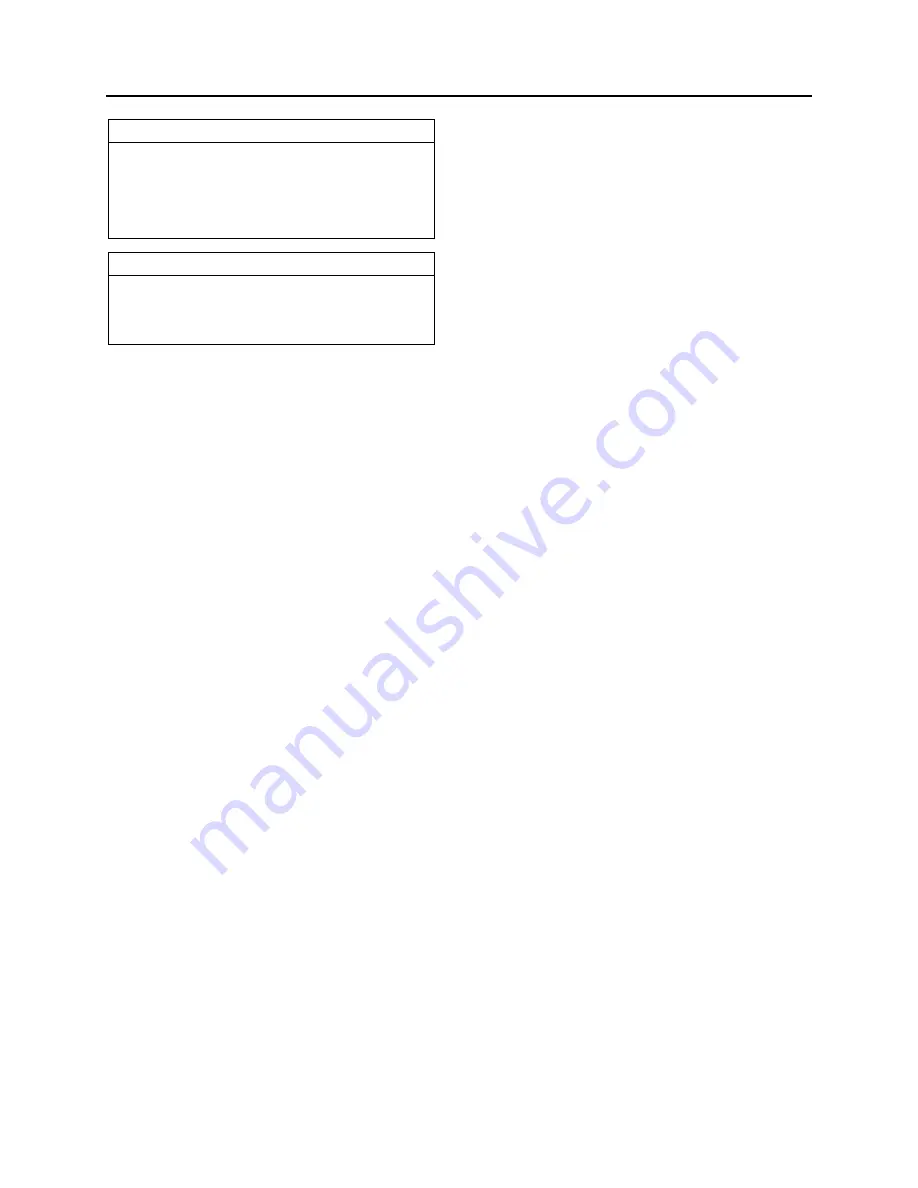
Section 13: WHEELS, HUBS & TIRES
PA1593
7
NOTE
If original bearing unit is re-fitted, and end-float
is measured at 1 mm, with hub not fully
tightened to correct torque [563-687 lb-ft (763-
931 Nm)], then the retaining clip within the unit
is damaged and a new unit must be fitted.
NOTE
For more information on front and tag axle
wheel hub, refer to “DANA SPICER Service
Manual NDS Axle Range” found in the OEM
manuals folder.
7.2 HUB BEARING REMOVAL
Stop engine and apply parking brake.
Loosen wheel nuts about one turn (do not
remove the nuts). This is not necessary if
equipped with hydraulic powered gun.
Raise the vehicle by its jacking points on the
body. See Section 18,
"Body",
under
heading
"Vehicle Jacking Points".
Unscrew wheel hex stud nuts (10) and
remove the wheel.
Unscrew hub flange hex cap screws (14).
Remove hub flange and rotor.
