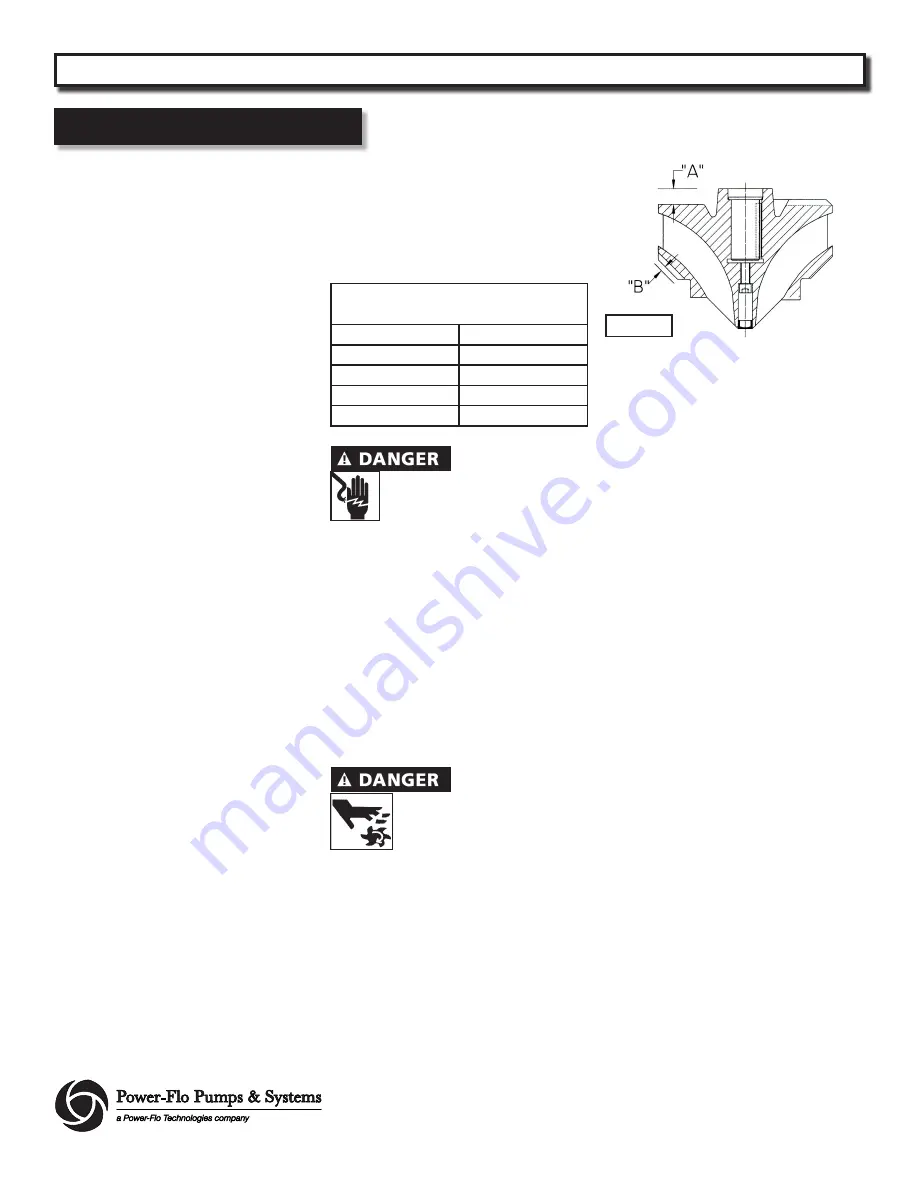
18
Power-Flo Pumps & Systems • 877-24PUMPS • www.powerflopumps.com
Maintenance
No lubrication or maintenance is required.
Perform the following checks when pump
is removed from operation or when pump
performance deteriorates:
a). Inspect seal chamber for oil level
and contamination.
b). Inspect impeller, adjust cutter knife
and blade.
c). Inspect motor and bearings.
d). Inspect lower seal for wear or leakage.
Servicing
NOTE: Item numbers in ( ) refer to Figures
6 & 7.
Seal Chamber Oil -
Anytime the pump
is removed from operation, the oil in the
seal chamber should be checked visually
for oil level and contamination.
To check oil, set unit on its side with pipe
plug (23) downward, remove pipe plug
(23) and drain oil from seal chamber.
Make sure it is clean and clear, light
amber in color and free from suspended
particles. Milky white oil indicates the
presence of water and lower seal should
be inspected or replaced.
Oil Testing
• Check oil for contamination using an
oil tester with a range to 30 Kilovolts
breakdown.
• If oil is found to be clean and
uncontaminated (measuring above
15 KV. breakdown), refill seal chamber.
• If oil is found to be dirty or
contaminated (or measures below
15 KV. breakdown), the pump must
be carefully inspected for leaks.
After leak is repaired, dispose of old oil
properly, and refill with new oil.
Oil Replacement:
Seal Chamber -
Drain all oil (if not already
done so) from seal chamber and dispose
of properly per Local and Environmental
Standards. Refill with approx. 51 oz. with
new oil, see chart.
Cooling Oil
Recommended Supplier/Grade
BP
Enerpar SE100
Conoco
Pale Paraffin 22
Mobile
D.T.E. Oil Light
Shell Canada
Transformer-10
Texaco
Diala-Oil-AX
Before any service
work is done,
disconnect and lock out
electrical power to pump.
Disassembly
Cutter & Impeller -
Remove cap screws
(45) and washer (47) from volute (40). Lift
motor from volute (40). Clean out volute
and check impeller for pitting or wear. To
replace impeller (41), remove plug (50),
screw (48) and washer (49). Pull impeller
straight off shaft with a wheel puller.
Carefully remove impeller (41) so as not to
damage the lower seal.
NOTE:
Seal spring
relaxes when impeller is removed and may
cause oil to leak through.
Impeller and knife
assemblies are
EXTREMELY SHARP
!
Handle with care.
To install impeller, check that lower seal is
in place, apply a thin film of oil to motor
shaft and slide impeller straight onto
shaft. Apply thread locking compound to
screw (45), and with washwe (11) place
into shaft and tighten. Check impeller for
binding. Assemble volute (40) onto motor
assembly with screws (45) and washers
(47). Apply thread locking compound on
screws (45).
Check the gap (A) between the intermediate
and upper portion of impeller with a feeler
gauge which should be between .012” -
.059”. Gap (B) between the lower portion
of impeller and volute should be between
.012” - .059”. See Figure 3.
Cutter Height Adjustment -
Loosen two
screws (51) and bring the upper surface of
the blade as close as possible to the lower
heel of the impeller without touching and
tighten firmly.
Cutter Angle Adjustment
- Loosen two
screws (45) and move the knife (42) across
so as to bring blade flush up to the point
of the impeller, permitted play between
.002” - .005” and tighten firmly.
Cable Assembly -
Loosen cable
connectors (32) and (35), replace if
required. Remove cap screws (19),
washers (20) and cable box cover (5) from
motor housing (1). Remove cable lead
wires from motor lead wires and sensor
wires from control cable by unscrewing
connectors (31) and (32). Note wiring
connections for reassembly. Remove
screw (26), washer (27) and ground wire
(30) from cover plate (5).
Service
PF4SCC, 4SCD, 4SCE, 4SCF
Submersible Cutter Pumps
Figure 3