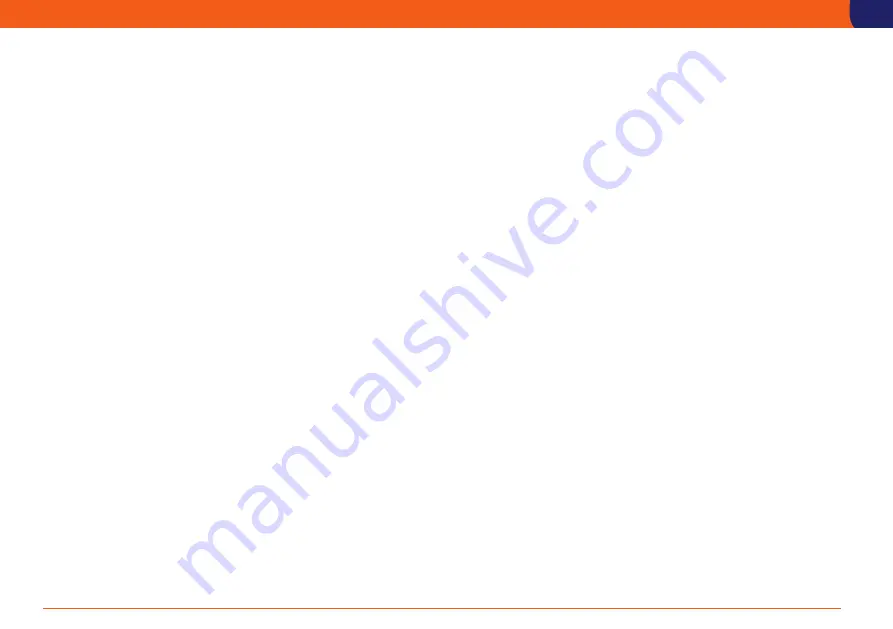
PRE-OPERATION CHECKS
Before operating the Nano SP the operator should check that the
working area is suitable for the machine. The ground should be
suitable to take the total weight of the Nano SP plus payload (i.e.
478kg + 200kg): a hard level surface is required e.g. concrete, tiled
flooring, adequately supported laminate flooring, raised access
flooring (medium duty). If unsure check floor specifications before use.
The ground should be free from debris and the operator should
beware of holes, hatches, pits, unprotected manholes, drains etc.
The work area should be cordoned off in a way to prevent inadvertent
collision with other personnel, plant or vehicles working in the area.
Check there are no live electrical cables or conductors that the
operator could come close to or into contact with when carrying out
tasks. Check there are no overhead obstructions likely to cause the
operator or the Nano SP danger.
A. Visual Inspection
Carry out a thorough visual inspection of the machine.
Look specifically for any signs of damage to:
1. Handrails, platform deck, cantilever deck and operation.
2. Lifting mast structure, chassis area structure.
3. Pothole mechanism.
4. Wheels and castors, for tyre damage and fixings.
5. Main control cable (curly cable to control arm).
6. All of the key fixings are intact and tight.
7. Check all instruction, information and safety decals are
affixed and are legible.
B. Ensure battery is charged by checking joystick LED light
(green = charged).
C. Ensure hydraulic oil level is at correct level. Do not over fill.
Check for hydraulic leaks.
D. Check Nano SP functions are working correctly
before normal use:
1. check lift functions at ground and in basket by lifting
approx.
0.5m;
2. check emergency lowering functions at ground
and in basket by lifting 0.5m;
3. check pothole mechanism and
interlock work correctly by lifting 0.5m;
4. check emergency stop functions at ground
and in basket.
Check drive and steer functions work correctly by selecting slow
speed in closed position first, followed by fast speed. Check automatic
elevated drive speed is engaged by elevating approx. 0.5m. Then
select drive; the joystick right-hand mode light (orange or green)
should be flashing and drive speed should be slightly slower than
slow closed speed. Check machine brakes when joystick is released.
OPERATING PROCEDURES
7