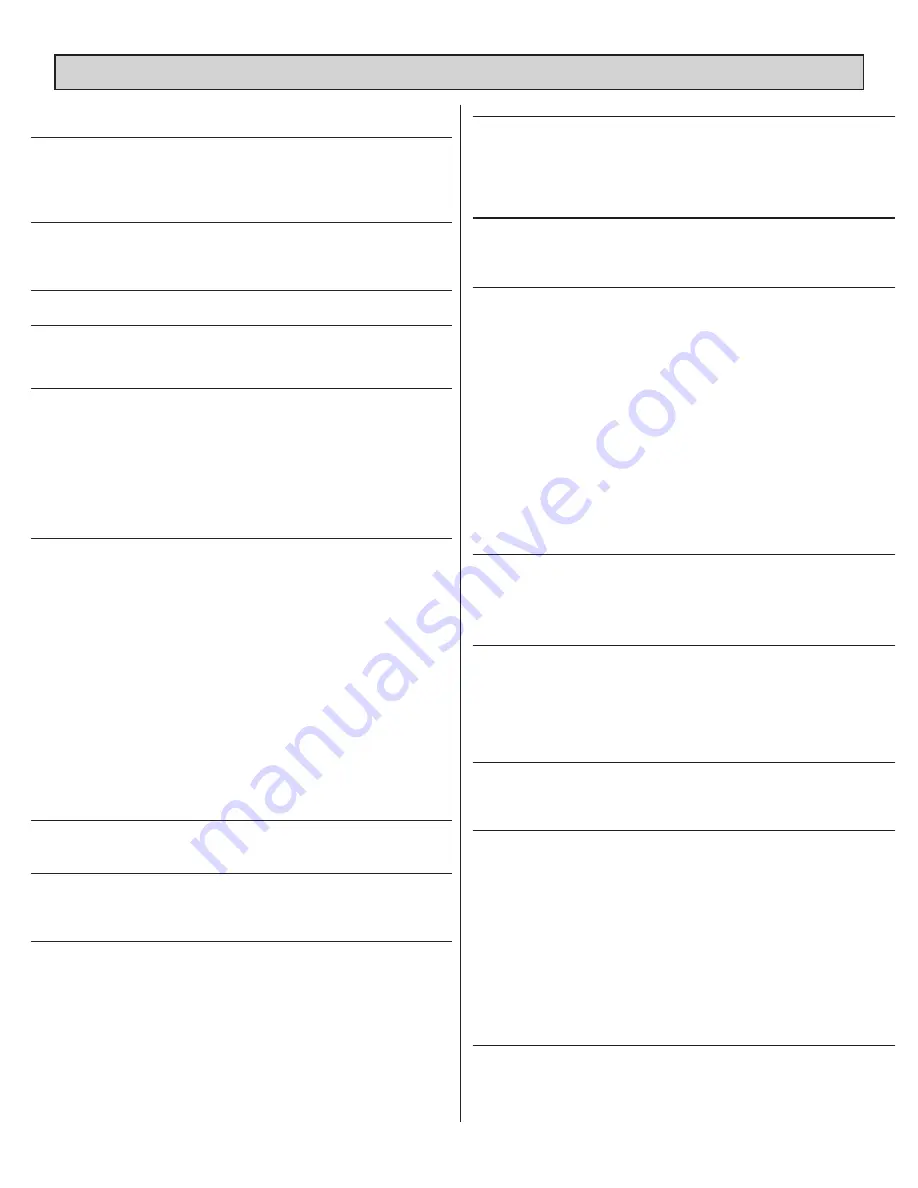
10
Troubleshooting Information
ELECTRICAL SYSTEM
PROBLEM
POSSIBLE CAUSE
SOLUTION
No electrical power.
1. Defective power cord.
1. Replace
2. Circuit breaker off or
2. Turn circuit breaker
fuse blown.
on or replace fuse.
Unplug any equipment
using the same circuit.
Switch is turned on.
1. Faulty electrical cable.
1. Repair or replace.
Intermittent power to
2. Defective switches.
2. Replace.
motor(s).
