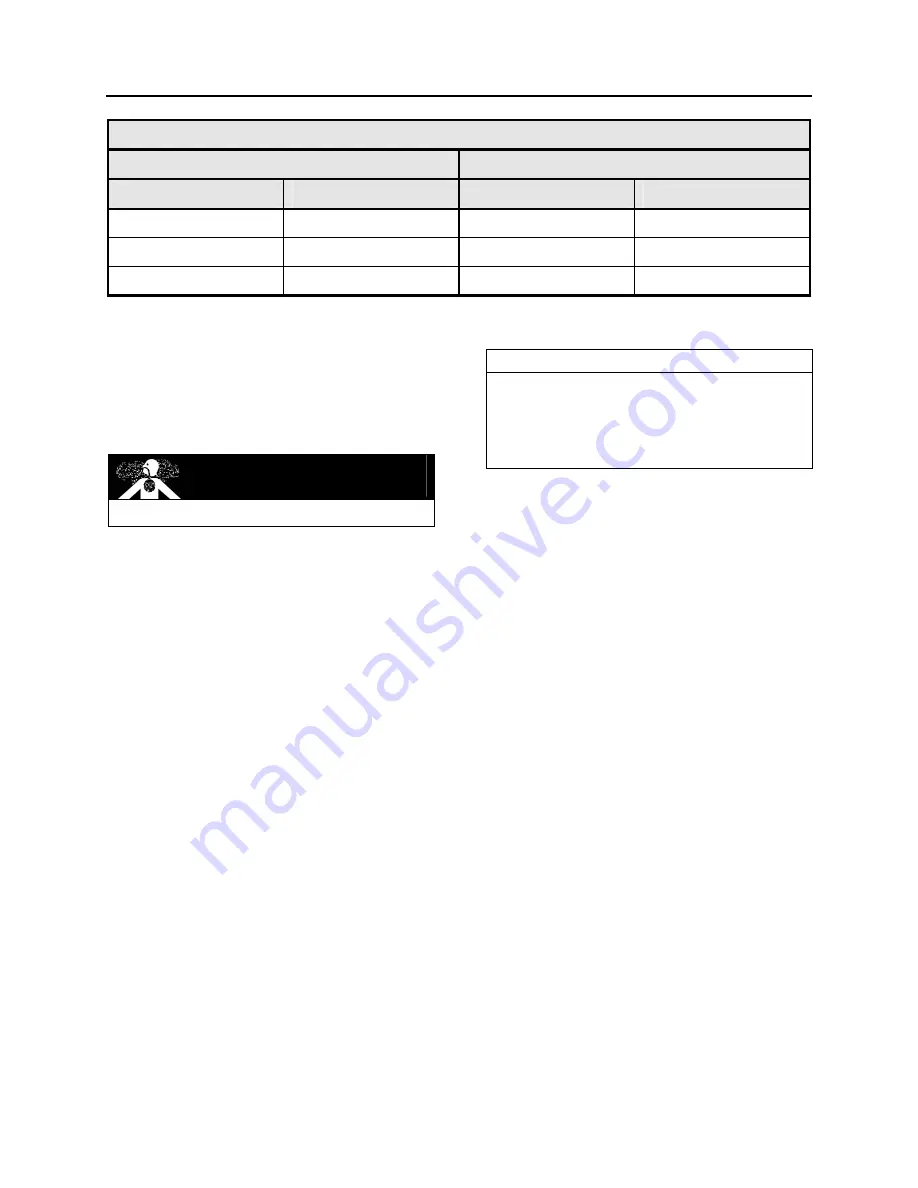
Section 22: HEATING AND AIR CONDITIONING
PA1593
34
VAPOR-PRESSURE
TEMPERATURE
PRESSURE
°F °C psi kPa
190 87.8 433.6
2989.7
200 93.3 485.0
3344.1
210 98.9 540.3
3725.4
7.12 LEAK TESTING
Some methods such as nitrogen pressure, soap
and electronic sniffer can be used for leak
testing. However, the most common method
used is a "Halide" torch consisting of an
acetylene tank, a burner and a suction test
hose. Proceed as follows:
DANGER
Do not inhale fumes from leak detector.
The flow of acetylene to the burner causes
suction in the test line. Any gas refrigerant
present will be drawn through the hose and into
the burner where it decomposes into free acids.
These acids come in contact with the hot copper
reaction plate in the burner, causing color
reaction in the flame. A small concentration is
indicated by a green tint and a large
concentration by an intense blue. Do not
confuse this change in color with the change
caused by shutting off the air supply through the
hose by holding the end too close to an object.
The procedure for testing is:
1. Adjust flame so that the top of the cone is
approximately level or within one-half inch
above the plate.
2. Probe end of suction test tube around all
joints, valves, etc. When a leak has been
found at a soldered joint, this section of the
system must be pumped down. Do not
solder as pressure will force hot solder out.
If the system is empty, it is more
economical to put in just enough R-134a to
produce about 15 psi (103 kPa). The
pressure can be raised to about 150 psi
(1034 kPa) with dry nitrogen.
NOTE
This gas is put into the suction and discharge
shutoff valves at the compressor. The receiver
valves must be opened. If no leaks are found,
dump this mixture, evacuate the system and
fill with refrigerant.
Summary of Contents for X3-45 2016
Page 4: ......
Page 16: ...Section 00 GENERAL INFORMATION PA1593 12 FIGURE 12 METRIC US STANDARD CONVERSION TABLE 00005...
Page 17: ...Section 00 GENERAL INFORMATION 13 PA1593 FIGURE 13 CONVERSION CHART 00006...
Page 18: ......
Page 26: ......
Page 58: ......
Page 72: ...Section 04 EXHAUST AND AFTERTREATMENT SYSTEM PA1593 14 7 TORQUE SPECIFICATIONS...
Page 73: ...SECTION 04 EXHAUST AND AFTERTREATMENT SYSTEM PA1593 15...
Page 74: ...Section 04 EXHAUST AND AFTERTREATMENT SYSTEM PA1593 16...
Page 76: ......
Page 96: ......
Page 134: ......
Page 176: ...SECTION 06B ELECTRICAL 38 overcurrent working Circuit 306 shorted to ground...
Page 180: ......
Page 202: ......
Page 205: ...Section 09 PROPELLER SHAFT PA1593 3 FIGURE 1 PROPELLER SHAFT ASSEMBLY 09002...
Page 256: ......
Page 268: ......
Page 295: ...SECTION 16 SUSPENSION PA1593 9 2 5 TORQUE SPECIFICATIONS...
Page 296: ...Section 16 SUSPENSION PA1593 10...
Page 297: ...Section 16 SUSPENSION PA1593 11...
Page 314: ......
Page 380: ......
Page 388: ......
Page 413: ...Section 22 HEATING AND AIR CONDITIONING PA1593 15 FIGURE 18 REFRIGERANT CIRCUIT CENTRAL SYSTEM...
Page 433: ...Section 22 HEATING AND AIR CONDITIONING PA1593 35 FIGURE 36 CENTRAL HEATING SYSTEM COMPONENTS...