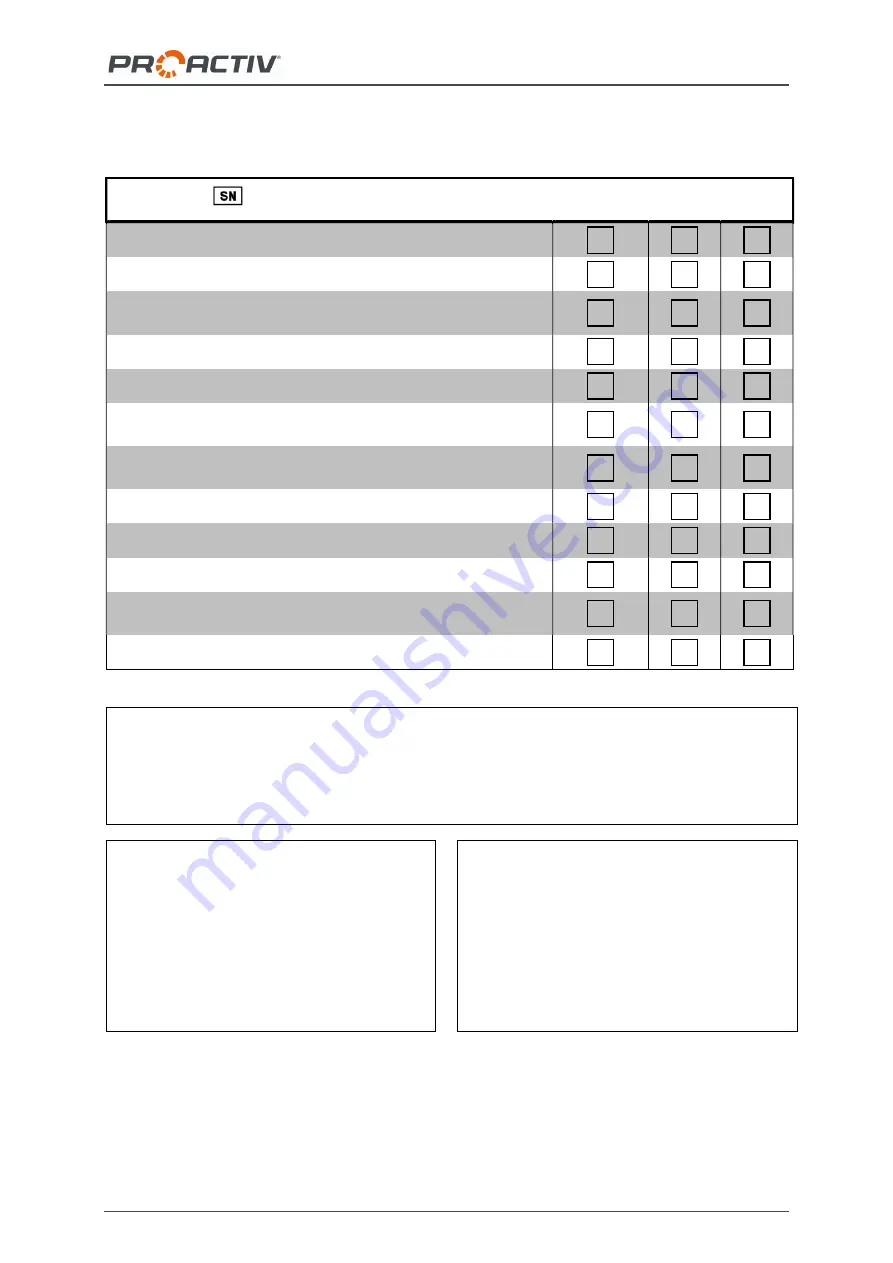
Usage instructions for SPEEDY F1
41
Subsequent inspection:
One year later after the last inspection or earlier following heavy
use
Serial number:
___________________
OK /
carried out
not OK
resolved
Check that all screws/fastening elements are firmly seated
Clean and oil/grease all pivot points, quick release axles and bearings
Carry out a visual inspection of the frame and attachments for crack
formations, deformations, etc.
Functional/safety check of anti-tipping supports
Functional/safety check of the seat and back system
Carry out a functional/safety check of the drive wheels and, if required,
replace the tyres on the product
Check that the wheel tracking and drive wheel bushing are firmly seated
(tightening torque 70 Nm)
Functional/safety check of caster wheels
Checking the caster wheel axle is firmly seated (tightening torque 7 Nm)
Functional/safety check of footrests
Checking and replacing, if necessary, the plastic protective hose on the
ram bar
Test drive/functional test
OK / carried out = OK | not OK = not OK | resolved = the fault was corrected
Comments:
Rehabilitation specialist dealer:
______________________________________
______________________________________
First name and last name of contact:
______________________________________
Stamp:
_________________________________________
Date/signature
To maintain the warranty rights, the completed inspection list must be sent by e-mail or post to PRO ACTIV within four weeks of
the inspection.