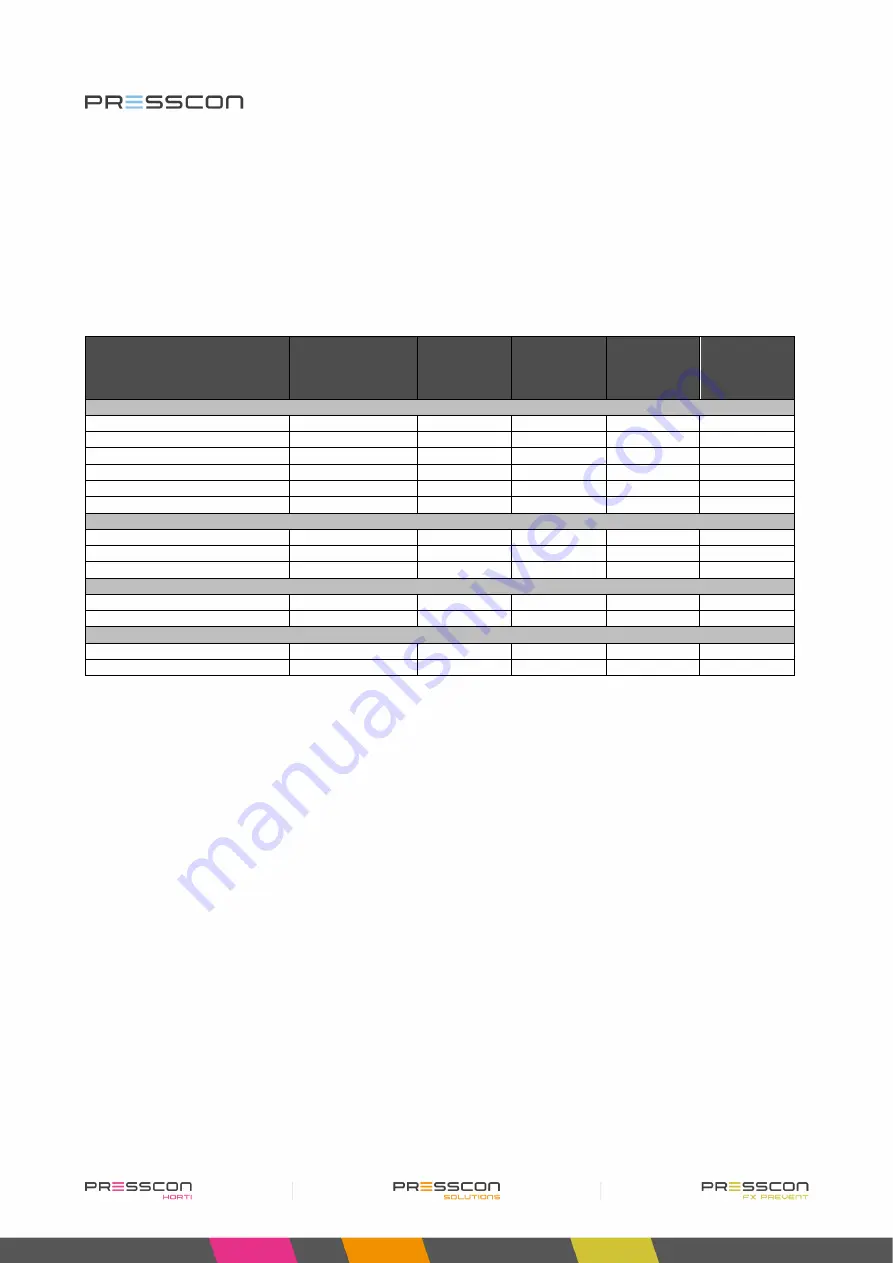
63
8
Maintenance and service
8.1 Expansion system maintenance
To make sure that the VERNIT or HORNIT expansion system continues to work well, the owner must provide the system
with its essential maintenance. A part of the maintenance, the weekly checks, are usually done by the owner or its
technical personnel. Other annual checks should be performed by a service engineer.
Activity
To be done by
Weekly
Each year or
every 2.000
hours
Every 2
years or
every 4.000
hours
Every 2
years.
Nitrogen generator
Visual inspection
Owner
X
Tightening PSA spindles
Service engineer
X
Clean dirt catcher
Service engineer
X
Check compressed air filters
Service engineer
X
Check output flow and purity
Service engineer
X
Replace compressed air filters
Service engineer
X
Sensors
Check water level
Service engineer
X
Check pressure measurement
Service engineer
X
Check sensor covers
Service engineer
X
Vacuum- overpressure safety valve (VERNIT systems)
Check safety valve(s)
Service engineer
X
Revision safety valve
Service engineer
X
Vacuum safety valve (HORNIT systems)
Check safety valve(s)
Service engineer
X
Revision safety valve
Mechanic/Factory*
X
*The revision of the vacuum safety valve for HORNIT systems should be performed at the factory of PRESSCON. The
used safety valve can be exchanged directly with a revised safety valve. Replacing the vacuum safety valve on the
horizontal buffer tank should be performed by an approved installer who can safely relief the pressure from the tank and
the safety valve.
8.2 Compressor maintenance
Although the expansion system is generally provided with a dedicated compressor, the maintenance instructions are
different for each type and brand of machine. The maintenance instructions of the compressor are described in the user
manual that is delivered as a separate document along with the compressor.
9 Warranty
PRESSCON provides a warranty of 1 year on the components of the expansion system, assuming that the following
conditions are met:
•
The equipment has been installed by PRESSCON or under direct or indirect supervision of PRESSCON.
•
The equipment is undamaged and unprocessed and not defective due to improper use.
•
The equipment is not defective by inadequate maintenance or other proceedings.
•
The equipment is not defective or non-speech hit by negligence, accident or whatsoever.
The warranty includes checking, repair or replacement if defective from proven equipment. Faulty equipment, which has
been replaced shall become property of PRESSCON.
Summary of Contents for HORNIT N2
Page 2: ...2...