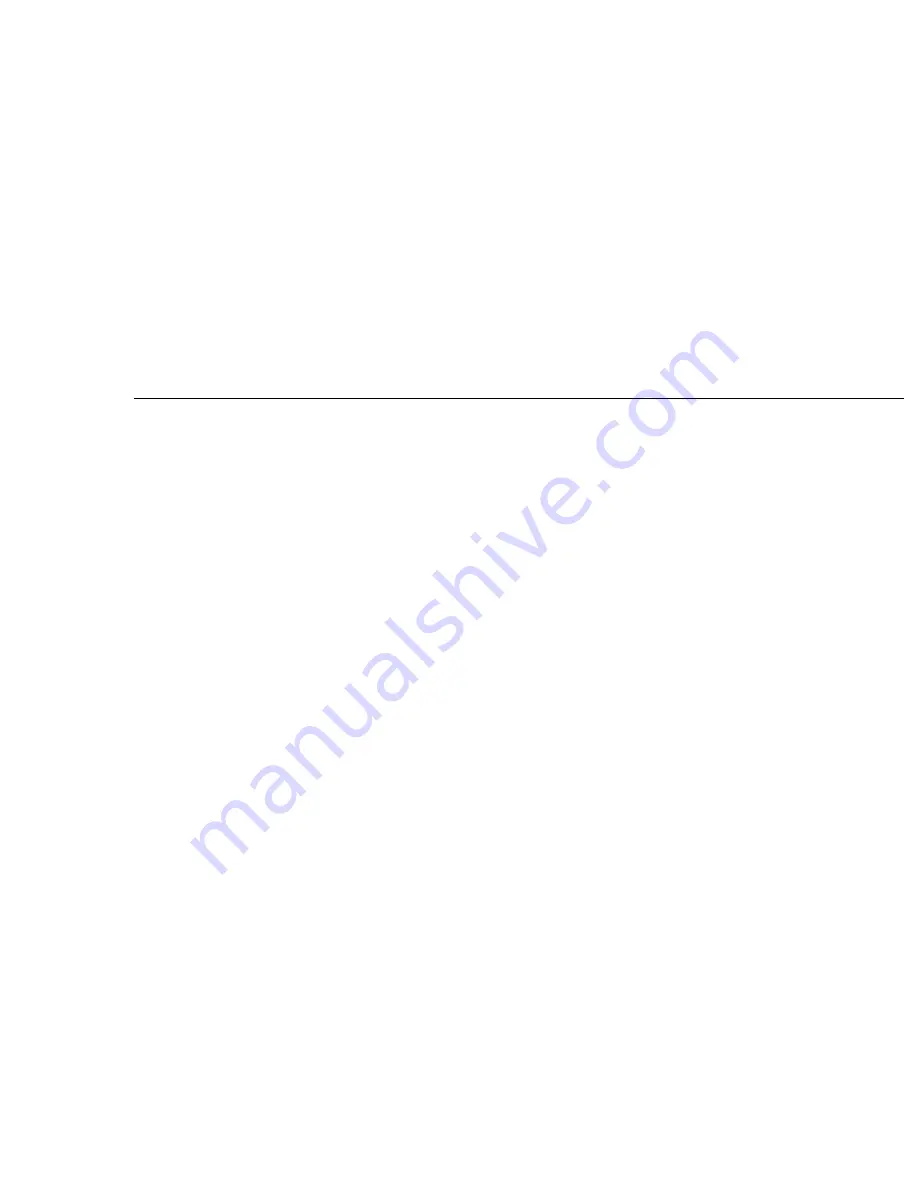
4. Gas High Fire Input Cannot Be Achieved
A. Gas company pressure regulator or meter
operating incorrectly, not allowing required gas
pressure at burner train inlet. Have gas company
correct.
B. Gas cock upstream of train inlet not fully open.
Check and correct.
C. Gas line obstructed. Check and correct.
D. Gas train main and/or leak test cocks not fully
open. Check and correct.
E. Gas supply line between gas company regulator
and burner inlet too small. Check supply pressure
at meter, determine pressure drop and increase
line size as required, or raise supply pressure to
compensate for small line. Do not raise pressure
so high that under static (no flow) conditions the
pressure exceeds the maximum allowable
pressure to the gas train components on the burner.
F. Burner gas train components sized too small for
supply pressure. Increase component size as
appropriate.
G. Automatic gas valve not opening fully due to
defective operation. Replace gas valve.
