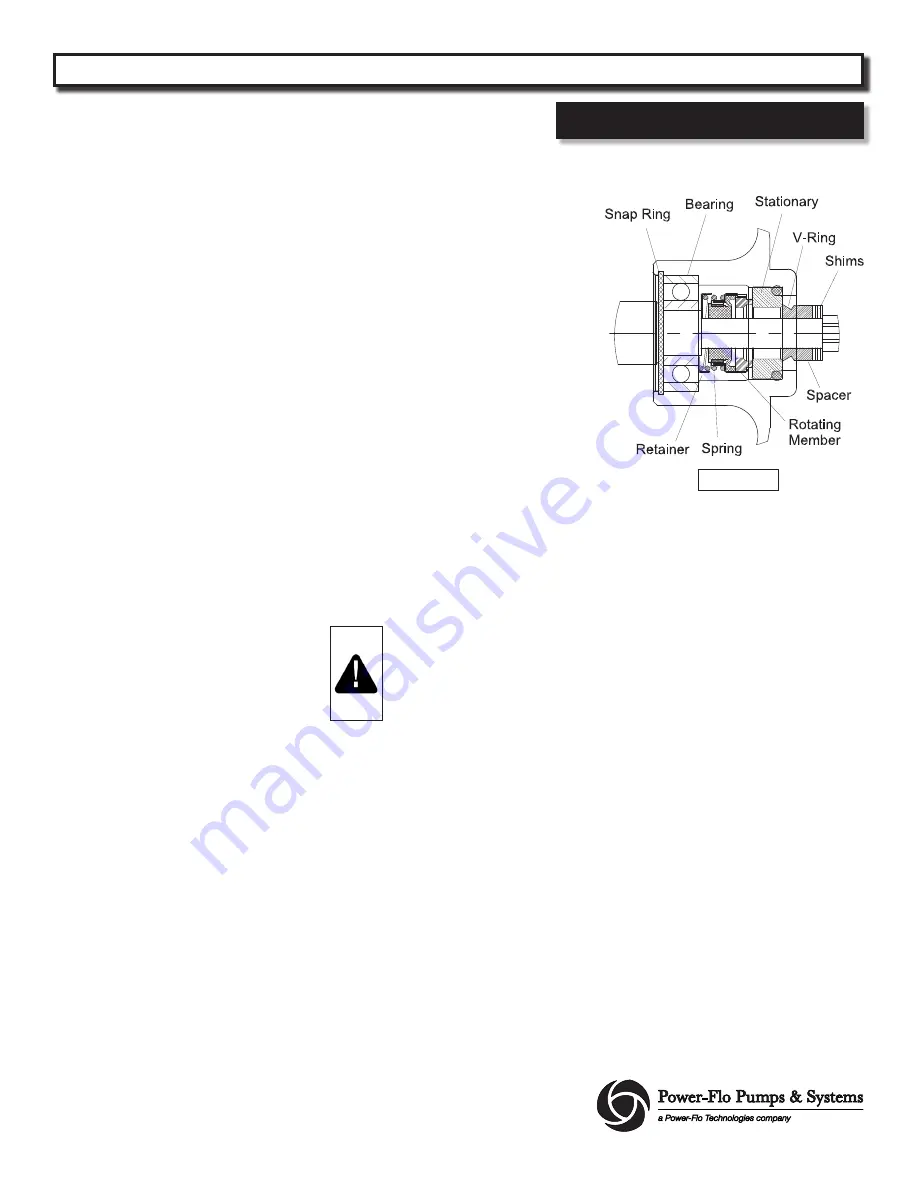
9
Power-Flo Pumps & Systems • 877-24PUMPS • www.powerflopumps.com
Disassembly & Assembly
Impeller and Volute:
Disconnect power. Disconnect discharge
piping. Remove screen (14) by removing
springs (33) and lifting off. Remove cap
screws (29) and pull volute (1) and gasket
from bearing sleeve (9). Remove set screw
(3), unscrew counter-clockwise impeller
(2) from motor shaft. Replace impeller if
worn or pitted.
