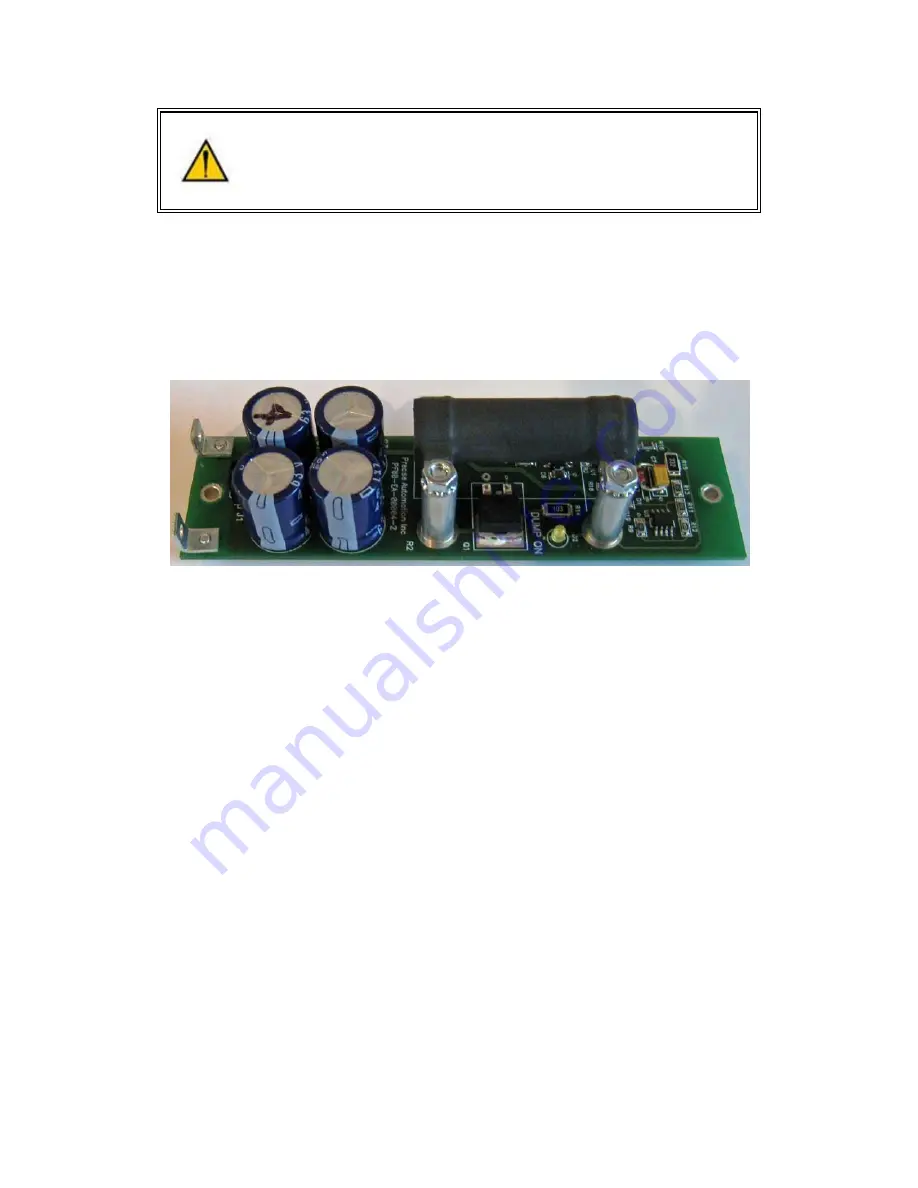
Introduction to the Hardware
7
DANGER:
In addition to exposed high voltage pins and components,
the
heat sinks on the Power Supplies are not grounded and expose high
voltage levels.
AC power to the robot must be disconnected prior to
accessing these units.
