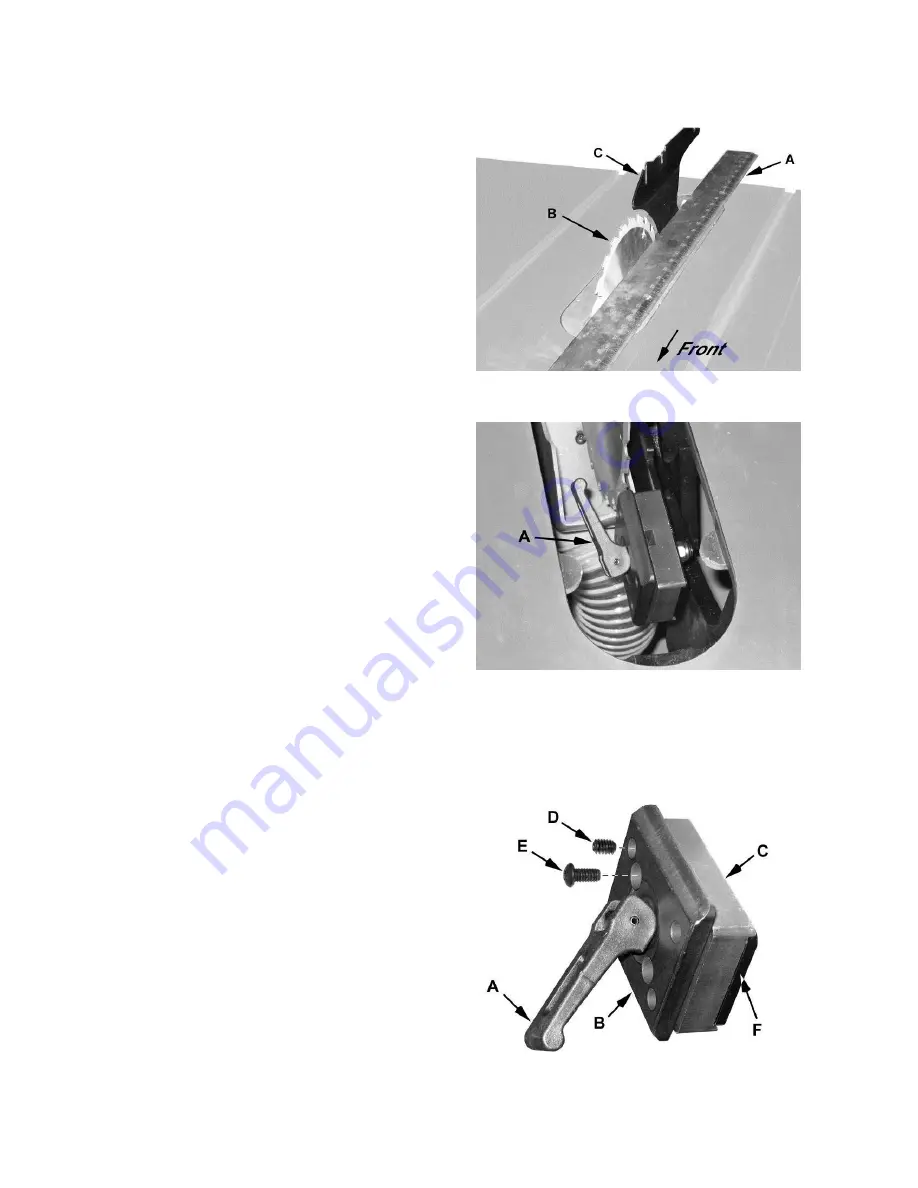
18
Riving Knife Adjustment
Lateral alignment
The saw blade and riving knife must be in line as
close as possible with each other (
lateral
alignment)
for the prevention of kickback. Upon
initial blade guard and riving knife installation no
further adjustment should be necessary. Alignment
should be checked and adjusted, if required, after
each blade change.
Check the alignment as follows:
1. Remove the
blade guard
and
pawl
(C, E,
Fig. 9).
2. Place
a
straightedge
(A, Fig. 17) on the table
so it rests against the
blade
(B, Fig 17) and
riving knife
(C, Fig. 17). Rotate the blade so the
top of the blade tooth touches the straightedge.
The saw blade and riving knife must be in line.
If adjustment is required:
3. Remove
the
blade guard
(C, Fig. 9) and
table
insert
.
4. Loosen the
lock handle
(A, Fig. 18) and
remove the riving knife, making a note as to
which direction the riving knife needs to be
moved to align it with the saw blade.
5. Using a 3mm hex wrench, make adjustments
to four
set screws
(D, Fig. 19) accessible
through openings located in the corners of the
floating clamp block
(B, Fig. 19).
Adjust any number of setscrews required to
bring the riving knife in alignment with the saw
blade. Then reinsert the riving knife, secure by
tightening the
lock handle
(A, Fig. 18) and
check the alignment per step 2.
Note:
Position the lock handle
towards
the saw
blade as shown in Figure 18. This will avoid the
table insert from being lifted when the blade is
raised with the handwheel.
6. Repeat steps 3–5 until the alignment is correct.
Blade proximity alignment
The gap between the saw blade and riving knife
must be between 3 and 8mm (Figure 20). If
adjustment is needed, note whether the blade to
knife gap needs to be increased or decreased.
Then adjust as follows:
1. Remove the blade guard, pawl, table insert and
riving knife.
Referring to Figure 19:
2. With a 5mm hex wrench, loosen two
socket
head button screws
(E).
Figure 17
Figure 18
Figure 19
Summary of Contents for 1792000K
Page 31: ...31 Table Cabinet Assembly ...
Page 35: ...35 Trunnion Motor Assembly ...
Page 37: ...37 Blade Guard Miter Gauge Assembly ...
Page 42: ...42 Notes ...
Page 43: ...43 ...