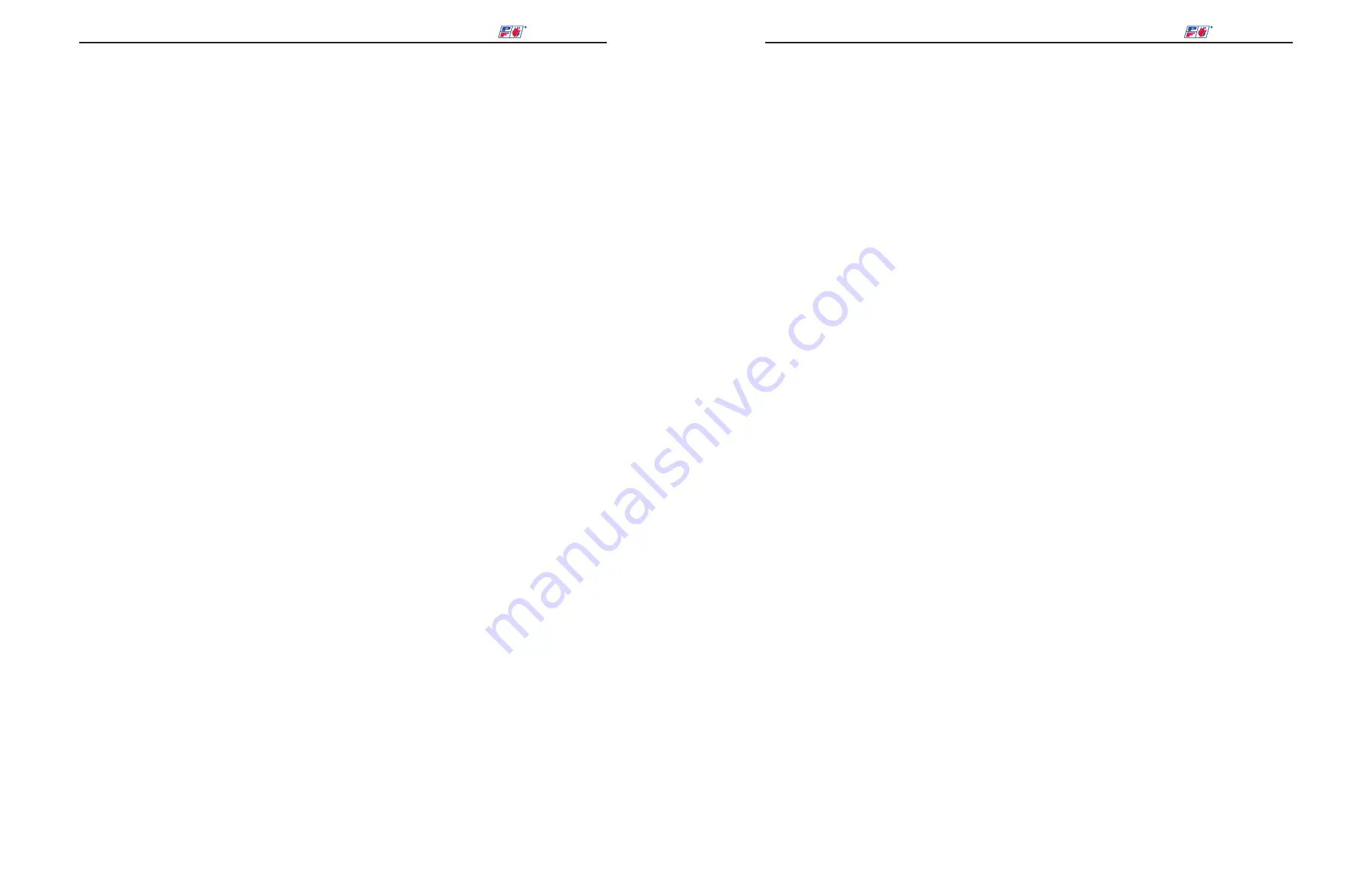
19
NOVA PLUS Installation & Operation Manual -
POWER FLAME INCORPORATED
DC4 DRAFT CONTROL
ENTER
ESC
®
16. MAINTENANCE
General Information
Only qualified service technicians should make mechanical or electrical adjustments to the
burner and/or associated control equipment.
Preventive maintenance can usually be performed by building maintenance or operating
personnel.
Always follow the information provided in the Owner Operating Instructions on
page 26.
These
should be conspicuously posted in the burner room at the time of the initial burner installation
and startup.
Always turn the power supply off to the burner and close manual fuel valves as appropriate for
routine maintenance.
Make sure that combustion and ventilation fresh air sources to the burner room remain clean
and open.
Periodically check all electrical connections and make sure the flame safeguard control chassis
is firmly connected to its wiring base.
Refer to manufacturer’s product bulletins supplied with the burner for maintenance on the flame
safeguard control and other components.
