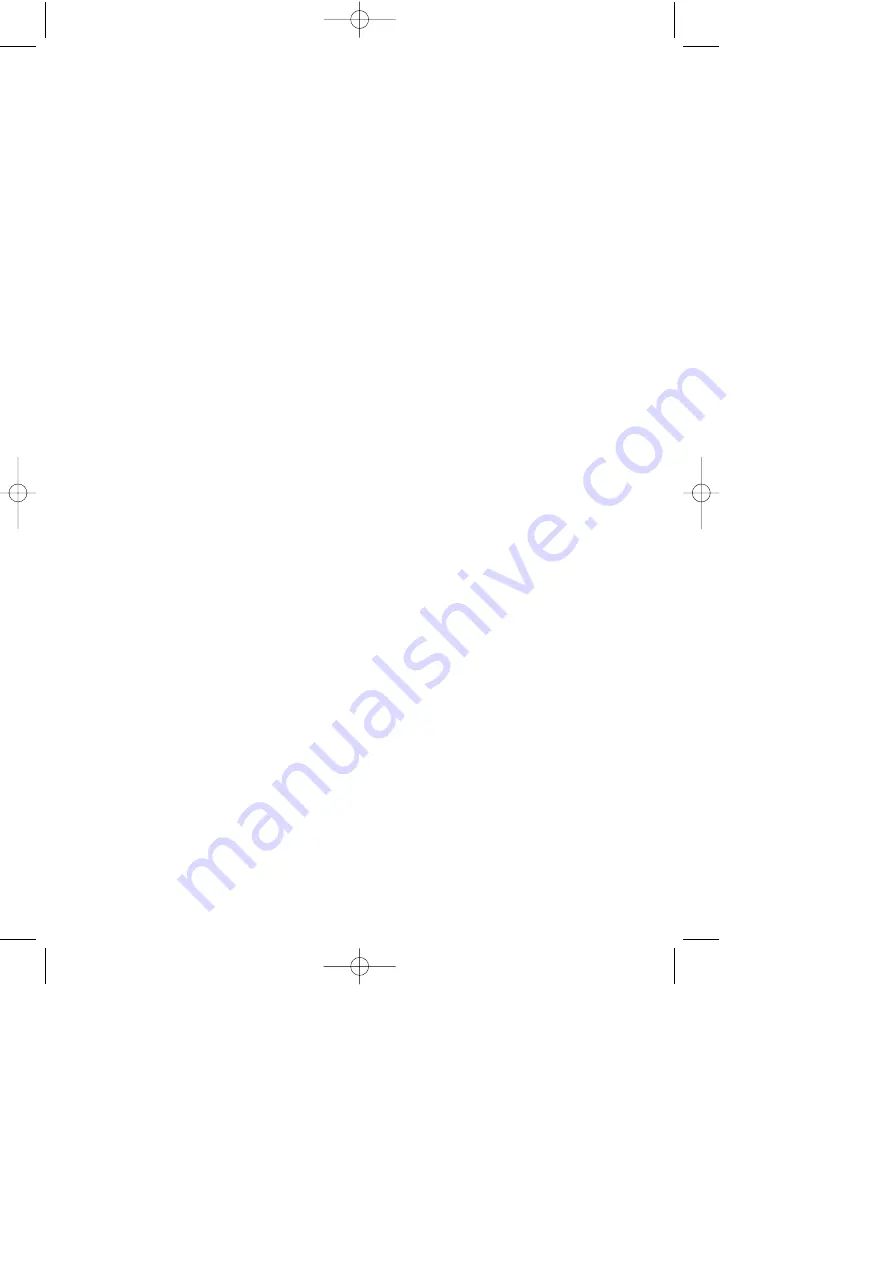
10
7.3 Precision adjustment of the stop for
crosscut 90° (Fig. 4/5)
Lower the machine head (4) and fasten in place
with the safety pin (16).
Loosen the tightening screw (13).
Place the angular stop (a) between the blade (5)
and the turntable (8).