Unscrew hub nut and discard.
Remove bearing thrust washer.
Remove unitized hub bearing by hand or
use a puller if necessary.
7.3 HUB BEARING INSTALLATION
Clean spindle using EFX degreaser (Prevost
#685313).
Lubricate part of spindle where bearing will
be located, use Gleitmo 805 grease
(Prevost #685274).
Slide unitized hub bearing over spindle and
position using insertion tool #491115.
Clean thrust washer and hub nut using EFX
degreaser.
Install thrust washer and hub nut then
torque hub nut to [563-687 lb-ft (763-931
Nm)].
Stake the hub nut by deforming with a round
nosed chisel.
Clean hub bearing, rotor and hub flange
clamping surfaces using EFX degreaser.
Install rotor onto hub bearing.
Add some grease (25-50 ml) (Fuchs
Renolite LX PEP-2) (Prevost #685325) into
the bottom of the hub flange cap. Mount hub
flange onto rotor.
Apply some Loctite 243 blue onto cap screw
threads then secure hub flange and rotor to
unitized hub bearing using cap screws (14).
Torque to [161-197 Lb-Ft (218-267 Nm)]
(Refer to figure 3 for tightening sequence).
Mount the wheel over studs, being careful
not to damage stud threads.
Screw in the hex stud nuts (refer to Figure 2
for sequence) so that wheel will position
itself concentrically with hub. This is
important, otherwise wheel may be eccentric
with hub and will not run straight. In this
initial step, slightly tighten the nuts to
correctly position the wheel.
Tighten stud nuts progressively as shown in
Figure 2. The final tightening should be
done with a torque wrench. Tighten stud
nuts to [450 - 500 lbf-ft (610 - 680 Nm)] for
all steel wheel.
8. DRIVE AXLE WHEEL HUBS
Drive wheels use a single oil-seal assembly.
They are lubricated from the oil supply in the
differential housing. Bearings are tapered
rollers, adjustable to compensate wear. Maintain
differential oil level with general-purpose gear
lubricant (refer to Section 24
"Lubrication"
for
proper oil grade selection) to ensure adequate
oil supply to wheel bearings at all times.
8.1 BEARING ADJUSTMENT
To adjust drive wheel bearings:
1. Raise vehicle until both dual wheels can be
turned freely (approximately 6 inches from
the ground). Position jack stands under drive
axle, then lower vehicle approximately 2
inches in order to avoid entire weight of the
axle being supported by the suspension air
bellows and the shock absorber pins.
2. Remove axle shaft as indicated in
"Meritor -
Maintenance Manual No. 5"
under heading
"Single Reduction Differential Carriers"
annexed to
"Section 11"
of this manual.
Summary of Contents for X3-45 2016
Page 4: ......
Page 16: ...Section 00 GENERAL INFORMATION PA1593 12 FIGURE 12 METRIC US STANDARD CONVERSION TABLE 00005...
Page 17: ...Section 00 GENERAL INFORMATION 13 PA1593 FIGURE 13 CONVERSION CHART 00006...
Page 18: ......
Page 26: ......
Page 58: ......
Page 72: ...Section 04 EXHAUST AND AFTERTREATMENT SYSTEM PA1593 14 7 TORQUE SPECIFICATIONS...
Page 73: ...SECTION 04 EXHAUST AND AFTERTREATMENT SYSTEM PA1593 15...
Page 74: ...Section 04 EXHAUST AND AFTERTREATMENT SYSTEM PA1593 16...
Page 76: ......
Page 96: ......
Page 134: ......
Page 176: ...SECTION 06B ELECTRICAL 38 overcurrent working Circuit 306 shorted to ground...
Page 180: ......
Page 202: ......
Page 205: ...Section 09 PROPELLER SHAFT PA1593 3 FIGURE 1 PROPELLER SHAFT ASSEMBLY 09002...
Page 256: ......
Page 268: ......
Page 295: ...SECTION 16 SUSPENSION PA1593 9 2 5 TORQUE SPECIFICATIONS...
Page 296: ...Section 16 SUSPENSION PA1593 10...
Page 297: ...Section 16 SUSPENSION PA1593 11...
Page 314: ......
Page 380: ......
Page 388: ......
Page 413: ...Section 22 HEATING AND AIR CONDITIONING PA1593 15 FIGURE 18 REFRIGERANT CIRCUIT CENTRAL SYSTEM...
Page 433: ...Section 22 HEATING AND AIR CONDITIONING PA1593 35 FIGURE 36 CENTRAL HEATING SYSTEM COMPONENTS...