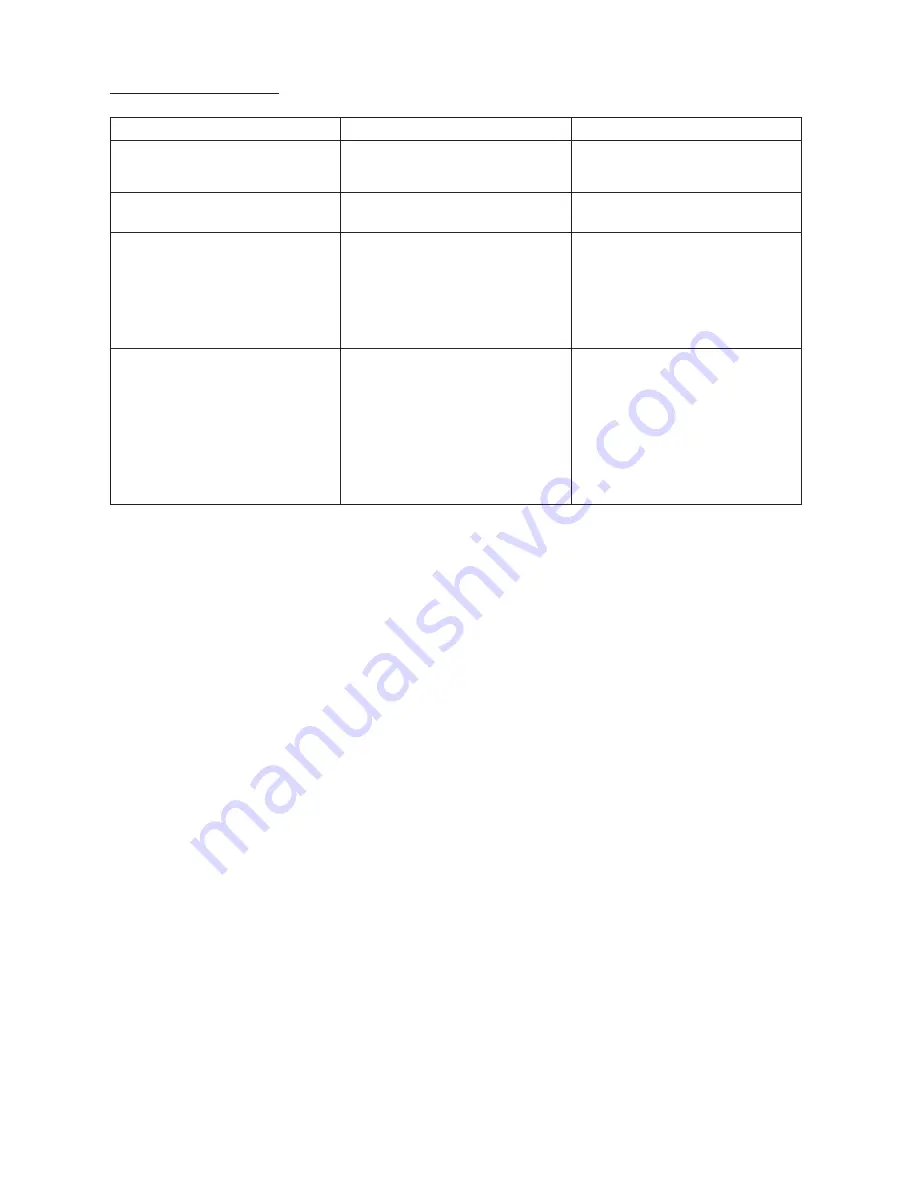
9 - ENG LISH
TROUBLE SOLVING
PROBLEMS
POSSIBLE CAUSES
SUGGESTED SOLUTIONS
Air leaking near the top of the tool or in
the trigger area.
1. Loose screws.
1. Tighten screws.
2. Worn or damaged O-rings or seals. 2. Install overhaul kit.
Air leaking near the bottom of the tool 1. Loose screws.
1. Tighten screws.
2. Worn or damaged O-rings or seals. 2. Install overhaul kit.
Tool dose nothing or operates sluggishly 1. Inadequate air supply.
1. Make sure the air compressor is set
between 70PSI and 115PSI.
2. Tool is too dry.
2. Add about 2-3 drops of lubrication
into the air connector.
3. Exhaust blocked.
3. Clean exhaust channel.
4. Worn or damaged O-rings or seals. 4. Install overhaul kit.
Fasteners are jammed in the tool
frequently.
1. Driver channel is worn.
1. Fix the drive channel.
2. Piston is broken or worn.
2. Replace the piston.
3. Bent fasteners.
3. Remove the bent fasteners, replace
with the right fasteners.
4. Dirty magazine.
4. Clean magazine.
5. Loose magazine.
5. Tighten screws.
6. Wrong fasteners
6. Verify that fasteners are the correct
size.