Reassemble by placing shims (5) on shaft,
to ensure proper clearance between
impeller (2) and bearing sleeve (9). The
clearance should be approximately .03
inches. Screw impeller (2) clockwise onto
shaft and place set screw (3) in place and
tighten. Place gasket (30) and volute (1)
onto bearing sleeve (9) and insert cap
screws in place and tighten. Replace
screen (14) with springs (33).
IMPORTANT:
For units Dated Jan. 2011 and newer, with
Ball Bearing Design, continue on.
For unites prior to Jan. 2011 with sleeve
design, see pages 11 through 14.
Motor & Shaft Seal:
Remove screen, volute and impeller
as previously stated and drain oil from
housing. Loosen gland nut (17) and slide
it back on cord (18). Remove hex nuts
(20) and lockwashers (21) from studs (28)
and pull housing end (19) from housing
tube (27). Disconnect cord set (18) and
check for damage or cracks, replace if
required. Remove grommet (15), friction
rings (16) from housing end (19), replace
if damaged. Pull housing tube (27) from
bearing sleeve (9). Remove seal spacer
(31) and v-ring (6) from shaft. Loosen
motor screws and pull bearing sleeve (9)
with shaft seal (8) from motor.
IMPORTANT
that you mark location of
overload in relation to bearing sleeve
(9). Remove retaining ring (7) and press
seal assembly (8) out of bearing sleeve.
Replace complete seal if seal shows
signs of uneven wear on seal faces,
chips, or scratches. If replacing seal,
remove stationary by prying out with flat
screwdrive.
Examine o-rings (23) and replace if
damaged. Check motor capacitor (12)
with an Ohm meter by first grounding
the capacitor by placing a screwdriver
across both terminals and then removing
screwdriver. Connect Ohm meter (set
on high scale) to terminals. If needle
moves to infinity (
∞
) then drifts back, the
capacitor is good. If needle does not move
or moves to infinity (
∞
) and does not
drift back, replace capacitor (12). Inspect
motor winding for shorts and check
resistance values. Check rotor for wear. If
rotor or the stator windings are defective,
the complete motor must be replaced.
To test the overload, check the continuity
between the black and white wires.
IMPORTANT! - All parts must be
clean before reassembly.
Handle seal parts with extreme
care. DO NOT damage lapped
surfaces.
To reassemble, clean seal cavity in bearing
sleeve (9) and oil. Lightly oil stationary
member of seal, and with lapped surface
facing motor, press stationary member
with seal pusher tool into bearing sleeve
(9).
Lightly oil
(Do not use grease)
inner
surface of rotating member. With the
lapped surface facing inward, place
rotating member into bearing sleeve (9)
until it seats against stationary member.
Place the spring and retaining ring onto
rotating member. Press bearing (39) into
bearing sleeve (9) and snap ring (7) into
bearing sleeve (9).
Lightly oil
(Do not use grease)
the shaft
on motor (10). Assemble bearing sleeve
(9) onto motor (10), being carfull not to
damage seal. locate overload as noted (or
at the 11 o’clock position as viewed from
motor end), with the four motor bolts.
Place capacitor (12) into bracket (25) if
removed and secure with screw. Connect
flag terminal from motor and terminal
boot (13) to capacitor (12).
Place one o-ring (23) into groove on
bearing sleeve (9) being careful not to
damage the o-ring. Slide housing tube
(27) onto bearing sleeve (9). Place o-ring
(23) into groove on housing end piece
(19) and place end piece onto housing
tube (27). Place pump support (22) onto
lower studs (28) and lockwashers (21) and
hex nuts (20) onto studs and tighten.
Place v-ring (6) and seal spacer (31) onto
shaft until seated. Assemble sceen, volute
and impeller as described.
Service
Figure 1
PFU31, PFU51, PFU71, PFU102, PFU152, PFU202
Submersible Fountain Pumps