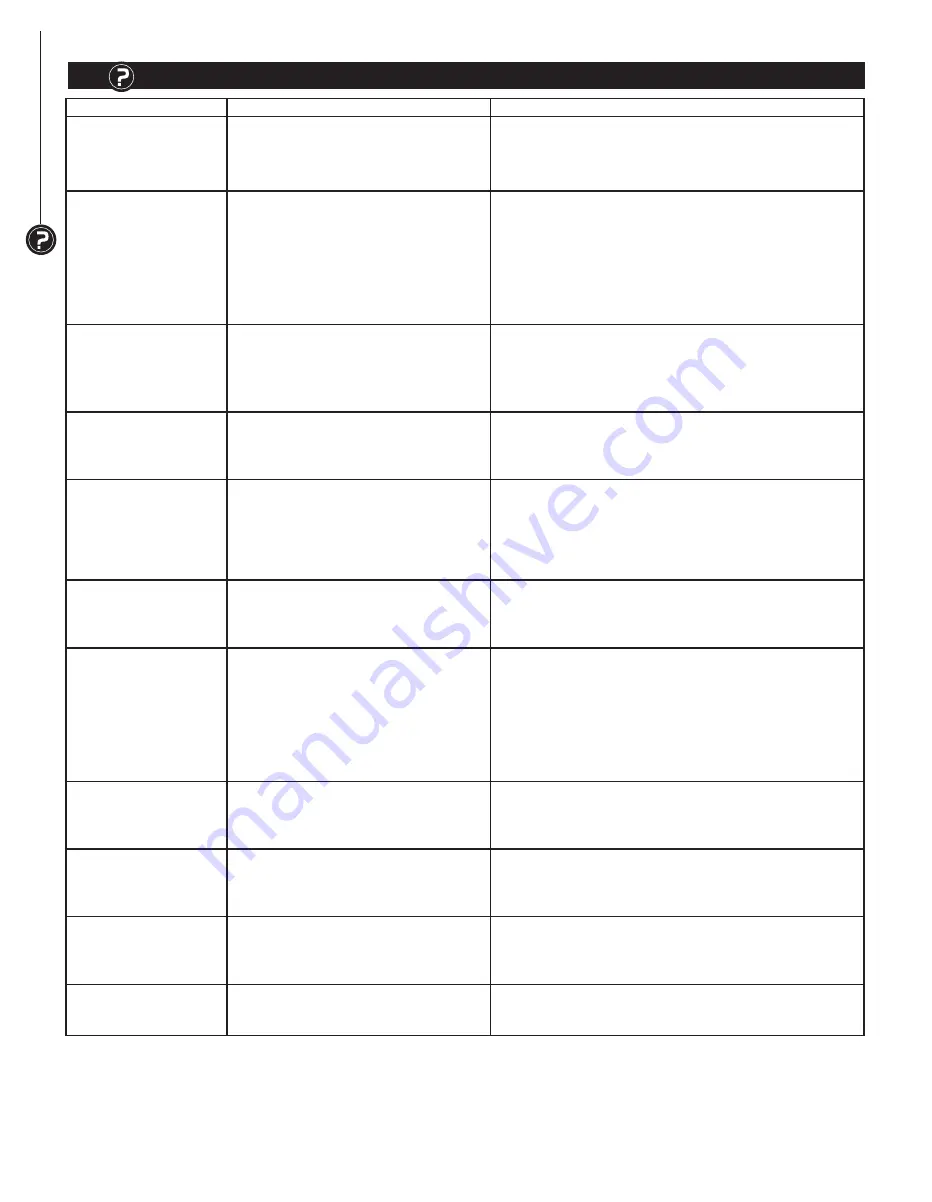
12
TROUBLESHOOTING
TROUBLESHOOTING
SYMPTOM
POSSIBLE CAUSE(S)
CORRECTIVE ACTION
Sanding Grains
easily rub off belt
or discs.
1. Sanding belt/disc has been stored
in an incorrect environment.
2. Sanding belt/disc has been
damaged or folded.
1. Ensure sanding accessories are stored away from
extremely hot or dry temperatures.
2. Store sanding accessories flat – not bent or
folded.
Deep sanding
grooves or scars
in workpiece.
1. Sanding belt/disc grit is too
coarse for the desired finish.
2. Workpiece sanded across
the grain.
3. Too much sanding force on the
workpiece.
4. Workpiece held still against the
belt/disc for too long.
1. Use a finer-grit sanding accessory.
2. Sand with the grain of the wood.
3. Reduce pressure on workpiece while sanding.
4. Keep workpiece moving while sanding on the
sanding accessory.
Sanding surface
clogs quickly.
1. Too much pressure against belt/
disc.
2. Sanding softwood.
1. Reduce pressure on workpiece while sanding.
2. Use different stock, different sanding accessories,
or accept that this will happen and plan on
cleaning or replacing discs/belts frequently.
Burns on workpiece.
1. Using a sanding grit that is
too fine.
2. Using too much pressure.
3. Work held still for too long.
1. Use a coarser-grit sanding accessory.
2. Reduce pressure on workpiece while sanding.
3. Do not keep workpiece in one place for too long.
Motor will not start –
fuses or circuit
breakers tripping
or blowing.
1. Short circuit in line, cord or plug.
2. Short circuit in motor or loose
connections.
3. Incorrect fuses or circuit breakers
in power line.
1. Inspect cord or plug for damaged insulation and
shorted wires.
2. Inspect all connections on motor for loose or
shorted terminals and/or worn insulation.
3. Install correct fuses or circuit breakers or switch
tool to an appropriately size circuit.
Motor overheats.
1. Motor overloaded.
2. Extension cord too long and of
insufficient gauge (weight).
1. Reduce load on motor (pressure on object being
sanded).
2. Utilize an extension cord of appropriate gauge and
length or plug tool directly into outlet.
Motor stalls
(resulting in blown
fuses or tripped
circuit).
1. Short circuit in motor or loose
connections.
2. Low voltage.
3. Incorrect fuses or circuit breakers
in power line.
4. Motor overload.
1. Inspect connections on motor for loose or shorted
terminals or worn insulations.
2. Correct low voltage conditions (for example:
improper extension cord length and/or gauge).
3. Install CORRECT fuses or circuit breakers or plug
tool into an appropriate circuit, matched to an
appropriate fuse or breaker.
4. Reduce the load on the motor.
Machine slows
when operating.
1. Feed rate too great.
2. Undersized circuit or use of
undersized extension cord.
1. Reduce the rate at which the workpiece is fed into
the working area of the tool.
2. Ensure circuit wires or extension cords are proper
gauge, or eliminate use of extension cords.
Machine
vibrates excessively.
1. Rubber feet worn, mounting
hardware loose
2. Workbench or table is not level
3. Worn bearings
1. Replace the rubber feet, tighten mounting
hardware
2. Shim or adjust as need
3. Have bearings replaced by service technician.
Workpiece frequently
gets pulled out of
operator’s hands.
1. Not supporting the workpiece
against the stop.
2. Attempting to sand (unaided) a
workpiece that is too small.
1. Use the platen (backstop) or miter gauge to
support the workpiece.
2. Use another hand tool or jig to grasp or hold
the workpiece.
Workpiece lifts up
from the sanding
disc/table.
Sanding on the “up” side wheel.
Sand on right side of sanding disc (as operator faces
the disc).
12