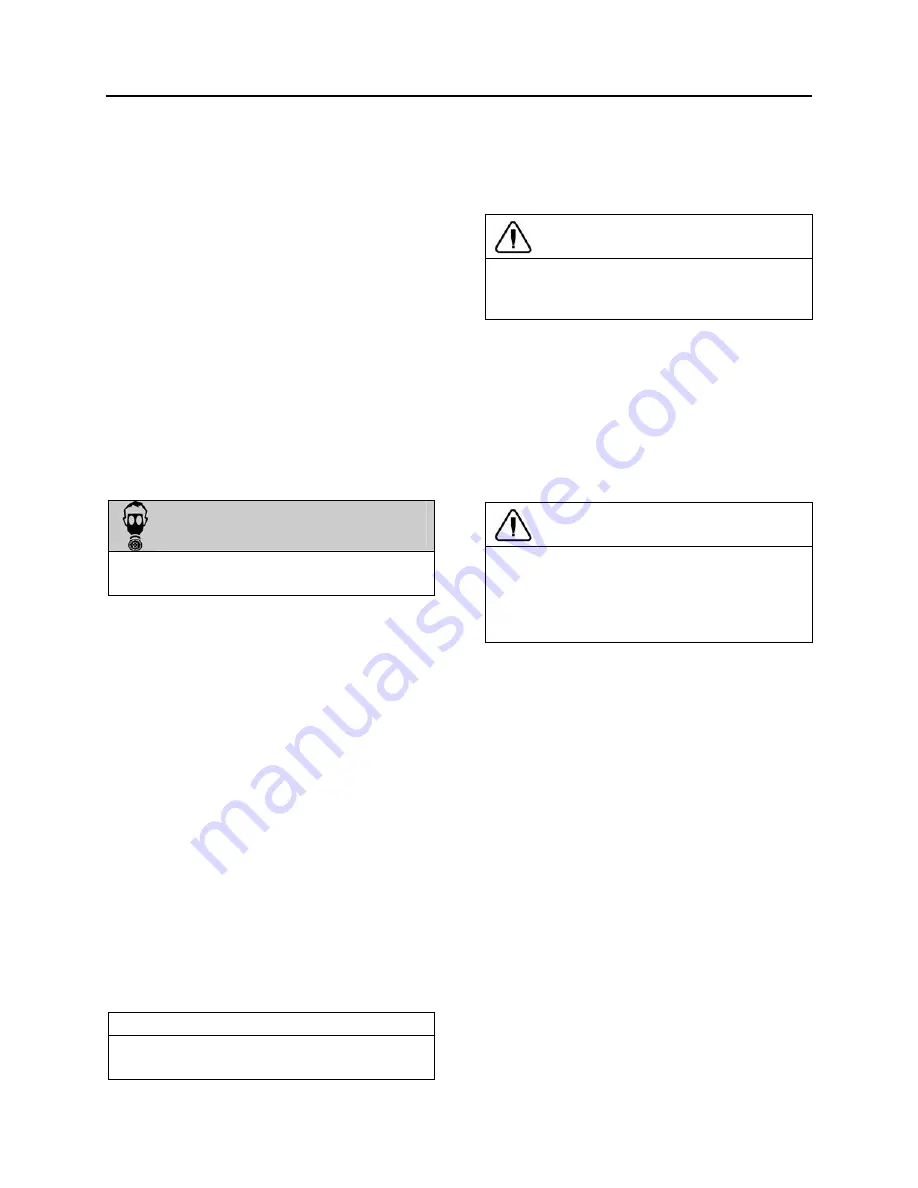
Section 18: BODY
PA1564
13
4. COMMON FIBERGLASS REPAIR
PROCEDURE
All repairs to fiberglass parts consist of filling the
damaged area with fiberglass cloth and resin or
strand fiberglass and resin. The repair is allowed
to harden, and then finishing operations may be
performed. Use of the various materials is
determined by the type of repair to be made.
Large holes, torn sections and separate joints
require the adhesive qualities of the resin and
the reinforcing qualities of the fiberglass. Small
dents, scratches or pits can be repaired using
resin and strand fiberglass and filler mixed into
paste. Instructions for either mix are explained
under their respective headings in this section.
For best results when making repairs,
temperature should be between 70 and 75
o
F
(21-24
o
C). Some people experience a skin
reaction to resins. In such cases, wipe resin off
with denatured alcohol or a good thinner. Use of
protective hand cream is recommended.
