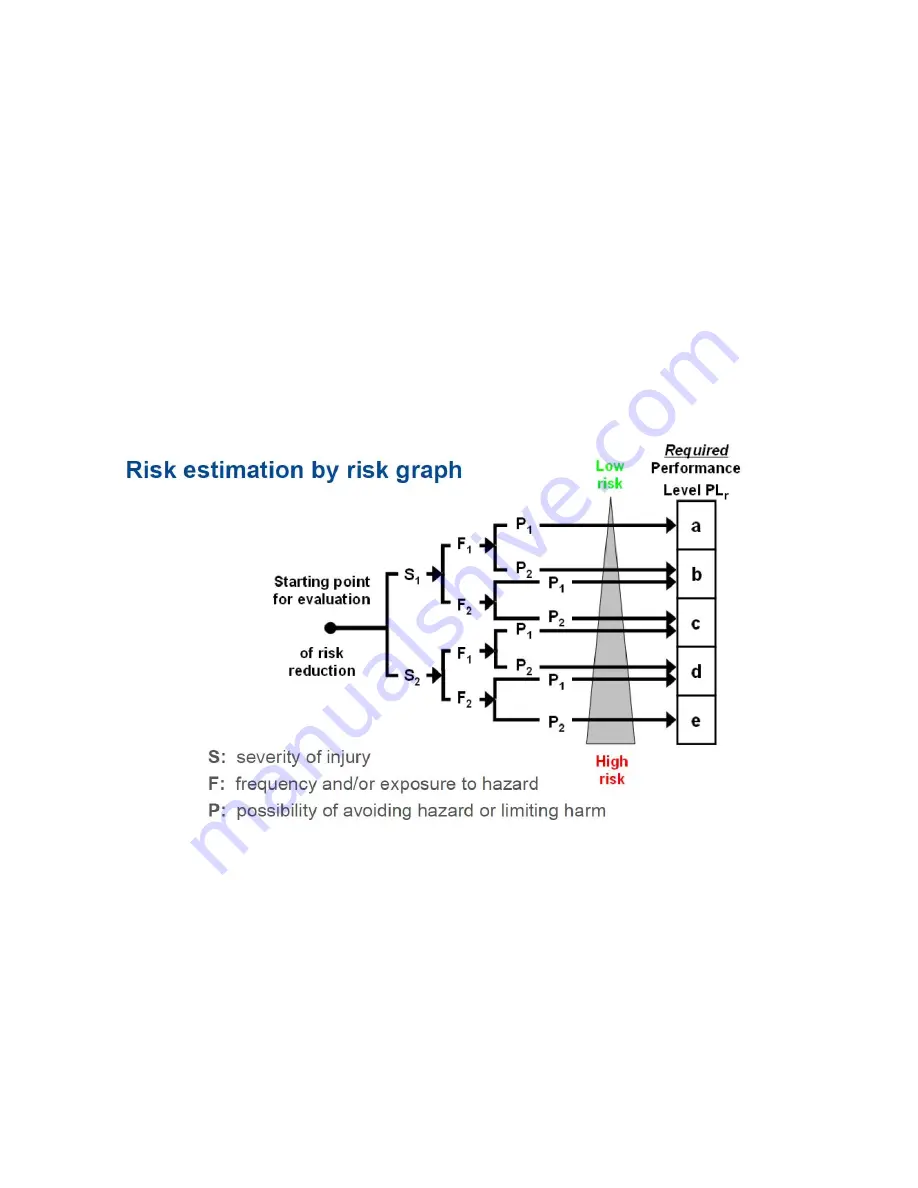
PreciseFlex_Robot
14
5.10.5 Power and force limiting by inherent design or control
“The power or force limiting function of the robot shall be in compliance with 5.4. If any parameter limit is
exceeded, a protective stop shall be issued.”
