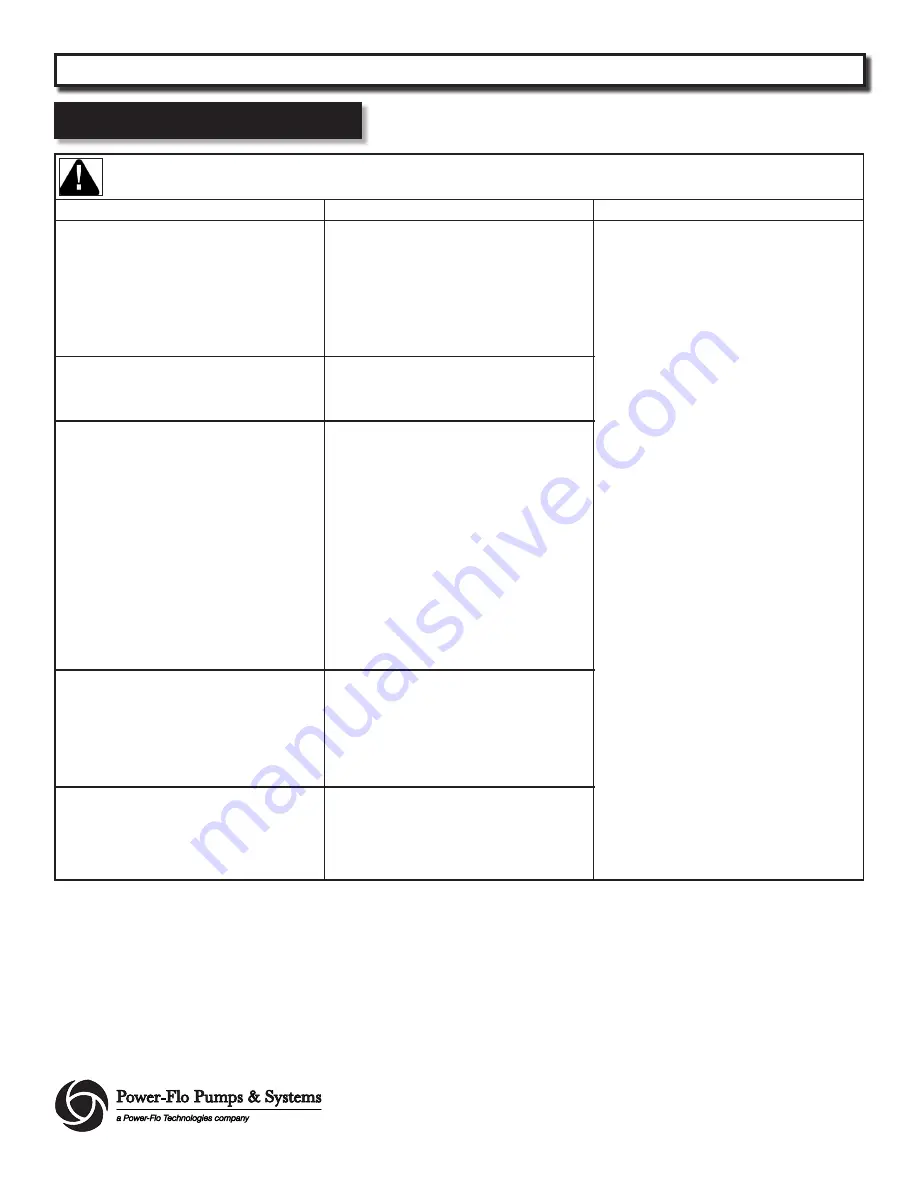
18
Power-Flo Pumps & Systems • 877-24PUMPS • www.powerflopumps.com
Risk of electric shock. Always disconnect the pump from the power source before handling inspections or repairs.
Symptom
Possible Cause(s)
Corrective Action
Pump will not run or pump fluid
1. Poor electrical connection, blown fuse, tripped
breaker or other interruption of power;
improper power supply
2. Defective motor
3. Insufficient liquid level
13. Debris plugging screen and suction intake
1. Check all electrical connections for security.
Have electrician measure current in motor leads,
if current is within ± 20% of locked rotor Amps,
impeller is probably locked. If current is 0,
overload may be tripped. Remove power, allow
pump to cool, then re-check current.
2. Check winding insulation (Megger Test) and
winding resistance. If check is outside of range,
dry and re-check. If still defective, replace per
service instructions.
3. Make sure liquid level is above the pump
4. Re-check all sizing calculations to determine
proper pump size.
5. Check discharge line for restrictions, including
ice if line passes through or into cold areas.
6. Remove and examine check valve for proper
installation and freedom of operation
7. Open valve
8. Check impeller for freedom of operation,
security and condition. Clean impeller cavity
and inlet of any obstruction
9. Loosen union slightly to allow trapped air to
escape.
10. Repair fixtures as required to eliminate leakage
11. Check pump temperature limits and fluid
temperature
12. Replace portion of discharge pipe with flexible
connector or tighten existing piping.
13. Check screen and/or suction inlet.
Pump hums but doesn’t run
1. Incorrect low voltage
8. Impeller jammed or loose on shaft, or inlet
plugged
Pump delivers insufficient capacity
1. Incorrect low voltage
4. Ecessive inflow or pump not properly sized for
application
5. Discharge restricted
6. Check valve partially closed or installed backwards
7. Shut-off valve closed
8. Impeller jammed or loose on shaft, or inlet
plugged
9. Pump may be air locked causing pump not to flow
10. Piping fixtures leaking or discharge before the
nozzle
13. Suction restricted
Pump shuts off and turns on independent of
switch, (trips thermal overload protector).
CAUTION!
Pump may start unexpectedly.
Disconnect power supply.
1. Incorrect low voltage
4. Ecessive inflow or pump not properly sized for
application
8. Impeller jammed or loose on shaft, or inlet
plugged
11. Excessive water temperature
Pump operates noisily or vibrates excessively
2. Worn bearings, motor shaft bent
8. Debris in impeller cavity or broken impeller
12. Piping attachments to building structure too
loose or rigid
NOTE:
Power-Flo Pumps & Systems assumes no responsibility for damage or injury due to disassembly in the field. Disassembly of the pumps or supplied
accessories other than at Power-Flo Pumps & Systems or its authorized service centers, automatically voids warranty.
Trouble Shooting Chart
PFU31, PFU51, PFU71, PFU102, PFU152, PFU202
Submersible Fountain Pumps