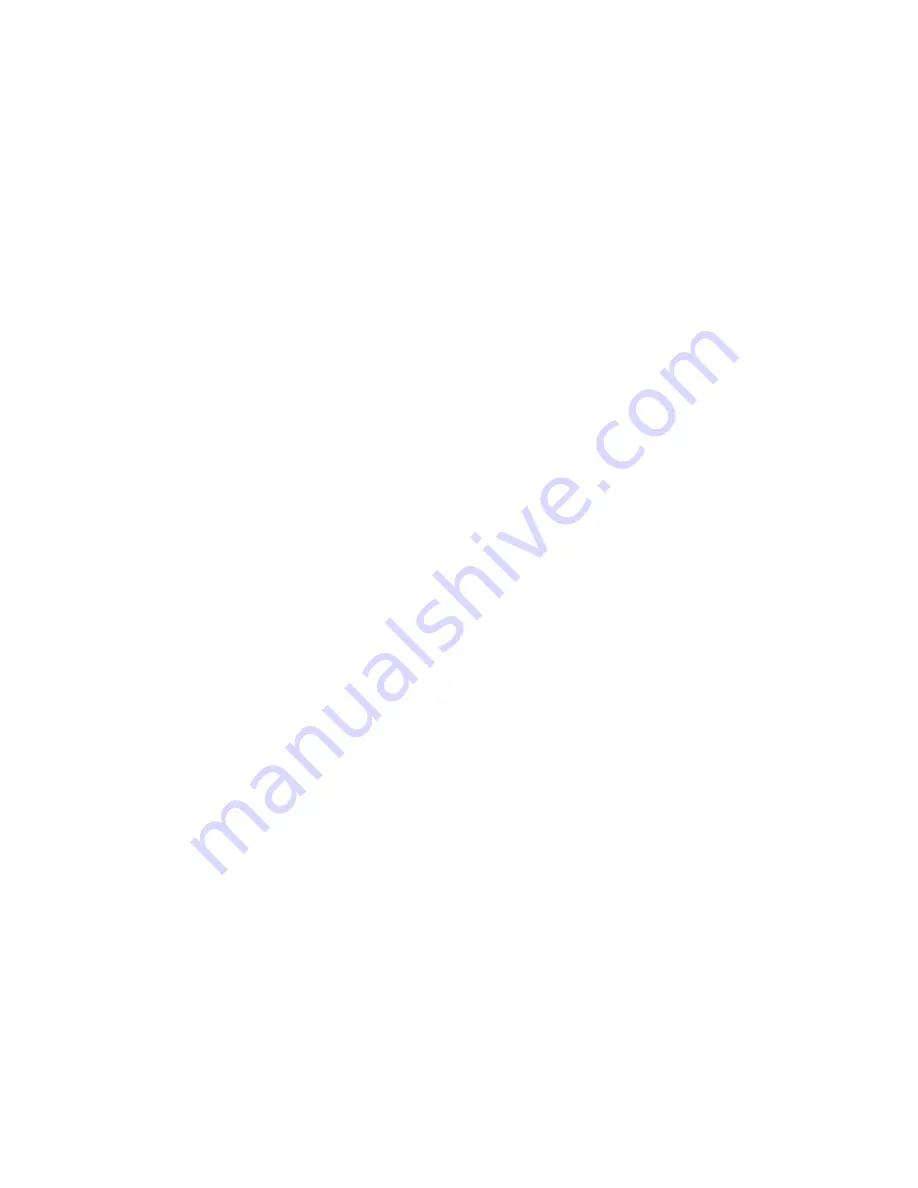
4. Installation of Air Heater(s)
4.1 General
Before installation, check that the local distribution
conditions, nature of gas and pressure (or oil type), and
adjustment of the appliance are compatible.
The air heater must be installed in accordance with the rules in
force and the relevant requirements of any fire regulations or
insurance company’s requirements appertaining to the area in
which the heater is located, particularly where special risks are
involved such as areas where petrol vehicles are housed, where
cellulose spraying is carried out, in wood working departments
etc.
The following minimum clearances for installation and servicing
must be observed.
To the front
1.0m
To the rear
The depth of the heater
To the side
1.0m
Above the heater
1.0m
Any combustible material adjacent to the air heater and the flue
system must be so placed or shielded as to ensure that its
temperature does not exceed 65 °C.
