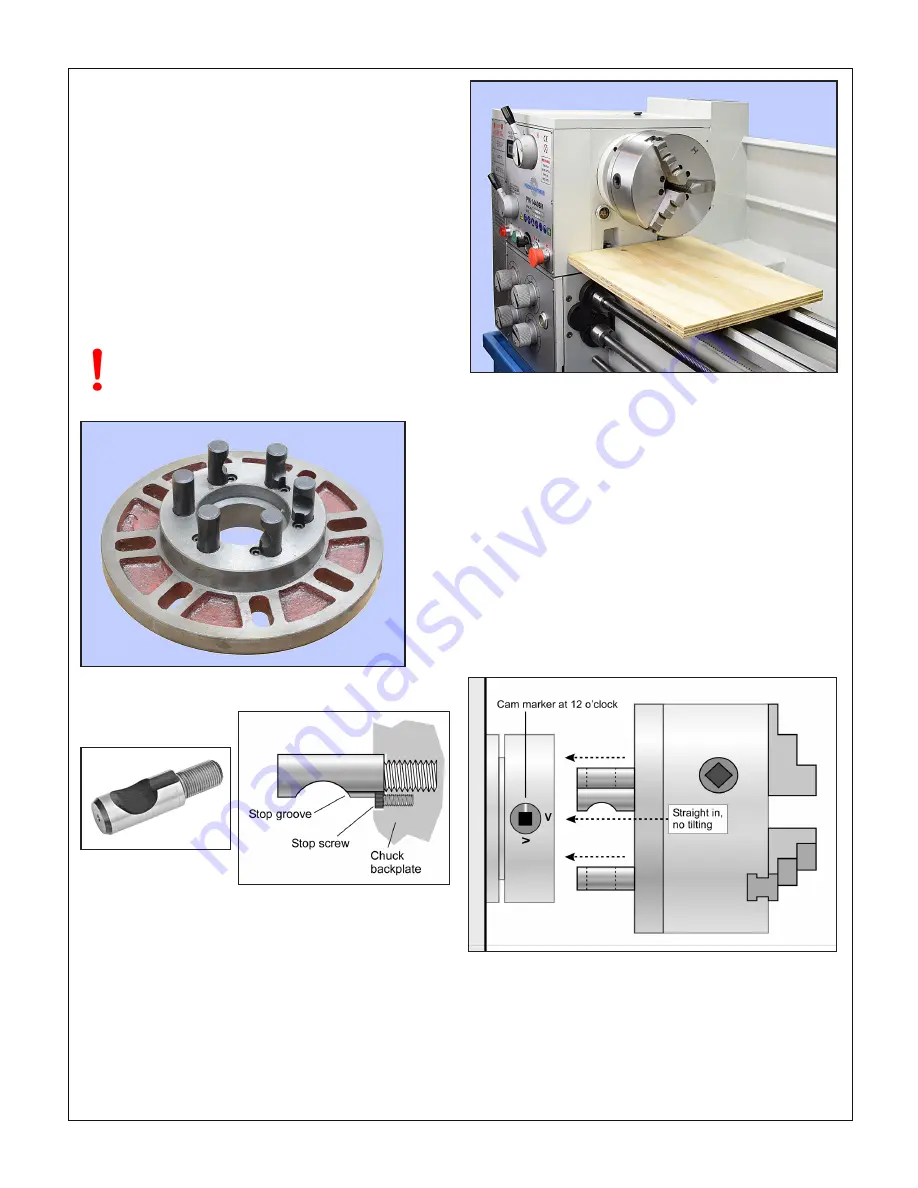
17
PM-1440BV v3 2020-10
Copyright © 2020 Quality Machine Tools, LLC
CHUCKS & FACEPLATE
The spindle nose on the PM-1440BV accepts D1-5 Camlock
chucks, faceplates and other work holding devices.
A D1-5 chuck or faceplate is held by six threaded studs, each
with a D-shape crosscut to engage a corresponding cam in the
spindle nose, Figures 3-21, 3-22. The function of the cams is
to pull the chuck backplate inward to locate its internal taper
firmly on the spindle nose.
Alongside each stud is a stop screw, the head of which fits
closely in a groove at the threaded end of the stud. The func-
tion of the stop screw is not to clamp the stud in place, but
instead to prevent it from being unscrewed when the chuck is
out on the bench.
TO INSTALL A CHUCK
Disconnect the 220V supply from the lathe!
D1-5 chucks and faceplates are heavy, some more than 30
lb. They will cause serious damage if allowed to fall. Even if a
chuck is light enough to be supported by one hand, the lathe
bed should be protected by a wood scrap, as Figure 3-23.
Some users add packing pieces, even custom-made cradles,
to assist “straight line” installation and removal.
All stop screws must be present & fully tightened!
Camlock action can jam any stud lacking a stop
screw — a serious problem.
Figure 3-21
D1-5 faceplate
Figure 3-22
Camlock stud
Before installing make certain that the mating surfaces of the
chuck/faceplate and spindle are
free of grit and chips
.
The cams on the spindle are turned with a square-tip wrench
similar to the chuck key (may be same tool in some cases).
Recommended procedure:
1. Select the high speed range
H
to allow easier hand rotation
of the spindle.
2. Turn the spindle by hand, checking that all six cam markers
are at 12 o’clock.
3. While
supporting its full weight
, install the chuck without
tilting, see Figure 3-24, then gently turn each of the cams
clockwise
— snug, firm, but not locked in this first pass.
Figure 3-23
Protect the lathe bed
4. Check that each of the cam markers lies between 3 and
6 o’clock, between the two Vees stamped on the spindle,
Figure 3-25.
5. If any cam marker is
not
within the Vees, first be sure
that there is
no gap
between chuck backplate and spin-
dle flange. Also, remove the chuck to inspect the studs —
Figure 3-24
Installing a Camlock chuck