PERIODIC CHECK LIST
Item
Frequency
Checked By
Remarks
Gages, monitors and indicators
Daily
Operator
Make visual inspection and record
Readings in log
Combustion Air Filter
Daily
Operator
Make visual inspection of filter and indicator light
Instrument and equipment
Daily
Operator
Make visual check against heat exchanger
settings
manufacturer’s recommended specifications
Firing rate control
Weekly
Operator
Verify heat exchanger manufacture’s settings
Semiannually
Service Technician
Verify heat exchanger manufacture’s settings
Annually
Service Technician
Check with combustion test
Flue, vent, stack or outlet damper
Monthly
Operator
Make visual inspection of linkage, check for
Proper operation
Combustion air
Monthly
Operator
All sources remain clean and open
Ignition System
Weekly
Operator
Make visual inspection, check flame signal
Strength if meter-fitted
(see Combustion Safety Controls)
Fuel Valves
Pilot and main
Weekly
Operator
Open limit switch-make aural and visual check
Check valve position indicators and check
Fuel meters if so fitted
Pilot & main gas
Annually
Service Technician
Perform leakage tests – refer to valve
manufacturer’s instructions
Combustion safety controls
Flame failure
Weekly
Operator
Close manual fuel supply for (1) pilot, (2) main
fuel cock, and/or valve(s) check safety
shutdown timing; log
F.
Main gas pressure regulator atmospheric vent line obstructed. Correct.
G.
Defective main gas pressure regulator – replace. Misadjusted main gas pressure
regulator – readjust to meet required operational values.
5.
Carbon Monoxide Readings Too High
A.
Flame impingement on cold heat transfer surfaces caused by excessive firing
rate. Reduce firing rate to correct input volume.
B.
Flame impingement on cold combustion chamber surfaces due to undersized
combustion chamber. Refer to chamber size charts, page 10, and/or contact
factory for additional information.
C.
Incorrect gas/air ratios. Readjust burner to correct CO
2
/ O
2
levels, reducing CO
formation to appropriate level.
6.
High Fire Input Cannot Be Achieved
A.
Gas company pressure regulator or meter operating incorrectly, not allowing
required gas pressure at burner train inlet. Have gas company correct.
B.
Gas cock upstream of train inlet not fully open. Check and correct.
C.
Gas line obstructed. Check and correct.
D.
Gas train main and/or leak test cocks not fully open. Check and correct.
E.
Gas supply line between gas company regulator and burner inlet too small.
Check supply pressure at meter, determine pressure drop and increase line size
as required, or raise supply pressure to compensate for small line. Do not raise
pressure so high that under static (no flow) conditions the pressure exceeds the
maximum allowable pressure to the gas train components on the burner.
F.
Burner gas train components sized too small for supply pressure. Increase
component size as appropriate.
G.
Automatic gas valve not opening fully due to defective operation. Replace gas
valve.
H.
Butterfly valve not fully opened. Readjust.
I.
Defective main gas pressure regulator. Replace
J.
Incorrect spring in main gas pressure regulator. Replace as required.
K.
Main gas pressure regulator vent line obstructed. Check and correct.
L.
Normally open vent valve (if supplied) not closing when automatic gas valves
open. Check to see if valve is fully closed when automatic valves are open.
Replace vent valve, if not closing fully.
8
NOVA PLUS Installation & Operation Manual -
POWER FLAME INCORPORATED
DC4 DRAFT CONTROL
ENTER
ESC
®
11. GENERAL START UP PROCEDURES
General Start Up
A thoroughly qualified burner technician must be employed to provide the initial burner start up,
as well as any subsequent servicing of the burner and related controls.
A representative of the owner and/or the person or persons responsible for operating and
maintaining the unit should be present during the initial start up. A service representative may
also be required by the local utility on gas-fired equipment. Instructions regarding the proper
care and maintenance of the unit should be outlined with these people present.
Before initiating start up, the start up technician should thoroughly study and become completely
familiar with the exact sequence of operation and all other details of the specific flame
safeguard control system being used. This information will be found in bulletins printed and
supplied by Autoflame, Honeywell, Fireye, or Siemens. A copy of this bulletin is supplied with
the burner in the Owners/Installers Packet.
After the burner is mounted and all wiring and piping has been completed, tested and determined to
be correct, the following procedures are recommended:
1. Make a general inspection of the equipment room to ensure that the installation is complete.
Check piping, controls, wiring and etc.
2. Close main and checking gas cocks.
3. Tighten all screws on terminal blocks in control cabinet in case some may have loosened in
shipment.
4. Check fuses in main panel (if supplied) and in burner control cabinet. Check wiring to the
burner control cabinet for compliance with the wiring diagram and local codes. Determine that
voltage supply is correct to motor starter line connections and to control circuit line connections.
If a control circuit transformer is supplied, make certain its primary voltage matches the line
voltage being supplied. (A 230 volt transformer does not produce proper control voltage when
supplied with 208 volts).
5. Check breaching and stack to ensure that they are open and unobstructed.
6. Check blower rotation by momentarily making contact of the motor starters. Proper rotation is
imprinted on the fan housing.
7. Check operating controls, limit controls, low water cut-off, flame safeguard control reset, high
and low gas pressure switches (if used), low fire interlock switch (if used) and all other
applicable interlocks. All contacts should be closed (an exception will be found on jobs using
the low gas pressure switch; this switch should be open until the main gas cock is opened).
8. Do not repeatedly recycle the burner, as to allow any unburned fuel in the combustion chamber
to collect. Allow 5 minutes between recycles.
9. Specific instructions relative to component sequencing are provided in the flame safeguard
manufacturer’s bulletin which is included with the documentation shipped with the burner.