IMPORTANT:
1.No air heater shall be installed where there is a foreseeable
risk of flammable particles, gases vapours or corrosion inducing
gases or vapours being drawn into either the heated air stream
or the air for combustion. In such cases installation may only
proceed if the air to be heated and the air for combustion are
ducted to the heater from an uncontaminated source preferably
outside the building. In certain situations where only airborne
particles are present it may suffice to fit filters on the air inlet
ducts of the heater. Advice in these instances may be obtained
from Powrmatic Ltd.
4.2 Location
The location chosen for the air heater must permit:
- the provision of a satisfactory flue system and an adequate air
supply.
- adequate space for servicing and air circulation around the air
heater.
The heater(s) must not be installed in conditions for which it is
not specifically designed e.g. where the atmosphere is corrosive
or salty, and they are not suitable for outdoor use unless the /EA
style is specified. /EA heaters must be installed on a plinth such
that there is a minimum distance of 0.5m between ground level
and the lowest point of any air inlet grilles.
Where the location of the air heater is such that it might suffer
external mechanical damage e.g. from overhead cranes, fork
lift trucks, it must be suitably protected.
TE heaters are for normal operation within an ambient
temperature range of -10 to 25°C.
4.3 Installation
TE heater installation may only be completed by Powrmatic
Ltd or their appointed representatives.The heaters must be
installed on a level noncombustible floor capable of supporting
the weight of the heater.
4.4 Combustion & Ventilation Air Supply
There shall be provision for a supply of air for combustion.
1) Installation in the heated space
In buildings with a design air change rate of 0.5 /h or greater,
additional natural or mechanical ventilation is not necessary.
In buildings not having a design air change rate of 0.5 /h the
following apply.
Natural Ventilation
Grilles having a free area of at least 2cm² per kW of rated heat
input shall be provided at low level i.e. below the level of the
heater flue connection.
Mechanical Ventilation
Must ensure that the space air change rate is at least 0.5/h, must
be of the ‘input’ type and interlocked to ensure the heaters cannot
work if the input system is not working.
2) Installation in plant rooms or enclosures
This type of installation is not applicable to TE heaters.
4.5 Flue System
A single wall tee piece is supplied with each heater and must
be fitted to the flue outlet socket on the heater. A closed chimney
system that conforms to the requirements of EN1856-1 and has
a designation appropriate to the application must be connected
to the outlet of this tee. The cross sectional area of the chimney
serving the appliance must be not less than the area of the flue
outlet of the air heater. The chimney must have a minimum
height, from the heater to the flue terminal, of 2m. Horizontal
runs of flue must be minimised but where they are
unavoidable the ratio of vertical to horizontal flue should be
not less than 3:1.
If necessary a single offset using two 45° bends can be included
to avoid obstructions. The minimum equivalent resistance of
the flue system should not be less than 0.0mb, the maximum
not greater than 0.5mb. Details of how to calculate the resistance
of the flue to be installed are given in Appendix A.
In order to minimise condensation the use of twin wall chimney
is recommended. With high efficiency heaters some condensation
in the chimney, particularly at the terminal, is unavoidable and
in addition there can also be rain water ingress. Use of a chimney
system having joint seals will minimise any leakage from the
flue system. The heater tee is provided with a collection tray
and the outlet from this should be run to a drainage point e.g.
a gully. The condensation pipe from the collection tray to the
disposal point should be of non-corrodible material of not less
than 22mm (3/4") size.
Facilities should be made for disconnecting the chimney pipe(s)
from the air heater(s) for inspection and servicing purposes.
The chimney outlet must be fitted with a terminal and where
the heater chimney is less than 200mm (8") in diameter an
approved terminal must be used.
The chimney must be supported independently of the air heater.
The chimney must terminate in a freely exposed position and
must be situated so as to prevent the products of combustion
entering any opening in a building in such concentration as to
be prejudicial to health or a nuisance..
The chimney terminal must be installed not less than:
- 300mm below an opening e.g. window, air brick etc.
- 200mm below eaves or gutter.
- 300mm from an internal or external corner.
- 1200mm from a surface facing the terminal.
- 1500mm vertically from another terminal on the same wall.
- 300mm horizontally from another terminal on the same wall.
- 2000mm from ground level.
4.6 Fuel Connection
4.6.1 Gas Connection
(if applicable)
A servicing valve and downstream union must be fitted at the
inlet to the air heater gas controls assembly to facilitate servicing.
