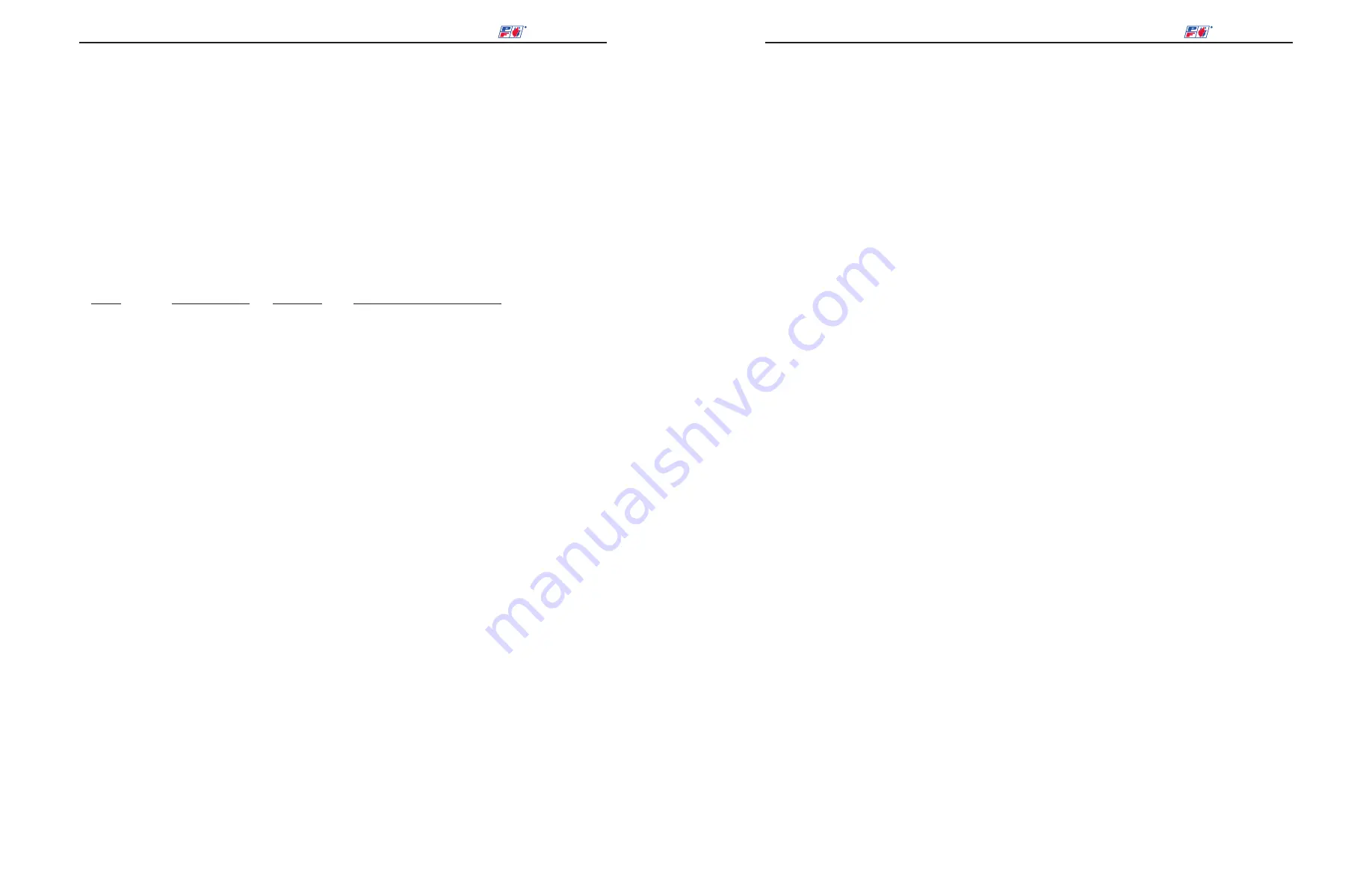
9
NOVA PLUS Installation & Operation Manual -
POWER FLAME INCORPORATED
DC4 DRAFT CONTROL
ENTER
ESC
®
10. Proper test equipment must be used in order to achieve maximum system operational reliability
and fuel efficiencies.
See page 10, item 12 for equipment lists.
11. All fuel/air adjustments should be made to achieve required input rate, satisfactory combustion
test values, flame stability and appearance. Before start up determine the burner’s manifold
pressure, see
Figure 5
, (Approximate High Fire Manifold Pressure). The pressures shown
(Total) are the approximate net pressure, therefore the heat exchanger’s over-fire pressure
must be added to these pressures for the total manifold pressure.