Loosen the counternut and adjust the adjustment
screw (21) until the angle between the blade (5)
and the turntable (8) equals 90°.
Retighten the counternut to secure this setting.
Finally, check the position of the angle indicator
(23). If necessary, release the pointer with a
crosstip screwdriver, move to the 0° position of
the angle scale (15) and retighten the holding
screw.
7.4 Making 90° crosscuts with turntable
at 0° - 45° (Fig. 6)
With the PSMS 2100 you can make right and left
angular cuts from 0° - 45° to the stop rail.
Use the handle (2) to set the turntable (8) to the
desired angle i.e. the scale pointer (11) on the
turntable must coincide with the desired angular
setting (12) on the stationary base plate (9).
Re-tighten the locking handle (10) to lock the
turntable (8) into place.
Cut as described under section 7.2.
7.5 Mitre cuts 0°-45° and rotary table 0° (Fig. 4/7)
The PSMS 2100 can be used to make mitre cuts of
0°-45° relative to the machine bed on the left side.
Lift the machine head (4) to its top position.
Fix the rotary table (8) in 0° position.
Undo the locking nut (13) and, holding the handle
(2), tilt the machine head (4) to the left until the
pointer (23) coincides with the required angle
dimension (15).
Re-tighten the locking nut (13) and make the cut
as described in Section 7.2.
7.6 Precision adjustment of the stop for 45° mitre
cuts (Fig. 2/4/8)
Lower the machine head (4) and fix with the lock
pin (16).
Fix the rotary table (8) in 0° position.
Undo the locking nut (13) and, holding the handle
(2), tilt the machine head (4) to the left by 45°
Place the 45° stop angle (b) between the saw
blade (5) and the rotary table (8).
Slacken the counter nut and adjust the setting
screw (22) until the angle between the saw (5)
and the rotary table (8) equals exactly 45°.
Re-tighten the locking nut (13) and make the cut
as described in Section 7.2.
7.7 Mitre cuts 0°-45° and rotary table 0°-45°
(Fig. 4/9)
The PSMS 2100 can be used to make mitre cuts on
the left at an angle of 0°-45° relative to the work top
and 0°-45° relative to the stop rail.
Lift the machine head (4) to its top position.
Release the turntable (8) by loosening the locking
grip (10).
Adjust the rotary table (8) by its handle (2) to the
required angle (see also Section 7.4).
Re-tighten the locking handle (10) to fix the rotary
table in position.
Undo the clamping nut (13) and, holding the
handle (2), tilt the machine head (4) to the left to
the required angle dimension
(see also Section 7.5).
Re-tighten the locking nut (13) and make the cut
as described in Section 7.2.
7.8 Dust extraction (Fig. 1)
The saw is equipped with a dust collection bag (24).
The dust bag (24) can be emptied by opening the zip
fastener at the bottom.
7.9 Replacing the saw blade (Fig. 11)
Pull out the power plug.
Swing up the machine head (4).
Press the lever and swing up the saw blade
guard to the point where the recess in the saw
blade guard is above the flange bolt.
Press the saw shaft lock (17) with one hand while
holding the wrench (31) on the flange bolt with
the other.
Firmly press on the saw shaft lock (17) and
slowly rotate the flange bolt in clockwise
direction. The saw shaft lock engages after no
more than one rotation.
Now, using a little more force, slacken the flange
bolt in clockwise direction.
Turn the flange bolt until it is completely
removed.
Take the blade (5) off the inner flange and pull
out downwards.
Mount the new saw blade in reverse order and
fasten.
Important! The cutting bevel of the teeth, i.e. the
direction of rotation of the saw blade, has to
conform with the direction of the arrow marked on
the housing.
Clean the saw blade flanges thoroughly before
mounting the saw blade.
Reattach the movable blade guard (6) in reverse
order.
Before using the saw again, check that the safety
devices are in good working order.
Important: Every time that you change the saw
Anleitung PSMS 2100 SPK7:_ 25.01.2007 16:37 Uhr Seite 10