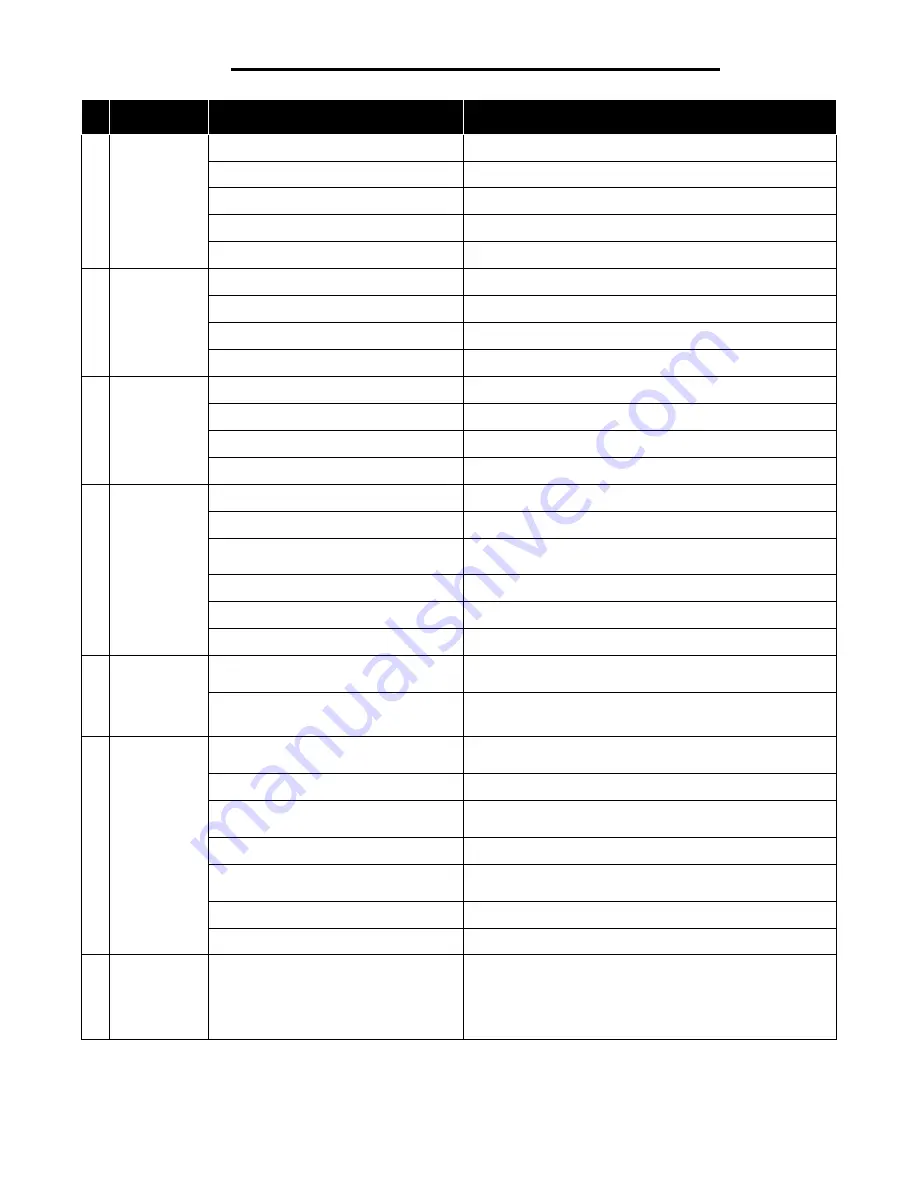
10
PROBLEM
POSSIBLE CAUSE
SOLUTION
1
Driving
blade does
not retract
1. Zero of Low air pressure
Check air supply for 80 psi minimum to 110 psi maximum
2. Lack of lubrication
Manually lubricate through male air inlet
fi
tting
3. Excessive dirt inside Stapler
Disassemble and clean
4. Bent or burred driving blade
Replace driving blade assembly (A-5)
5. Seals worn out
Replace driving blade assembly (A-5)
2
Driving
blade
retracts
slowly
1. Low air pressure
Turn up air pressure to 80-110 psi max
2. Lack of lubrication
Manually lubricate through male air inlet
fi
tting
3. Air supply restricted by small ori
fi
ce Use 1/4" minimum diameter air
fi
ttings
4. Excessive dirt inside nailer
Disassemble, clean and lubricate
3
Staple is not
countersunk
1. Low air pressure
Turn up air pressure to 80-110 psi max
2. Broken Driving Blade
Replace driving blade assembly (A-5)
3. Stapler hit hard surface
Move from obstruction
4. Worn out gate and/or gate plates
Replace gate (406-Gate, 402 and 403-Gate plates)
4
Stapler
leaks air
1. Air supply
fi
ttings loose
Tighten all air line
fi
tting connections
2. Dry wall dust in Stapler
Rebuild Stapler, Replace driving blade assembly (A-5)
3. Excess air pressure blew out seals Check air supply for 110 psi maximum—Replace driving
blade assembly (A-5)
4. Plunger screws loose
Tighten the 5 plunger screws (107)
5. Cracked or damaged body
Replace Stapler
6. Seals worn out
Replace driving blade assembly (A-5)
5
Bottom
of stapler
cracked off
1. Operated without rubber bumper
installed
Replace damaged parts
2. Excessive air pressure used
Replace damaged parts
6
Staples jam
in nailer
1. Not using Powerstapler™ Staples
Use Powerstapler™ Staples only (2”,1-3/4”,1-1/2”
Lengths)
2. Continued use after a short hit
Clear staple immediately after short hit
3. Staple pusher damaged or spring
broken
Replace staple pusher assembly (412 or 409)
4. Staple channel loose
Tighten staple channel retaining screws (411)
5. Bent staple stuck in gate or gate
plates
Remove gate plates B & A and clear out bent staple
(402, 403)
6. Hit another set staple or hard object Move from obstruction
7. Stapler gate worn out
Replace staple gate (402, 403)
7
Plunger
locked
up—won't
move or
fi
re
1. Lack of lubrication
Manually lubricate through male air inlet
fi
tting
PowerStapler 15FS Trouble Shooting Chart