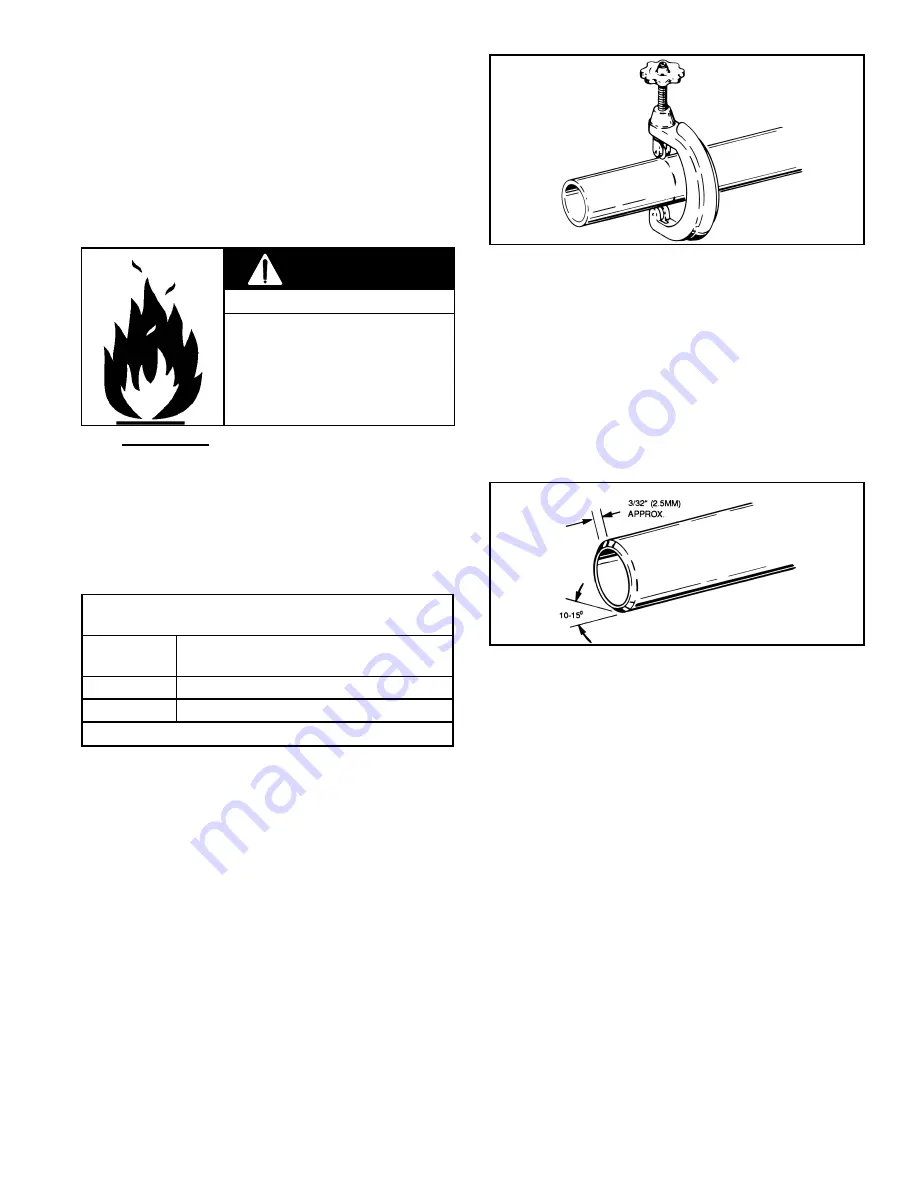
The cement should be a bodied cement of
approximately 500 to 1600 centipoise viscosity
containing 10-20% (by weight) virgin PVC material
solvated with Tetrahydrofuran (THF). Small
quantities of Dimethyl Formamide (DMF) may
be included to act as a retarding agent to extend
curing time. Select the proper cement; Schedule
40 cement should be used for Schedule 40 pipe.
Never use all-purpose cements, commercial glues
and adhesives or ABS cement to join PVC or CPVC
pipe and
fi
ttings.
•
Primers and cements are
extremely flammable, and must
not be stored or used near heat
or open flame.
•
Also, use only in a well venti-
lated area.
Fire Hazard
WARNING
Applicators:
Select a suitable pure bristle type paint brush. Use
a proper width brush or roller to apply the primer
and cement (see chart below). Speedy application
of cement is important due to its fast drying
characteristics. IMPORTANT NOTE: A dauber type
applicator should only be used on pipe sizes 2” and
below. For larger diameter pipe, a brush or roller
must be used.
RECOMMENDED BRUSH* SIZE FOR
PRIMER AND CEMENT APPLICATIONS
Nominal
Pipe (IPS)
Brush Size
2
1.5”
3
1.5” - 2.5”
*USE ONLY NATURAL BRISTLE
Table 3.
3. MAKING THE JOINT
A. Cutting
Pipe must be squarely cut to allow for the proper
interfacing of the pipe end and the
fi
tting socket
bottom. This can be accomplished with a miter box
saw or wheel type cutter. Wheel type cutters are not
generally recommended for larger diameters since
they tend to
fl
are the corner of the pipe end. If this
type of cutter is used, the
fl
are on the end must be
completely removed.
Note:
Power saws, if used, should be speci
fi
cally
designed to cut plastic pipe.
Figure 43.
B. Deburring
Use a knife, plastic pipe deburring tool, or
fi
le to
remove burrs from the end of small diameter pipe.
Be sure to remove all burrs from around the inside
as well as the outside of the pipe. A slight chamfer
(bevel) of about 10°-15° should be added to the end
to permit easier insertion of the pipe into the end of
the
fi
tting. Failure to chamfer the edge of the pipe
may remove cement from the
fi
tting socket, causing
the joint to leak.
Figure 44.
C. Test dry
fi
t of the joint
Tapered fitting sockets are designed so that
an interfaced
fi
t should occur when the pipe is
inserted about 1/3 to 2/3 of the way into the socket.
Occasionally, when pipe
fi
tting dimensions are at
the tolerance extremes, it will be possible to fully
insert dry pipe to the bottom of the
fi
tting socket.
When this happens, a suf
fi
cient quantity of cement
must be applied to the joint to
fi
ll the gap between
the pipe and
fi
tting. The gap must be
fi
lled to obtain
a strong, leak-free joint.
36 www.americanwaterheater.com