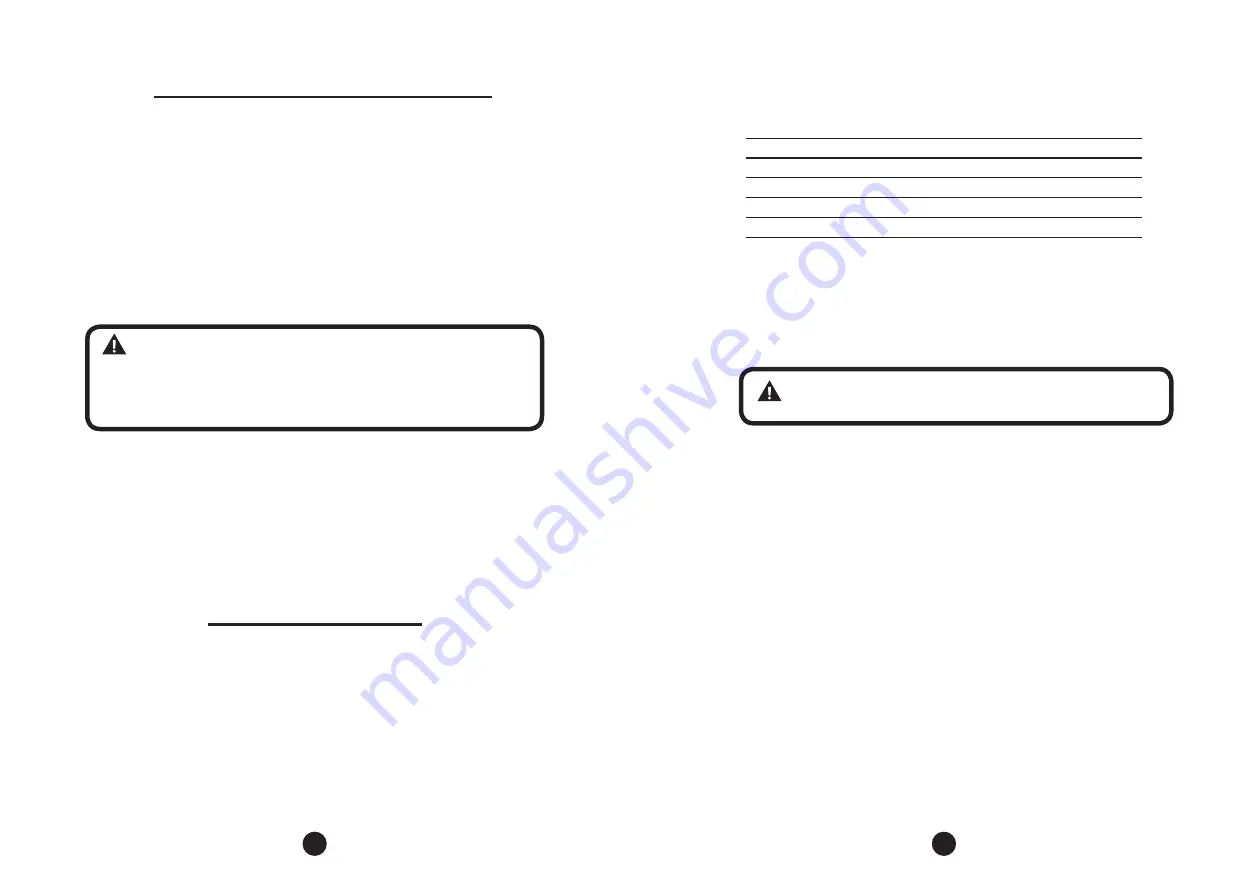
22
23
LOGICAL FUNCTION OF THE SYSTEM FOR GATES
First operation after installation (gate travel recognition)
When the control board is powered up for the first time, after the operator being
properly installed, the gate should start an opening movement after an external
command or if the ‘+’ button is pressed.
If instead the gate starts a closing movement, remove the ‘F/R’ jumper to change
the direction of the motor. After removing the jumper the gate will stop. Press
the ‘+’ button again or proceed with an external command. The gate should start
opening. Let the gate reach the opening physical stop or the REED A (magnet limit
switch) is activated. Then, it will automatically reverse the movement direction to
close; let it reach the closing physical stop or activate the closed REED F.
NOTE
: The operator can work with encoder (digital) or either encoder
+ reed (hybrid), but cannot work only with a reed.
During the travel recognition only the obstruction of the external
entrapment protection device can reverse the gate movement
direction.
Gate Operation after a power cycle (travel recognized)
After the previous operation, the gate does not need to recognize the travel
again. When the inverter is powered up, the gate simply closes slowly after a
command (‘+’ button or external one), until it reaches the closing physical stop. The
motor will turn off and the operator is ready to use again.
If the photocell is obstructed or the board receives a command during this first
closing, the gate movement direction will be reversed and, in this case, when the
gate is fully opened the operator is ready to use.
PARAMETERS PROGRAMMING
Operator Model Selection
The board can operate, with the same firmware, on gates and barriers.
To select the desired model, simply remove the TST jumper and close the B/G
(Barrier / Gate) pins. When the function is selected, the “OSC” LED flashes rapidly for
short time interval and then indicates the parameter value.
The following table shows the number of blinks for each function:
NUMBER OF FLASHES
REFERENCE MODEL
1
LIGHTWEIGHT GATE (RESIDENCIAL)
2
HEAVY GATE (INDUSTRIAL)
3
BARRIER 3M (BARRIER UP TO 3M IN LENGTH)
4
BARRIER 6M (BARRIER ABOVE 3M TO 6M IN LENGTH)
5
NON STOP BARRIER (SPECIFIC PPA BARRIER MODEL)
The pause before repeating the parameter value is three seconds and the flashes
indicating the parameter value occur every half second, so they are very different.
To increase the values, simply press the plus (+) button and to decrease, simply
press the minus (-) button.
When you reach the desired model, return the B/G jumper to the TST position.
Once this is done, the board is ready to operate on the chosen operator model.
NOTE:
For the DZ Concominium operator or higher model, use the
“Heavy Gate” parameter in this function.
TST jumper Function
When the TST jumper is removed, the control board enters a mode of operation that
allows to position the operator at any point of its travel path to adjust the limit switches
or to check the mechanical part.
In this operating mode, when the (-) button is pressed, the motor is activated in a
clockwise direction while the button is pressed, when the motor is released, the motor
shuts off, and when the (+) button is pressed, it is activated counterclockwise.
Adjustment of other parameters
The control board also has other functions controlled by the DS1 dip switch.
When a function is selected, the ‘OSC’ LED flashes rapidly for a specific period of time
and then indicates the parameter value. When the ‘OSC’ LED flashes each half second
(0.5s), the minimum value is selected; when it is off, an intermediate value is selected
and when it keeps lit, the maximum value is selected.
In order to increase the values, just press the ‘+’ button; to decrease the values, just
press the ‘-’ button when the desired function is selected.
When leaving the function, the ‘OSC’ LED rapidly blinks again for a specific period
of time, and when all DIPs are off it blinks in a one-second interval again.