3. Loose terminal or dis-
3. Replace.
colored terminal connections.
Electrical Shock
1. Equipment not
1. Locate grounded
grounded.
outlet.
VACUUM SYSTEM
PROBLEM
POSSIBLE CAUSE
SOLUTION
Vacuum motor on
1. Drain hose open.
1. Close drain hose.
Little or no vacuum
Recovery tank lid must
on wand head.
be closed.
2. Defective vacuum hose
2. Repair or replace.
Kinks in vacuum hose.
3. Vacuum disconnected.
3. Open machine, connect
vacuum hose to
recovery tank.
Not enough vacuum
1. Damaged recovery
1. Replace
power at the machine. tank lid.
2. Lint clogging ball -
2. Remove screen.
type shutoff screen.
Clean out fibers and
accumulated dirt.
3. Vacuum hose connection
3. Check for leaks
between stand pipe and
around clamps and cuffs
vacuum motor.
(tighten). Replace damaged
hose(s).
4. Vacuum motor
4. Check air flow by
exhaust blocked.
removing hose from
machine and feel the
exhaust under the
machine. Remove
obstruction.
5. Cords not plugged into
5. Relocate one cord to a
seperate circuits
different room.
VACUUM SYSTEM
PROBLEM
POSSIBLE CAUSE
SOLUTION
Motor running and no 1. Faulty vacuum motor.
1. Replace.
vacuum at all.
No exhaust from the
2. Water shutoff closed.
2. Clean water shutoff
blowport.
screen.
Premature closing of 1. Dirty or clogged shut-
1. Remove and clean
ball type shutoff.
off filter screen.
screen.
Ball type shutoff
2. Ball coated with
2. Remove and rinse
failing to release after detergent or other
ball with clean water.
recovery tank is drained. foreign material.
3. Screen slightly out of
3. Bend screen by
round.
squeezing slightly by
hand until there is an
obvious space between
ball and inside of screen.
Foam/dirty solution
1. Foam from carpet by-
1. Use additional
coming out of vacuum passing water shutoff.
defoamer.
exhaust port.
2. Elbow in vacuum tank
2. The elbow should be
is not positioned
pointed directly at the
correctly.
side wall of the tank
away from the ball type
shutoff.
SOLUTION SYSTEM
PROBLEM
POSSIBLE CAUSE
SOLUTION
Pump motor on –
1. Clogged or faulty
1. Check intake on
no spray through jets. solution control valve.
valve and remove lint
or other foreign
material.
2. Clogged or faulty
2. Depress plunger on
quick disconnect on
solution hose against
housing.
inside wall of solution
tank. If solution is flow-
ing at this point, the
system is O.K. If no
solution flows, check the
quick disconnect for lint
and other foreign matter.
3. Punctured pump
3. Replace with
diaphragm.
diaphragm repair kit.
4. Clogged jets
4. clean jets on wand or tool.
Uneven spray from
1. Clogged strainer in
1. Unscrew strainer
jet. Spray weak or
solution tank.
and remove lint and
uneven.
any other foreign
material from screen.
2. Clogged jet.
2. Remove and clean.
Leaking or stuck
1. Foreign material in
1. Remove brass hex
solution valve.
valve.
plug, clean valve and
replace.
2. Loose brass hex nut.
2. Reseal hex and plug.
3. Valve worn or seals
3. Replace worn parts
worn.
with solution valve
repair kit.
Pump motor
1. Loose wiring
1. Tighten wiring
not working.
2. Defective pump
2. Replace with new
pressure switch
pressure switch assembly
3. Motor burnout
3. Replace pump motor
Pump pressure low
1. Clogged screens on
1. Unscrew strainer
strainer in solution tank
remove lint and any
other foreign material
from screen.
2. Punctured pump
2. Replace with
diaphragm.
diaphragm repair kit.
3. Defective rectifier or
3. Replace.
motor.
4. Pump not primed
4. Plug priming hose into
solution connection and place
end in solution tank. Run
pump for 4 minutes
Pump pressure varies. 1. Worn carbon brushes.
1. Replace brushes.
2. Defective pump
2. Replace.
pressure control switch.