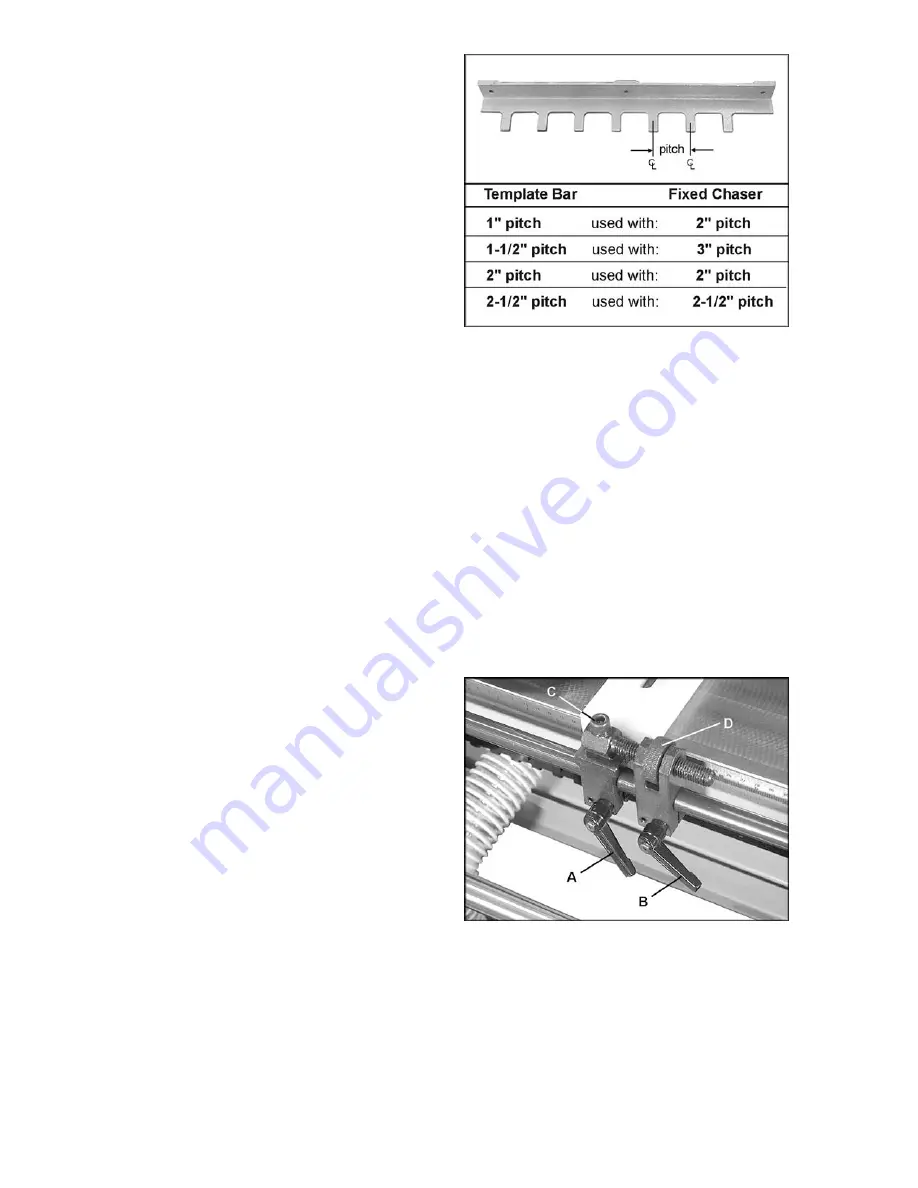
15
1. To replace the fixed chaser, remove the
three M6 socket head cap screws and flat
washers, using a 5mm hex wrench as
shown in Figure 17. Remove the fixed
chaser.
2. Install the new fixed chaser and make sure
it is level with the main table.
3. Re-insert and tighten the socket head cap
screws against the flat washers.
After mounting the fixed chaser, make sure it will
correspond to your chosen pitch on the template
bar. With the
machine power off
, slide the
headstock across the length of the fixed chaser,
allowing the cutter to move in and out of the
spaces. If there is any interference between the
cutter and one of the “fingers” on the fixed
chaser, then try a different fixed chaser, or
change the pitch of the template bar.
Horizontal and Vertical Fences
The workpieces will lie flush against the fences
during cutting to ensure squareness. Two buffer
pads made of polyethylene material are
mounted to the fences – these provide a
“chipbreaker” effect to prevent chip-out on the
left edges of the workpieces. They are designed
so the cutter can bite into them without any
damage to the cutter.
To adjust these fences, proceed as follows:
1. Place your FRONT/BACK workpiece on the
horizontal table and against the fence/buffer
pad. Move the headstock to the left edge of
the workpiece, then slide it to the right,
allowing the tracer pin to slide just a little
into the template recesses, while observing
through the dust hood window the progress
of the cutter. This will give you an idea
where the cuts will be made and how they
will be spaced across the width of the
workpiece.
2. For broad movement of the horizontal fence,
loosen both locking handles on the
horizontal fence (A and B, Figure 19) and
slide the horizontal fence into position.
Tighten both locking handles (A & B, Figure
19).
3. There is also a micro adjustment on the
horizontal fence; loosen locking handle (A,
Figure 19), but leave locking handle (B)
tight. Loosen the screw (C, Figure 19) with a
6mm hex wrench and rotate the knurled
knob (D, Figure 19) as needed for precise
positioning of the horizontal fence.
4. When finished, tighten screw (C, Figure 19)
and locking handle (A, Figure 19).
Figure 18
Figure 19
Summary of Contents for 1791305
Page 27: ...27 Base Assembly ...
Page 29: ...29 Hold Down Assembly ...
Page 32: ...32 Headstock Assembly ...
Page 34: ...34 Electrical Connections ...
Page 35: ...35 ...
Page 36: ...36 427 New Sanford Road LaVergne Tennessee 37086 Phone 800 274 6848 www powermatic com ...