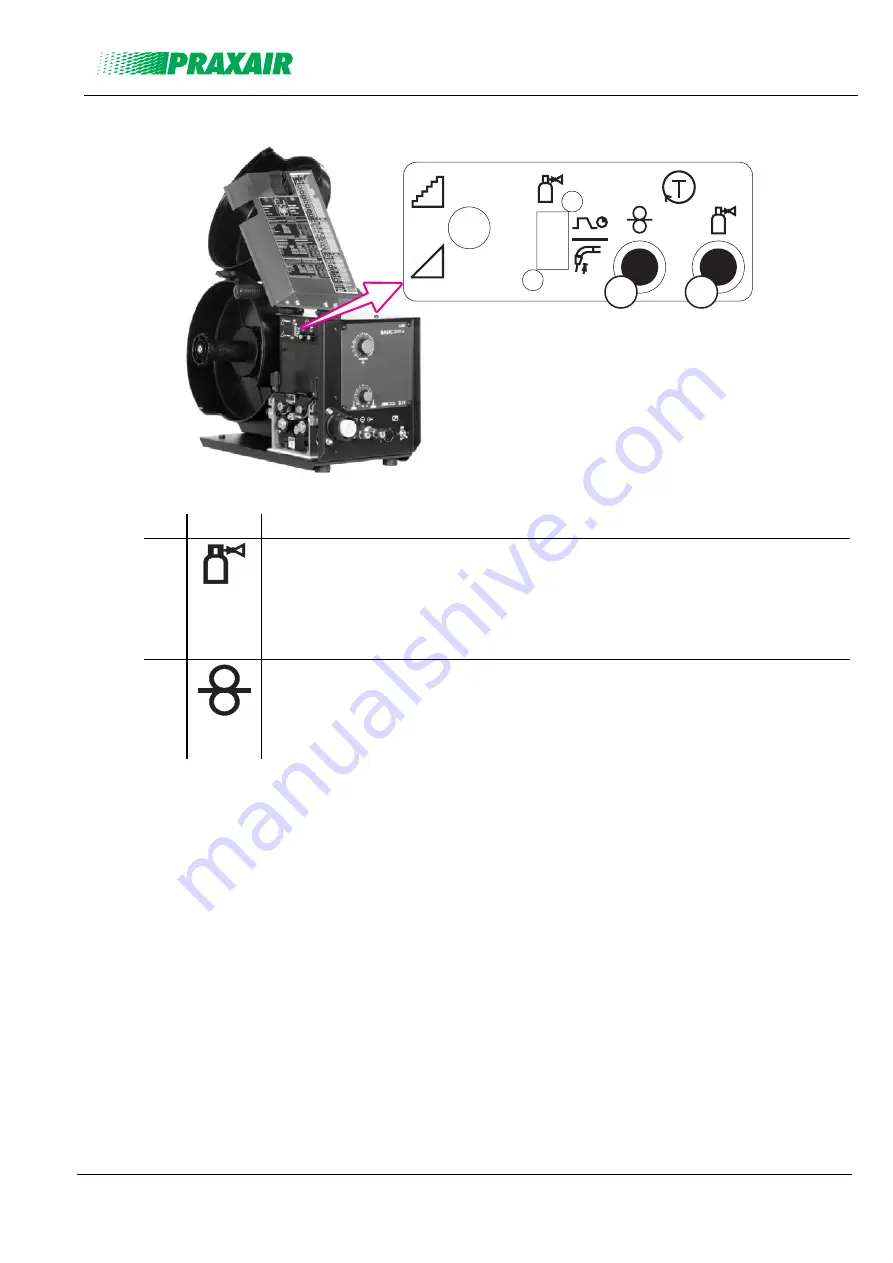
Functional characteristics
Machine control – Operating elements
Item No.: 099-004838-PRA01
25
5.1.2
Operating elements in the machine
Figure 5-4
Item Symbol Description
0
1
“Gas test” button
The welding voltage and wire feed remain off when testing and setting the gas flow.
Pressing the key button once causes shielding gas to flow for approx. 25 seconds. The
button can be pressed again at any time to cancel the process.
This ensures a high standard of safety for the welder by preventing accidental ignition
of the arc.
2
"Wire inching" button
For inching the wire electrode when changing the wire spool
(speed = 50% of set wire speed)
The welding wire is inched into the tube package with the current off and without the
gas being expelled.