H. Side tee (limiting) orifice (if supplied) too small.
Replace with correct size.
I. On modulating burner, butterfly valve not fully
opened. Readjust.
J. Defective main gas pressure regulator. Replace.
K. Incorrect spring in main gas pressure regulator.
Replace as required.
L. Main gas pressure regulator vent line obstructed.
Check and correct.
M. Normally open vent valve (if supplied) not closing
when automatic gas valves open. Check to see if
valve is fully closed when automatic valves are
open. Replace vent valve, if not closing fully.
OIL OPERATION
1. Burner Motor Runs, but Direct Spark Ignited Oil
Flame is Not Established
A. Defective or incorrect size oil nozzle. Remove and
clean or replace.
B. Low oil pressure. Check with gauge for correct
light-off pressure.
C. Defective oil pump. Replace.
D. Defective oil solenoid valve. Replace.
E. Oil pump coupling loose or defective. Replace or
tighten as required.
F. Low oil pressure switch (if supplied) defective or
incorrectly set. Adjust or replace switch.
G. Ignition transformer defective. Replace.
H. Ignition electrode set incorrectly. Remove electrodes
and reset.
I. Ignition electrodes cracked and grounding out
spark. Replace electrodes.
J. Ignition leadwire defective and grounding spark out.
Replace.
K. Ignition plug in connections at transformer or
electrodes loose. Tighten.
L.. Air flow switch (if provided) not making. Reset
pressure or replace.
M. Defective flame safeguard control or plug in
purge timer card. Replace.
N. Air dampers held in high fire position due to
mechanical binding of linkage. Readjust linkage.
O. Loose wiring connections. Check and tighten all
connections.
2. Oil Flame Ignites, but then Flame Safeguard
Control Locks Out on Safety
A. Flame scanner lens dirty. Remove and clean.
B. Scanner sight tube blocked or dirty. Check and
clean.
C. Flame scanner defective. Replace.
D. Defective oil nozzle causing unstable flame and
scanning problems. Replace oil nozzle.
E. Fuel/air ratios incorrect, resulting in unstable or
smoky flame causing scanner flame sighting
problem. Readjust ratios for clean stable flame.
F. Defective flame safeguard amplifier or control.
Replace as appropriate.
3. Oil Flame Extremely Smoky at Light Off or in Low
Fire Position
A. Defective or incorrect size oil nozzle. Replace.
B. Fuel/air ratio incorrect. Readjust.
C. N.C. oil solenoid valve in oil nozzle return line not
opening. Check electrical circuitry and replace
valve if defective.
D. On two-step pump - N.O. pump mounted solenoid
valve malfunctioning. Replace valve or pump.
4. Light Off Oil Flame Is Established and Proven, but
Burner Will Not Attempt to Go to the High
Fire Position
A. Low/High/Low or Modulating burner high fire
temperature or pressure control could be
defective or not set to call for high fire. Readjust
or replace control.
B. Loose wires or incorrectly wired. Verify wiring and
tighten all connections.
C. Flame safeguard control or high fire panel
switching relay (if supplied) defective. Verify and
correct as required.
D. High fire 3 way solenoid valve defective. Replace.
E. Hydraulic oil cylinder defective. Replace.
F. On two-step pump - N.O. solenoid valve defective
(not closing). Replace pump or valve.
G. Linkage mechanically binding. Readjust linkage.
H. On modulating system - defective modulating
motor. Replace.
5. Low Oil Flame Is Established and Proven, but Flame
Out Occurs in Transition from Low Fire to High Fire
A. On Low/High/Off or Low/High/Low system - N.C.
oil solenoid valve in nozzle return line not closing
(or leaking). Check valve operation and replace
if necessary.
B. On two-step oil pump - N.O. solenoid valve
defective (not closing). Replace valve or pump.
C. Defective or incorrect size oil nozzle. Replace.
D. High fire oil pressure too low. Readjust.
E. Air dampers set too far open at low fire, which
causes flame to blow out in starting to high fire.
Readjust dampers.
F. Oil pump coupling loose or defective. Tighten or
replace.
G. Defective oil pump. Replace.
H. Linkage mechanically binding. Readjust.
I. Make certain the #72 orifice into the N.C. side of
the 3 way valve has not been removed.
J. On modulating systems - fuel/air ratios set
incorrectly, causing flame to blow out when
going to high fire. Readjust linkage.
C43
Rev.304
TROUbLE ShOOTING SUGGESTIONS
GAS, OIL OR GAS/OIL bURNER