Section 5.4 requires the system designer to perform a Performance Level (PL) or Safety Integrity Level
requirement
(SIL) check based on the robot AND the application tooling and workcell. For example, a
safe robot may still need safety interlock screening if it is moving a dangerous tool. This requires the
application designer to review the requirements of 10218-2:2011 which addresses robots in workcells.
Determining a Machine’s Required Performance Level (PLr). ISO 13849-1:2006 Annex A
provides
tables and a worksheet to identify a machine’s Required Performance Level
requirements. Figure 1 below
shows a flow chart for determining Performance Levels. Briefly these are: Select S1 for slight injuries
(normally reversible) and S2 for serious injuries or death. Select F1 for infrequent exposure to a hazard
(for example only from time to time) and F2 for frequent exposure (for example continuously entering
workcell). Select P1 for easily recognizing and avoiding a hazard (for example a repetitive motion) and
P2 for a hazard that may be difficult to avoid (for example a sudden, non-repetitive motion that may trap
an operator). An example of determining PL for a PF400 workcell is given in Appendix A of this section,
where it is shown that a PL of “a” is sufficient for the workcell.
Figure 1
In determining whether operators should be prevented from entering a workcell while a robot is moving,
the first question that must be answered when performing a risk assessment is determining the likely
severity of injury if a robot strikes a person. If the robot will not injure a person in the event of a collision,
and there is no other equipment in the workcell that can injure a person, then a person may be allowed to
enter the workcell while the robot is moving.
Summary of Contents for PF3400
Page 8: ......
Page 32: ...PreciseFlex_Robot 24 Appendix B TUV Verification of PF400 Collision Forces...
Page 33: ...Introduction to the Hardware 25...
Page 34: ...PreciseFlex_Robot 26...
Page 35: ...Introduction to the Hardware 27...
Page 37: ...Introduction to the Hardware 29 Appendix C Table A2 from ISO TS 15066 2016...
Page 38: ...PreciseFlex_Robot 30 Table A2 Continued...
Page 41: ...Introduction to the Hardware 33 PF400 500gm Safety Circuits PF3400 3kg Safety Circuits...
Page 45: ...Installation Information 37...
Page 46: ...PreciseFlex_Robot 38...
Page 47: ...Installation Information 39...
Page 48: ...PreciseFlex_Robot 40...
Page 54: ...PreciseFlex_Robot 46 Schematic System Overview...
Page 55: ...Hardware Reference 47 Schematic FFC Boards Revision B PF400...
Page 56: ...PreciseFlex_Robot 48...
Page 57: ...Hardware Reference 49 Schematic FFC Boards Revision C PF400...
Page 58: ...PreciseFlex_Robot 50 Schematic FFC Boards 3kg PF400...
Page 59: ...Hardware Reference 51...
Page 60: ...PreciseFlex_Robot 52 Schematic Safety System Overview PF400 CAT3...
Page 61: ...Hardware Reference 53...
Page 62: ...PreciseFlex_Robot 54 Controller Power Amplifier Connectors Control Board Connectors...
Page 63: ...Hardware Reference 55 Gripper and Linear Axis Controller Connectors...
Page 64: ...PreciseFlex_Robot 56...
Page 65: ...Hardware Reference 57...
Page 66: ...PreciseFlex_Robot 58 Schematic Slip Ring for 60N Gripper...
Page 67: ...Hardware Reference 59...
Page 68: ...PreciseFlex_Robot 60...
Page 69: ...Hardware Reference 61...
Page 70: ...PreciseFlex_Robot 62...
Page 71: ...Hardware Reference 63...
Page 72: ...PreciseFlex_Robot 64...
Page 73: ...Hardware Reference 65 Motor 60N Gripper...
Page 74: ...PreciseFlex_Robot 66...
Page 106: ...PreciseFlex_Robot 98 b The CALPP application takes about 1 minute to run...
Page 124: ...PreciseFlex_Robot 116 Wiring for 60N Gripper with Battery Pigtail Wiring for Pneumatic Gripper...
Page 125: ...117 Wiring for Vacuum Gripper Wiring for Vacuum Pallet Gripper...