WARNING
Always wear a respirator and goggles when
grinding or sanding.
Extreme care must be taken if the sander is
electrically operated, as dust from some resins
is combustible when subjected to sparks or
open flames. The proper tool for sanding resin is
a low speed, air driven disc sander with a water
attachment or a dry sander having a vacuum
bag. Either will eliminate flying glass and resin
dust.
The following additional tools and materials will
assist in making repairs: hacksaw blade,
assorted files, emery paper or cloth (150 or
finer), scissors or tin snips, wax paper or
cellophane sheets, a 3" (75 mm) paint roller,
paint brush, putty knife, acetone and one or
more heat lamps.
4.1
REPAIR USING FIBERGLASS CLOTH
Where necessary, sand paint away around
damaged area and scrape away undercoating, if
any, and wipe clean with solvent. Grind or file
the damaged area to form a "V" at the broken or
cracked portion. Sides of "V" should have a
shallow pitch for maximum bonding area.
NOTE
Roughening the surface improves adhesion of
resin.
If part is warped from original shape, use
clamping equipment to straighten the surface.
Preheat area to be repaired with one or two heat
lamps placed 18 to 24 inches (450-610 mm)
from repair.
CAUTION
Temperature should not exceed 140
o
F (60
o
C) during 30 minutes in order to avoid
distortion.
Cut fiberglass cloth with scissors or tin snips, 1
to 3 inches (25-75 mm) larger than area to be
repaired. Build area to desired height.
Mix resin and hardener following instructions on
their containers. Saturate layers of fiberglass
with mixture and place laminates over damaged
area. Smooth out wrinkles and make sure
general contour of area is maintained. Bubbles
and wrinkles can be eliminated with a roller.
CAUTION
The pot life of the mix is approximately 15
minutes. Any accidental contamination to the
skin, clothing, tools, etc. must be removed
within this period. Use acetone to remove
uncured resin.
Heat resin material again by placing heat lamps
18 to 24 inches (450-610 mm) from repaired
area. Allow 12 to 15 minutes for repair to cure.
After repair is cured, grind, file or sand to
contour. Files other than body files may be more
suitable. Featheredge and finish sanding.
If small pits or irregularities appear after making
repair, correct by using a liberal amount of
chopped strand or filler mixed with resin to form
a paste. Refer to heading
"Repair using
Fiberglass Paste"
in this section.
4.2
REPAIR USING FIBERGLASS PASTE
Fiberglass paste is used for repairing small
dents, scratches, and pits. Paste is made by
mixing resin, hardener and fiberglass strand or
filler to the consistency of putty. Where it may be
necessary, sand paint away around damaged
area. On underside of coach, scrape away
undercoating from damaged area, and wipe
clean with solvent.
Preheat the area to be repaired using heat
lamps. Mix desired quantities of resin and
hardener according to manufacturer's
Summary of Contents for LE MIRAGE XLII BUS SHELLS
Page 1: ...COACH MANUFACTURER MAINTENANCE MANUAL LE MIRAGE XLII BUS SHELLS PA1564 1ST EDITION...
Page 12: ...Section 00 GENERAL INFORMATION 10 PA1564 FIGURE 13 METRIC US STANDARD CONVERSION TABLE 00005...
Page 13: ...Section 00 GENERAL INFORMATION PA1564 11 FIGURE 14 CONVERSION CHART 00006...
Page 14: ......
Page 30: ......
Page 63: ...SECTION 01 ENGINE PA1564 33 FIGURE 13 POWER PLANT CRADLE INSTALLATION 01140...
Page 108: ......
Page 160: ......
Page 210: ......
Page 229: ...FAULT CODE MANUAL Created on 00 04 25 15 30 1 FAULT CODE MANUAL B7L B7TL B12...
Page 254: ......
Page 281: ......
Page 282: ......
Page 283: ......
Page 284: ......
Page 285: ......
Page 286: ......
Page 287: ......
Page 288: ......
Page 289: ......
Page 290: ......
Page 291: ......
Page 292: ......
Page 309: ......
Page 379: ...Section 12 BRAKE AND AIR SYSTEM PA1564 21 FIGURE 38 AIR OPERATED BRAKING SYSTEM WE...
Page 380: ...Section 12 BRAKE AND AIR SYSTEM PA1564 22 FIGURE 39 AIR OPERATED BRAKING SYSTEM W5...
