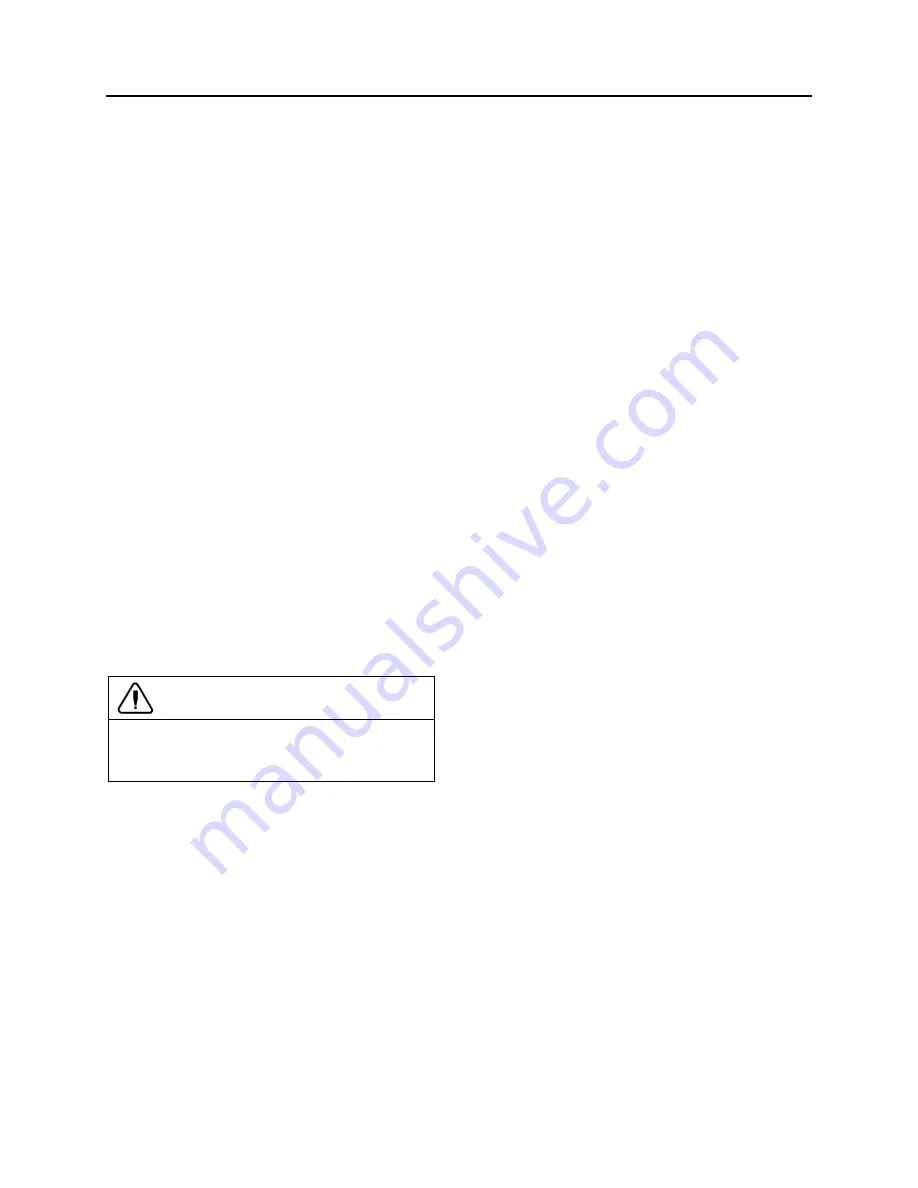
Section 22: HEATING AND AIR CONDITIONING
PA1593
19
3. Turn in the two shutoff valves 3 to 4 turns.
4. Open the lower receiver valve by turning
“out” all the way.
5. Backseat the upper receiver valve by turning
out all the way.
6. Remove the cover cap from the service
fitting in the top receiver valve.
7. Attach a charging hose to the R-134a tank.
Open the tank valve slightly permitting R-
134a to escape thus purging the hose of air.
8. Connect the charging hose to the service
fitting.
9. Open the R-134a tank valve.
10. To build up pressure in the receiver tank,
heat the receiver tank with a heating
blanket.
11. Turn in the upper receiver valve several
turns. The R-134a will now enter the
system.
12. The proper charge of R-134a is 24 lbs
(10.89 kg). When the scale indicates this
amount of charge, backseat the receiver
valve and close the R-134a tank valve.
