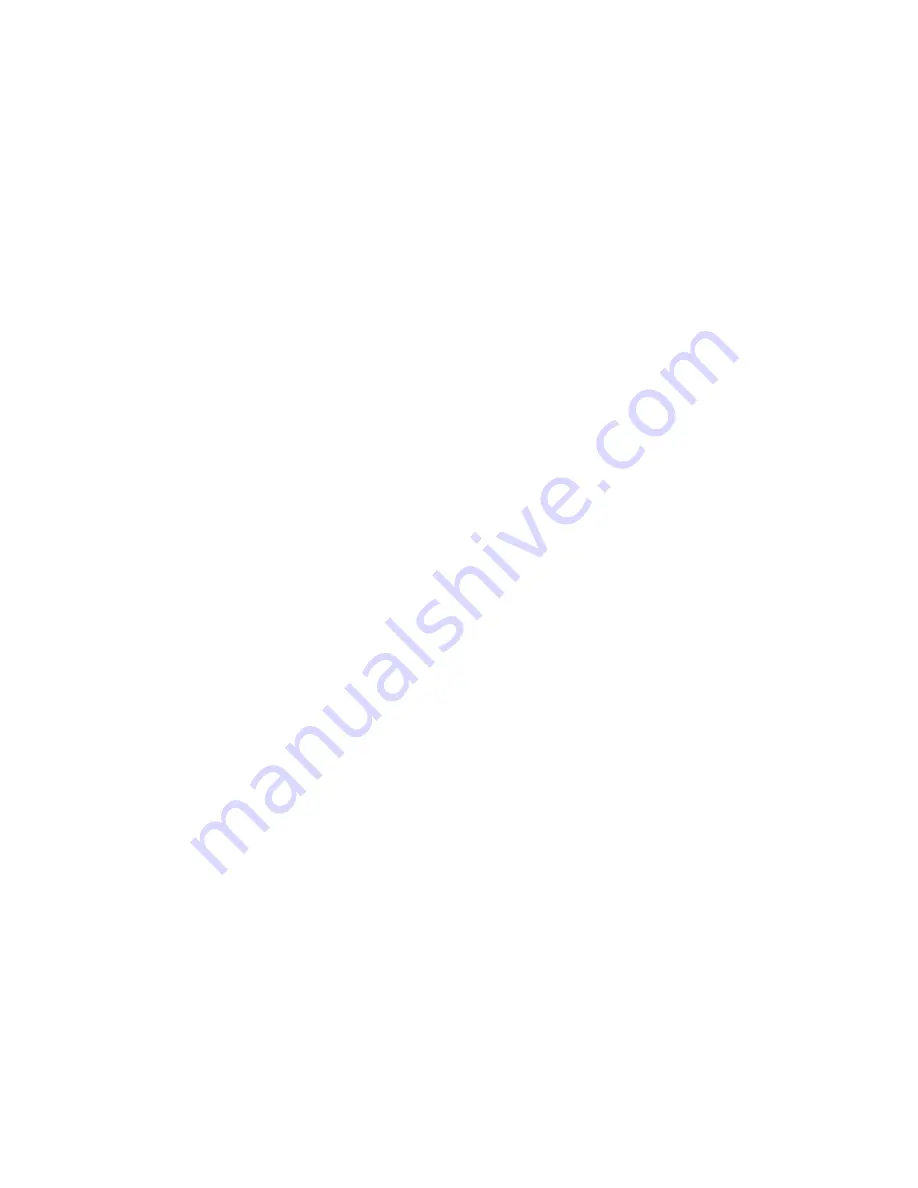
C932i, C946i Treadmill
Page 32
Procedure 5.5 - Troubleshooting the 3 Phase A.C. Drive Motor
System
Circuit Description
The power control module converts single phase 120Vac or 240Vac into three phase variable
frequency current for the A.C. drive motor. The motor speed is controlled by controlling the
frequency of the drive motor current.
1.
When taking voltage readings of the A.C. drive motor current, the readings will not be
accurate because of the frequencies being used. However, they are indicative of the
presence of drive motor voltage and relative frequency changes.
2.
If the symptoms are the drive motor starts when you force the running belt to move and once
running the drive motor runs “rough”, skip to step 10. If the drive motor will not start continue
with step 3.
3.
If the drive motor does not start, the power control module will only apply voltage for a
couple of seconds before it shuts down. Therefore the voltage readings in the following step
must be taken within the first couple of seconds after the treadmill is instructed to start the
running belt.
4.
Connect an A.C. voltmeter between terminals 4 & 5 of the OUTPUT connector on the power
control module. See Diagrams 5.3 and 5.4. Set the treadmill’s on/off switch in the “on”
position. Press the QUICK START key. If the power control module is supplying output, you
will momentarily read approximately 55 Vac. Set the treadmill’s on/off switch in the “off”
position.
5.
Repeat the procedure in step 4 between terminals 4 & 6 of the OUTPUT connector on the
power control module.
6.
Repeat the procedure in step 4 between terminals 5 & 6 of the OUTPUT connector on the
power control module.
7.
If one or more of voltage readings in steps 4 through 6 are not present, replace the power
control module. If the voltage readings in steps 4 through 6 are present, continue with step
8.
8.
Set the treadmill’s on/off switch in the “off” position. Disconnect the drive motor connector
from the OUTPUT connector on the power control module. With an ohmmeter, measure
between terminals 4 & 5, 4 & 6 and 5 & 6 of the drive motor connector. Each reading should
be approximately 2.5
Ω.
If any of the readings are significantly high or open, replace the
drive motor.
9.
If you have performed all of the procedures above and have been unable to correct the
problem, call Precor customer service.