Page 387: ...Section 12 BRAKE AND AIR SYSTEM PA1564 29 FIGURE 46 ABS 6S 5M CONFIGURATION...
Page 418: ...16 BW2158 Honeywell Commercial Vehicle Systems Company 4 2001 Printed in USA...
Page 422: ......
Page 430: ......
Page 438: ......
Page 445: ......
Page 458: ......
Page 534: ......
Page 540: ......
Page 543: ......
Page 660: ......
Page 661: ......
Page 662: ......
Page 663: ......
Page 664: ......
Page 665: ......
Page 666: ......
Page 667: ......
Page 668: ......
Page 669: ......
Page 670: ......
Page 671: ......
Page 672: ......
Page 673: ......
Page 674: ......
Page 675: ......
Page 676: ......
Page 677: ......
Page 678: ......
Page 679: ......
Page 680: ......
Page 681: ......
Page 682: ......
Page 683: ......
Page 684: ......
Page 685: ......
Page 686: ......
Page 687: ......
Page 688: ......
Page 689: ......
Page 690: ......
Page 691: ......
Page 692: ......
Page 693: ......
Page 694: ......
Page 695: ......
Page 696: ......
Page 697: ......
Page 698: ......
Page 699: ......
Page 700: ......
Page 701: ......
Page 702: ......
Page 703: ......
Page 704: ......
Page 705: ......
Page 706: ......
Page 707: ......
Page 708: ......
Page 709: ......
Page 710: ......
Page 711: ......
Page 712: ......
Page 713: ......
Page 714: ......
Page 715: ......
Page 716: ......
Page 717: ......
Page 718: ......
Page 719: ......
Page 720: ......
Page 721: ......
Page 722: ......
Page 723: ......
Page 724: ......
Page 725: ......
Page 726: ......
Page 727: ......
Page 728: ......
Page 729: ......
Page 730: ......
Page 731: ......
Page 732: ......
Page 733: ......
Page 734: ......
Page 735: ......
Page 736: ......
Page 737: ......
Page 738: ......
Page 739: ......
Page 740: ......
Page 741: ......
Page 742: ......
Page 743: ......
Page 744: ......
Page 745: ......
Page 746: ......
Page 747: ......
Page 748: ......
Page 749: ......
Page 750: ......
Page 751: ......
Page 752: ......
Page 753: ......
Page 754: ......
Page 755: ......
Page 756: ......
Page 757: ......
Page 758: ......
Page 759: ......
Page 760: ......
Page 798: ......
Page 886: ......
Page 900: ......
Page 902: ......
Page 904: ......
Page 910: ......
Page 916: ......
Page 920: ......
Page 924: ......
Page 926: ...PROCEDURE NO SAV00044 REVISION 00 Page 2 of 2 Slide out...
Page 930: ......
Page 932: ......
Page 934: ......
Page 940: ......
Page 944: ......
Page 946: ......
Page 954: ......
Page 976: ......
Page 988: ......
Page 992: ......
Page 996: ......
Page 1032: ......
Page 1038: ......
Page 1044: ......
Page 1064: ......
Page 1086: ...Section 22 HEATING AND AIR CONDITIONING PA1564 18 FIGURE 17 DOUBLE SWEEP EVACUATION SET UP...
Page 1118: ...Section 22 HEATING AND AIR CONDITIONING PA1564 50 FIGURE 54 HEATER LINE SHUTOFF VALVES WE...
Page 1124: ......
Page 1125: ...Compressor 62 11052 Rev A WORKSHOP MANUAL for MODEL 05G TWIN PORT COMPRESSOR R...
Page 1126: ...WORKSHOP MANUAL COMPRESSOR MODEL 05G TWIN PORT...
Page 1149: ...Compressor 62 11053 Rev B SERVICE PARTS LIST for MODEL 05G TWIN PORT COMPRESSOR 1 2 3 4 5 6 R...
Page 1177: ......
Page 1178: ......
Page 1179: ...1...
Page 1180: ...2...
Page 1181: ...3...
Page 1182: ...4...
Page 1183: ...5...
Page 1184: ...6...
Page 1185: ...7...
Page 1186: ...8...
Page 1187: ...9...
Page 1188: ......
Page 1212: ......
Page 1223: ...Section 26 XLII SLIDE OUT PA1564 11...
Page 1224: ...Section 26 XLII SLIDE OUT PA1564 12 FIGURE 16 KEYLESS BUSHING INSTALLATION INSTRUCTION...