The gas supply to the air heater must be completed in solid
pipework and be adequately supported.
Warning
When completing the final gas connection to the heater do not
place undue strain on the gas pipework of the heater.
4.6.2 Oil Connection
(if applicable)
Refer to the supplied burner installation instructions for details
regarding oil supply options.
5.4 Lighting the Air Heater
5.4.1 Gas Controls Assembly - Soundness
Check
1. Ensure the gas service valve at the inlet to the gas controls
assembly is shut.
2. To prove soundness of the first main safety shut-off
valve and first start gas safety shut-off valve:-
a) Connect pressure gauge to the inlet pressure test point on
the main valve block or inlet pipework.
b) Open gas service valve and allow pressure to
stabilise before shutting it again. The valves are sound if
no pressure drop is observerved. If a pressure drop is
observed do not proceed until the fault has been rectified.
Remove pressure gauge and refit sealing screw in pressure
test point.
5.4.2 Sequence Check
1. Refer to the burner instructions supplied with the heater.
5.4.3 Final Adjustment
1. Remove the sealing screw from the pressure test point located
on the side of the gas inlet to the burner head and attach a
pressure gauge. Remove the sample point cover plug from the
outlet flue length and insert a CO
2
measuring instrument.
2. Remove the link in the main electrical control panel to isolate
the main gas valves.
3. Turn "ON" the main electricity supply and check that the
following sequence of events occur.
i) Burner fan runs.
ii) Ignition spark is heard.
iii) Start gas valves open.
iv) Start gas flame is established.
4. Check that the start gas pressure agrees with that in Tables
3.1 or 3.2. If necessary adjust the start gas pressure (See Data
Sheet).
4. Turn "OFF" the main electricity supply.
5. Reconnect the main gas valves electrical link.
6. Turn "ON" the main electrical supply and the burner will run
through its sequence untill main flame is established. Check
that the main burner gas pressure agrees with that on the
specification sheet. If necessary adjust the main burner gas
pressure (See Data Sheet and also Burner Manual for method).
7. Measure the CO
2
content of the flue gases. If it is necessary
to adjust the combustion air ratio controls, to obtain a reading
of 9.0 - 9.5%, refer to the Burner Manual.
8. Remove pressure gauge, refit sealing screw in pressure test
point and flue sample point cover plug.
5.4.4 Final Soundness Test
1. After making final gas rate checks all joints on the gas controls
assembly must be tested for soundness using leak detection
fluid.
5.5 Controls
The general layout of the control panel is as shown opposite.
The MC200 controller is mounted in the access door of the
electrical panel.
5.5.1 Inverter Drives
This will have been set prior to the heater being despatched. A
data sheet of the settings used is included for future reference.
5.5.3 MC200
See the MC200 instructions seperately supplied.
5.6 Hand Over
Hand the Users Instructions to the user or purchaser for retention
and instruct in the efficient and safe operation of the air heater
and associated controls.
Adjust the automatic controls to those values required by the
User.
Finally, advise the user or purchaser that, for continued efficient
and safe operation of the air heater, it is important that servicing
is carried out annually.
In the event that the premises are not yet occupied turn off the
gas and electricity supplies and leave instructional literature
adjacent to gas meter.
10
6. Servicing
WARNING: Always switch off and disconnect electricity supply
and close the gas service valve before carrying out any servicing
work or replacement of failed components. Access doors on TE
units are fitted with electrical interlocks however these alone
must not be relied upon to prevent equipment operation during
maintenace or servicing work.
6.1 General
Full maintenance should be undertaken not less than once per
year. After any servicing work has been completed or any
component replaced the air heater(s) must be fully commissioned
and tested for soundness as described in Section 6.
6.2 Burner Maintenance
1. Refer to the Burner Instructions supplied with the heater.
6.3 Heat Exchanger Cleaning
1. Disconnect the gas supply at the inlet to the gas controls
assembly.
2. Unplug the electrical connections from the heater electrical
panel to the buner.
3. Remove the nuts securing the burner to the heat exchanger
and remove the burner.
4. (TE 41 & 61 only) Remove the fixings of the second section
(from the floor) rear panel and hinge panel down to expose the
heat exchanger clean out access plate.
(TE21 only) Remove heater rear panel.
5. Remove the nuts securing the cleanout plate and remove.
6. Withdraw the heat exchanger baffles, if fitted.
7. Brush through heat exchanger tubes and remove loose material
using a vacuum cleaner.