Energy Dump Circuit
The 48 VDC supply has a regulated output and an overvoltage protection circuit that is triggered if the
voltage reaches 60 volts. Rapid deceleration of the robot motors can generate a Back EMF voltage that
can pump up the motor voltage bus. In order to avoid bus pump up, an Energy Dump Circuit is
connected to the 48 VDC bus.
Remote Front Panel, E-Stop Box and Manual Control Pendant
For users that wish to have a hardware E-Stop button, Precise offers an E-Stop Box or a portable
Hardware Manual Control Pendant that includes an E-Stop button. The E-Stop box can be plugged into
the green Phoenix connector in the connector panel in the base of the robot. The E-Stop box completes
a circuit from the top pin, Pin 1 (24VDC) to Pin 2 (E-Stop) in this connector. If this circuit is not completed
it is not possible to enable motor power to the robot. If no E-Stop box or Manual Control Pendant is
connected, a jumper must be connected between these two pins to enable robot motor power. For those
applications where an operator must be inside the working volume of the robot while teaching, a second
teach pendant with a 3-position run hold switch is available. The Manual Control Pendants can be
plugged directly into the 9 pin Dsub connector mounted on the robot's Facilities Panel in the base of the
robot. The E-Stop connections are also present on the 9 pin Dsub connector and each of these units
provides the hardware signals to permit power to be enabled and disabled.
Summary of Contents for PF3400
Page 8: ......
Page 32: ...PreciseFlex_Robot 24 Appendix B TUV Verification of PF400 Collision Forces...
Page 33: ...Introduction to the Hardware 25...
Page 34: ...PreciseFlex_Robot 26...
Page 35: ...Introduction to the Hardware 27...
Page 37: ...Introduction to the Hardware 29 Appendix C Table A2 from ISO TS 15066 2016...
Page 38: ...PreciseFlex_Robot 30 Table A2 Continued...
Page 41: ...Introduction to the Hardware 33 PF400 500gm Safety Circuits PF3400 3kg Safety Circuits...
Page 45: ...Installation Information 37...
Page 46: ...PreciseFlex_Robot 38...
Page 47: ...Installation Information 39...
Page 48: ...PreciseFlex_Robot 40...
Page 54: ...PreciseFlex_Robot 46 Schematic System Overview...
Page 55: ...Hardware Reference 47 Schematic FFC Boards Revision B PF400...
Page 56: ...PreciseFlex_Robot 48...
Page 57: ...Hardware Reference 49 Schematic FFC Boards Revision C PF400...
Page 58: ...PreciseFlex_Robot 50 Schematic FFC Boards 3kg PF400...
Page 59: ...Hardware Reference 51...
Page 60: ...PreciseFlex_Robot 52 Schematic Safety System Overview PF400 CAT3...
Page 61: ...Hardware Reference 53...
Page 62: ...PreciseFlex_Robot 54 Controller Power Amplifier Connectors Control Board Connectors...
Page 63: ...Hardware Reference 55 Gripper and Linear Axis Controller Connectors...
Page 64: ...PreciseFlex_Robot 56...
Page 65: ...Hardware Reference 57...
Page 66: ...PreciseFlex_Robot 58 Schematic Slip Ring for 60N Gripper...
Page 67: ...Hardware Reference 59...
Page 68: ...PreciseFlex_Robot 60...
Page 69: ...Hardware Reference 61...
Page 70: ...PreciseFlex_Robot 62...
Page 71: ...Hardware Reference 63...
Page 72: ...PreciseFlex_Robot 64...
Page 73: ...Hardware Reference 65 Motor 60N Gripper...
Page 74: ...PreciseFlex_Robot 66...
Page 106: ...PreciseFlex_Robot 98 b The CALPP application takes about 1 minute to run...
Page 124: ...PreciseFlex_Robot 116 Wiring for 60N Gripper with Battery Pigtail Wiring for Pneumatic Gripper...
Page 125: ...117 Wiring for Vacuum Gripper Wiring for Vacuum Pallet Gripper...