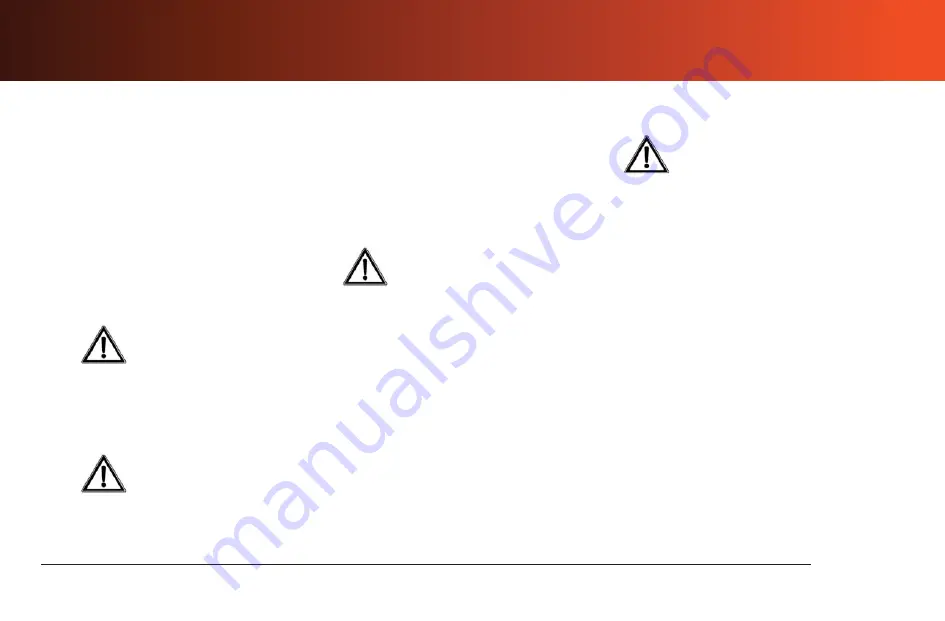
Page 27
PowerBoss
®
5.4.1 Charging The Batteries
Use the integrated battery charger
(Fig.7/3) to charge batteries. Proceed
to connect the charger to an AC outlet
by the integrated cord (Fig. 7/4) with
safety plug. Charging batteries is
recommended if at least one bar of
the LDS display has extinguished
after operation of the machine. You
are required to observe the operating
instructions of the charger as well as
the operating instructions of the battery
manufacturer.
Charge the batteries properly
before starting the machine
for the fi rst time. PowerBoss
cannot be held liable for
battery damage resulting
from failure to initiallly charge
batteries.
Provide suffi cient ventilation
of areas where batteries
are being charged.
Explosion hazard
5.4.2 Low Discharge Signal Sender (LDS)
The machine has been equipped with a
charge indicator to prevent the batteries
from low discharge. This low discharge
signal sender has been integrated into the
electronics. If other batteries are used,
readjustment of the low discharge signal
sender is required.
Only PowerBoss contract
workshops are authorized to make
adjustments to the low discharge
signal sender.
5.4.3 Removing Batteries
1. Park machine on level ground.
2. Switch off machine by key switch.
3. Open empty dirty water tank (Fig.7/7)
and secure with support (Fig. 7/8).
4. Disconnect battery plug (Fig. 7/5).
5. Disconnect battery connection cables.
6. Remove batteries
5.4.4 Installing Batteries
Do not make changes to the center
of gravity. Only use batteries as
recommended at the prescribed
position.
1. Turn off machine by the ignition switch.
2. Open empty dirty water tank (Fig.7/7) and
secure by support (Fig. 7/8).
3. Place batteries into holder according to
fi gure.
4. Connect battery poles and enclosed
connecting cables according to wiring
diagram (Fig.7/9). Provide for tight fi tting
and grease poles.
5.4.5 Disposal of Batteries
Used batteries labeled with the recycling
sign contain reusable substances, such
batteries must not be added to normal
household waste.