8. Reassemble all components in reverse order. Inspect all gaskets
and replace if necessary.
6.4 Fan Assembly
WARNING
Electrical supplies to the heater must be isolated
and
locked OFF before proceeding.
1. Gain access to the fan section by removing the lower panels.
2. Inspect the fan blades to see that they are not damaged and
that there is no excessive build up of deposits that could give
rise to an imbalance. If necessary clean the fan blades using a
stiff brush and vacuum cleaner.
6.5 Replacement of Faulty Components
6.5.1. Burner Components
1. Refer to the burner supplement supplied with the heater.
6.5.2 Gas Controls Assembly
1. Refer to the burner supplement supplied with the heater.
6.5.3 Main Fan Motors
DANGER
Electrical supplies to the heater must be isolated
and
locked OFF before proceeding.
1. Remove fan assmbly from motor shaft. Note: On TE41 and
TE61 units the fans are fitted to the motor shafts by taper lock
bushes.
To remove a bush slacken all screws in it and remove (one or
two screws depending on the size of the bush). After oiling point
and thread of grub screws (bush size 1008 to 3030) or under
the head and thread of cap screws (bush size 3535 to 5050)
insert them into the jacking off hole(s) in the bush.
Tighten the screw(s) uniformly and alternatively until the bush
is loose in the hub and fan is free on the motor shaft. Remove
fan and bush.
4.6 Electrical Connections
Wiring external to the air heater must be installed in accordance
with the I.E.E. Regulations for Electrical Installations and any
local regulations which apply. Wiring should be completed in
flexible conduit.
Heaters are for use with 230V, 1N, 50Hz or 400V, 3N, 50Hz
supplies
(see heater data plate)
.
The method of connection to the main electricity supply must:-
- facilitate the complete electrical isolation of the heater(s) that
will prevent remote activation of the heater during servicing.
- be in a readily accessible position adjacent to the heater(s).
- serve only the heater(s).
- have a contact separation of at least 3mm in all poles. See the
wiring diagram for the heater electrical connections. All units
are fully pre-wired and only require final connections for the
incoming mains supply. The electrical supply must be run to a
point adjacent to the heater and be suitably terminated to provide
an isolation point that will prevent remote activation of the unit
during servicing. The heater electrical panel is located at the
front of the heater and cable entry points are provided in the
adjacent heater framework. Reference must be made to the
enclosed data sheet to ascertain the electrical loading of the air
heater(s) being installed so that cables of adequate cross-sectional
area to safely carry that load are used for the electrical
installation. The length of the conductors between the cord
anchorage and the terminals must be such that the current
carrying conductors become taut before the earth conductor if
the cable or cord slips out of the cord anchorage. All external
controls must be of an approved type.
See the wiring diagram accompanying these instructions.
5. Commissioning & Testing
Note: TE41 & TE61 - Turn key for electical panel access door
locks may be used to operate door elctrical interlock for
commissioning purposes .
5.1 Electrical Installation
Checks to ensure electrical safety must be carried out by a
qualified person.
5.2 Gas Installation
The whole of the gas installation, including the meter, should
be inspected and tested for soundness and purged in accordance
with the recommendations of the applicable IGE documents.
5.3 Fan Rotation
1. Whilst the main electrical supply is isolated and
locked off
inspect the fan blades and ascertain the required direction of
rotation. See below.
1. Reinstate the electrical supply Turn the AUTO-OFF-MAN
switch to 'MAN'. Depending on the current state and setting of
the MC200 the mains fans may start immediately. If they do
not switch MC200 control (see MC200 manual supplied) to
‘Summer’ mode and then press the fan button on the front cover.
2. Ensure that the fan direction of rotation corresponds with the
direction of rotation arrow on the fan blades. If necessary turn
the AUTO-OFF-MAN switch to 'OFF', turn OFF the main
isolator and reverse the direction of rotation by interchanging
any two of the 3ph main supply leads at the terminal strip in the
electrical panel.
2. If appropriate reset the MC200 to Winter mode.
Fault
Main burner will not light
Main burner lights, but
goes out before main fan
comes on.
Main fan fails to run
Cause
Electrical
Electrical
Electrical
Action
1. Check electrical and fuel supplies are ON.
2. Check controls are ON or calling for heat.
1. Unit goes out on high limit -
a. Check limit thermostat setting - See Section 7.5.5.
b. Faulty limit thermostat - change.