13. Disconnect the charging hose. Replace the
cover caps.
14. The system is now ready for operation.
CAUTION
The evacuation of the system must be made
by authorized and qualified personnel only.
Refer to local laws for R-134a recuperation.
6.7 REFRIGERANT SYSTEM CLEAN-OUT
AFTER COMPRESSOR FAILURE
Although the vast majority of reciprocating
refrigerant compressors manufactured today are
extremely reliable, a small percentage do fail.
These failures usually result in minor or
extensive system contamination depending on
the severity of the failure. When an open type
compressor becomes damaged internally, this
provokes small particles of bearings, steel,
brass, copper, and aluminum and, in severe
cases, carbonized oil, which could contaminate
the system. To prevent repeated failures, the
problem which caused the failure should be
corrected, and depending upon the severity of
the failure, the system should be thoroughly
cleaned out using one of the clean-out
procedures mentioned.
6.7.1 Determining Severity of Failure
The severity of compressor failure can be
categorized as minor or major. A failure is
considered minor when the contamination is
limited to the compressor with little or no system
contamination. A major failure, or burnout,
results in extensive system contamination as
well as compressor damage. Extensive system
contamination can be determined by
withdrawing a small sample of compressor oil
and checking its color, odor and acidity. A
Virginia Chemical "TKO" one step acid test kit is
one of several compressor oil test kits that may
be used. A high acid content would indicate a
major failure or burnout. A small amount of
refrigerant gas may be discharged. A
characteristic burned odor would also indicate
severe system contamination.
6.7.2 Clean-out after Minor Compressor
Failure
1. Be sure to correct the problem which
caused the failure.
2. Change liquid line filter dryer.
3. Run the unit for 2 hours on high speed cool
only.
4. Check compressor oil level to ensure
compressor is not overcharged with oil.
Sometimes a significant amount of oil is
pumped out of the compressor to other
parts of the system when a compressor
fails. This oil will return to the replacement
compressor when it is started, causing an
overcharge of oil in the sump of the
replacement compressor. In this case, it is
important that the oil level be adjusted to
the proper level.
5. Withdraw a sample of the compressor oil and
check its color, odor, and acidity, using
instructions supplied above. If the oil is
contaminated, change the oil and filter dryer,
and repeat the procedure until the system is
clean.
6.7.3 Clean-out After Major Compressor
Failure
1. Reclaim the refrigerant into a refrigerant
bottle through a filter dryer to filter out
contaminants.
Summary of Contents for X3-45 2016
Page 4: ......
Page 16: ...Section 00 GENERAL INFORMATION PA1593 12 FIGURE 12 METRIC US STANDARD CONVERSION TABLE 00005...
Page 17: ...Section 00 GENERAL INFORMATION 13 PA1593 FIGURE 13 CONVERSION CHART 00006...
Page 18: ......
Page 26: ......
Page 58: ......
Page 72: ...Section 04 EXHAUST AND AFTERTREATMENT SYSTEM PA1593 14 7 TORQUE SPECIFICATIONS...
Page 73: ...SECTION 04 EXHAUST AND AFTERTREATMENT SYSTEM PA1593 15...
Page 74: ...Section 04 EXHAUST AND AFTERTREATMENT SYSTEM PA1593 16...
Page 76: ......
Page 96: ......
Page 134: ......
Page 176: ...SECTION 06B ELECTRICAL 38 overcurrent working Circuit 306 shorted to ground...
Page 180: ......
Page 202: ......
Page 205: ...Section 09 PROPELLER SHAFT PA1593 3 FIGURE 1 PROPELLER SHAFT ASSEMBLY 09002...
Page 256: ......
Page 268: ......
Page 295: ...SECTION 16 SUSPENSION PA1593 9 2 5 TORQUE SPECIFICATIONS...
Page 296: ...Section 16 SUSPENSION PA1593 10...
Page 297: ...Section 16 SUSPENSION PA1593 11...
Page 314: ......
Page 380: ......
Page 388: ......
Page 413: ...Section 22 HEATING AND AIR CONDITIONING PA1593 15 FIGURE 18 REFRIGERANT CIRCUIT CENTRAL SYSTEM...
Page 433: ...Section 22 HEATING AND AIR CONDITIONING PA1593 35 FIGURE 36 CENTRAL HEATING SYSTEM COMPONENTS...