Figure 5
Approximate High Fire Manifold Pressures
Burner
Mixing Spool
Firing
Model
Orifice Qty/Size
Rate CFH
Or Element =
Total
NVC2
(8).313
2,000
3.86”
5”
8.8
”
NVC3 (20)
(8).344
2,500
4.17”
5”
9.1
”
NVC3 (25)
(8).375
3,000
4.24”
5”
9.2
”
NVC3 (25B)
(8).406
3,500
4.15”
5”
9.2
”
NVC4
(6).577, (6).531
5,000
1.16”
5”
6.2
”
NVC5A
(6).577, (6).531
5,520
1.42”
5”
6.4
”
NVC5
(6).577, (6).531
7,000
2.29”
5”
7.3
”
NVC6A
(6).577, (6).531
8,400
3.29”
5”
8.3”
NVC6
(6).577, (6).531
10,500
5.15”
5”
10.2
”
NVC7
(6).620, (6).531
12,600
5.85”
5”
10.9
”
NVC8
(6).620, (6).531
14,700
7.98”
5”
13.0
”
NVC9
(8).646, (8).625
16,800
3.98”
5”
9.0
”
NVC10A
(8).646, (8).625
18,860
5.00”
5”
10.0”
NVC10
(8).646, (8).625
21,000
6.21”
5”
11.2
”
NVC11
(8).646, (8).625
25,200
8.9”
5”
13.9
”
NVC12
(20).709
29,400
5.0”
5”
10.0
”
NVC13
(20).709
33,600
6.58”
5”
11.6
”
NVC14
(16).834
37,800
6.8”
5”
11.8
”
NVC15
(16).834
42,000
8.45”
5”
13.5
”
NVC16
(16).834
50,400
12.16”
5”
17.1
”
NVC17
(16).834
63,000
19.01”
5”
24.0
”
12. Every new burner startup should employ the use of the Burner Start Up Information and Test
Data sheets on
page 22.
The gas system uses two motorized gas shutoff valves to control the on/off flow of the gas. A
modulating motor or servo motor (depending on the control scheme) controls the positioning of
a butterfly type Gas Proportioning Valve. When the modulating motor is employed it also
controls the positioning of the combustion air dampers, while a second servo will control the air
dampers when servos are used.
18
NOVA PLUS Installation & Operation Manual -
POWER FLAME INCORPORATED
DC4 DRAFT CONTROL
ENTER
ESC
®
F.
Main gas pressure regulator atmospheric vent line obstructed. Correct.
G.
Defective main gas pressure regulator – replace. Misadjusted main gas pressure
regulator – readjust to meet required operational values.
5.
Carbon Monoxide Readings Too High
A.
Flame impingement on cold heat transfer surfaces caused by excessive firing
rate. Reduce firing rate to correct input volume.
B.
Flame impingement on cold combustion chamber surfaces due to undersized
combustion chamber. Refer to chamber size charts, page 10, and/or contact
factory for additional information.
C.
Incorrect gas/air ratios. Readjust burner to correct CO
2
/ O
2
levels, reducing CO
formation to appropriate level.
6.
High Fire Input Cannot Be Achieved
A.
Gas company pressure regulator or meter operating incorrectly, not allowing
required gas pressure at burner train inlet. Have gas company correct.
B.
Gas cock upstream of train inlet not fully open. Check and correct.
C.
Gas line obstructed. Check and correct.
D.
Gas train main and/or leak test cocks not fully open. Check and correct.
E.
Gas supply line between gas company regulator and burner inlet too small.
Check supply pressure at meter, determine pressure drop and increase line size
as required, or raise supply pressure to compensate for small line. Do not raise
pressure so high that under static (no flow) conditions the pressure exceeds the
maximum allowable pressure to the gas train components on the burner.
F.
Burner gas train components sized too small for supply pressure. Increase
component size as appropriate.
G.
Automatic gas valve not opening fully due to defective operation. Replace gas
valve.
H.
Butterfly valve not fully opened. Readjust.
I.
Defective main gas pressure regulator. Replace
J.
Incorrect spring in main gas pressure regulator. Replace as required.
K.
Main gas pressure regulator vent line obstructed. Check and correct.
L.
Normally open vent valve (if supplied) not closing when automatic gas valves
open. Check to see if valve is fully closed when automatic valves are open.
Replace vent valve, if not closing fully.
E.
Occasional low voltage supply. Have local utility correct. Make certain that the
burner control circuit transformer (if supplied) is correct for the voltage being
supplied.
F.
Occasional low gas supply pressure. Have utility correct.
G.
Element air pressure switch opens during purge. Reset switch to remain closed
just under maximum purge pressure.
3.
Burner Motor Runs, but Pilot Does Not Light
A.
Gas supply to burner shut off – make sure all manual gas supply valves are
open. Automatic high pressure valve at meter such as Sentry type tripped shut
due to high gas pressure – reset valve and correct cause for trip out.
B.
Pilot solenoid valve not opening – listen and feel for valve actuation. Solenoid
valve not being powered – check electrical circuitry. Replace coil or entire valve
if coil is burned out.
C.
Defective gas pilot regulator – replace.
D.
Gas pressure too high or too low at pilot orifice. Check orifice size in gas pilot
assembly. Replace if incorrect. Refer to gas pilot adjustments for correct
settings. Readjust as required.
E.
Defective ignition transformer – replace. Incorrect ignition electrode settings –
refer to gas pilot adjustments for correct settings.
F.
Defective flame safeguard control or plug in purge timing card. Replace as
required.
G.
Air flow switch not making circuit – check out electrically and correct pressure
adjustment on switch, if required. Defective air flow switch – replace. Air switch
negative pressure sensing tube out of position – reposition as necessary.
4.
Burner Motor Runs and Pilot Lights, but Main Gas Flame Is Not Established
A.
Main shutoff or test cock closed. Check to make certain fully open.
B.
Pilot flame signal reading too low to pull in flame safeguard relay. Refer to gas
pilot settings section and readjust as required.
C.
Defective automatic main or auxiliary gas shut off valves. Check electrical
circuitry to valves. Replace valves or correct circuitry as required.
D.
Defective flame safeguard control or plug in amplifier. Check and replace as
required.
E.
Butterfly valve set incorrectly on modulating burner. Readjust as required.