3. Inverter code 0C6, motor overloaded. - Check running amps. See
specification sheet.
1. Fan motor (or capacitor - 1ph only) failed - replace.
2. Fan thermostat faulty - replace.
3. Inverter failed - replace
8. Short List of Parts
Refer to the burner supplement supplied with the heater.
Refer to Powrmatic Ltd for the details of other parts quoting the serial number of the heater.
7.
Fault Finding
Refer also to the burner supplement supplied with the heater
3. Fit new motor and reassemble in reverse order.
Refit the taper lock bush into the fan and line up the holes (half
threaded holes must line up with half straight holes). Lightly
oil the grub screw or cap screws and srew in but do not tighten.
Fit fan to shaft. Gradually tighten the grub/cap screws in
accordance with the torque schedule. Fill all holes with grease
to prevent dirt ingress. Recheck torque settings after half an
hours running.
6.5.4 Main Air Fan(s)
DANGER
Electrical supplies to the heater must be isolated
and
locked OFF before proceeding.
Should it be necessary to replace one or both of the fans
proceed as follows.
(TE41 & 61)
1. Remove fans as detailed in 6.5.3 above. On units with fans
having a high number of blades it may also be necessary to
remove one or two heat exchanger module side panels.
(TE21 & 31)
1. Remove one or two side panels to gain access to the top of
the fan shaft. Remove set screw securing fan assembly to the
motor shaft and remove fan.
2. Fit new fan(s) and reassemble in reverse order. Ensure the
loose key that prevents the fan assembly rotating on the fan
shaft is refitted.
6.5.5 Fan and Limit Thermostats
6.5.5.1 Honeywell L4064B
1. Release the single screw securing the fan and limit thermostat
cover and remove cover by pulling forward.
2. Release wiring from screw terminals.
3. Remove the 2 screws securing the thermostat to the heater
panel and withdraw thermostat and sensor.
4. Reassemble new unit in reverse order refering to the heater
wiring diagram to ensure correct wiring location.
Important:
A replacement fan/limit thermostat will have a brass
link between the bottom fan terminal and the bottom limit
terminal (situated in the slot between the two terminals). This
MUST
be removed, by breaking the link off using a pair of thin
nose pliers, before the replacement thermostat is installed.
5. Ensure that the fan and limit settings are as follows:-
Fan ON - 40°C, Fan OFF - 20°C
Limit 60°C
Note:
The new L4064B may be supplied with the limit
temperature mechanically limited to less than the setting required.
To release the mechanical limit push a pointed object into the
small hole at the top of the dial. At the same time prevent the
dial from rotating and push the limit temperature adjuster around
to the required setting.
6.5.5.2 High Limit Thermostat
TE41 & 61
1. Release the two screws securing the limit thermostat housing
cover and remove cover by pulling forward.
2. Release the thermostat from the front cover, two screws
3. Pull off wiring connectors from under the thermostat.
4.Remove a central side panel from the heater exchanger section
to gain access to the heat exchanger and release the thermostat
sensing phial from its holder on top of the heat exchanger and
withdraw thermostat and phial.
5. Reassemble new unit in reverse order refering to the heater
wiring diagram to ensure correct wiring location.
6. Ensure that the setting is as follows:-
Limit 100°C
TE21 & 31
1. Release the two screws securing the limit thermostat housing
cover and remove cover by pulling forward.
2. Release the thermostat from the front cover, two screws
3. Pull off wiring connectors from under the thermostat.
4.Remove heater side panels and release the thermostat sensing
phial from its holder on the fan shroud and withdraw thermostat
and phial.
5. Reassemble new unit in reverse order refering to the heater
wiring diagram to ensure correct wiring location.
6. Ensure that the setting is as follows:-
Limit 50°C
6.5.5.3 Fan Protection Thermostat
TE 21 & TE31
1. To replace the thermocouple remove the side panels on
on side of the heater. Release the tip of the thermocouple
from its holder and disconecct the other end from the relay
base. Renew using a Type K thermocouple only.
2. Disconnect the electrical connections from the motor and
remove the motor. Note: Providing the replacement motor is
identical it is recommended that bolts are fitted in the motor
mounting plate directly under the existing motor so that mounting
position is marked. The bolts will also support the weight of the
new motor whilst it is fitted.