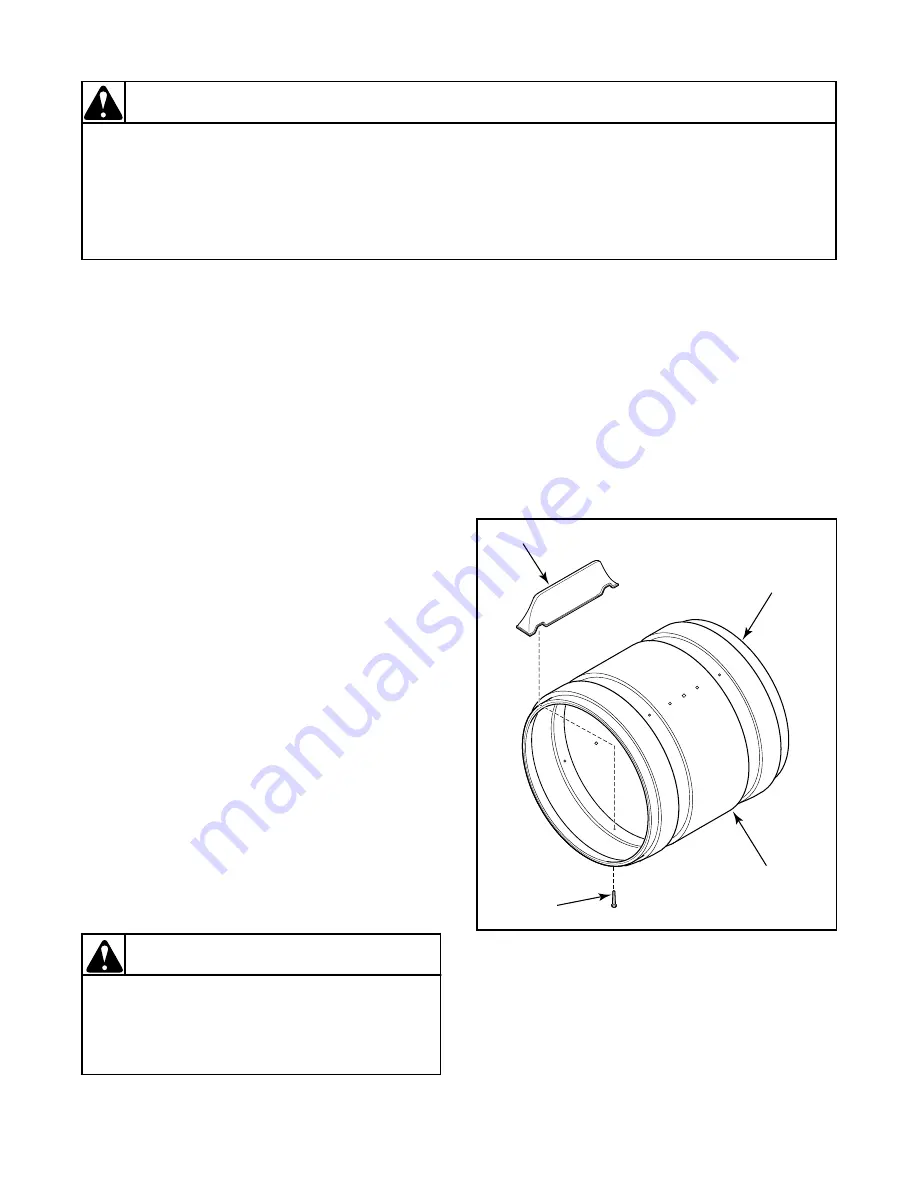
70
516514
Section 5 Service Procedures
To reduce the risk of electric shock, fire, explosion, serious injury or death:
• Disconnect electric power to the dryer(s) before servicing.
• Close gas shut-off valve to gas dryer(s) before servicing.
• Never start the dryer(s) with any guards/panels removed.
• Whenever ground wires are removed during servicing, these ground wires must be
reconnected to ensure that the dryer is properly grounded.
W001R1
WARNING
51. CYLINDER ASSEMBLY
a. While supporting the access panel, remove two
screws from bottom edge of access panel. Refer
to Figure 7.
b. Gently lower the access panel to disengage
locators from bottom edge of front panel. Refer
to Figure 37.
c. Remove two screws holding bottom tabs on
front panel to dryer side panels. Refer to
Figure 37. Swing bottom of front panel away
from dryer far enough to disengage hold-down
clips and locators from cabinet top.
d. Disconnect wires from door switch. Refer to
NOTE: Refer to wiring diagram when rewiring
switch.
e. Disengage belt from motor and idler pulleys.
Refer to Figure 47.
NOTE: When reinstalling belt, be sure belt is
properly installed on motor and idler pulleys, and is
on the correct side of the idler lever. Refer to
Figure 47. Belt must be positioned around center
section of cylinder approximately three inches
ahead of rear rib on cylinder, with the ribbed
surface of the belt against the cylinder. Refer to
Figure 57. After installing belt, manually rotate
cylinder counterclockwise to check that belt is
properly aligned.
f. Remove four screws holding bulkhead to front
flange of cabinet. Then lift complete bulkhead
assembly out of slots in cabinet. Refer to
Figure 53.
IMPORTANT: When reassembling, be sure seal on
exhaust fan cover makes airtight seal on flange of
duct. Refer to Figure 44. If the seal is installed
improperly, the airflow through the exhaust system
will be restricted which can adversely affect dryer
performance.
g. Remove two cabinet top hold-down screws.
Refer to Figure 53.
h. Carefully remove cylinder out through front of
dryer.
i. Baffles – Remove screws holding baffles to
cylinder. Refer to Figure 57.
To reduce the risk of serious injury or death
by carbon monoxide and other gases in gas
dryers, carefully read and follow all
instructions given in this section.
W005
WARNING
Figure 57
BAFFLE
CYLINDER
ASSEMBLY
(Includes
three baffles)
SCREW
REAR
RIB
D414SE1A
Summary of Contents for DAM 9
Page 1: ...DAM 9 SERVICE MANUAL INDUSTRIAL DRYERS PUBLICATION DATE 02 01 516514 ...
Page 2: ......
Page 127: ......
Page 128: ......